主要缺陷检测的核心项目与技术手段
在现代工业生产与质量管理体系中,缺陷检测已成为确保产品合格率的核心环节。通过系统化的检测项目设计,企业能够精准识别材料缺陷、工艺偏差和装配异常等问题。典型的缺陷检测体系包含物理特性检测、几何尺寸测量、表面完整性分析、内部结构探伤四大模块,每个模块均通过前沿技术手段实现毫米级甚至纳米级的检测精度。
1. 表面缺陷检测
基于机器视觉的自动化检测系统可识别划痕、凹陷、氧化斑等表面异常,采用高分辨率工业相机(最高可达5μm/pixel)结合深度学习算法,实现实时检测速度超过2000件/分钟。系统通过多光谱成像技术区分油污、锈蚀等不同缺陷类型,检测精度较传统人工目检提升90%以上。
2. 内部结构探伤
采用工业CT(计算机断层扫描)技术可实现非破坏性三维检测,分辨率达到0.5μm级别。X射线衍射仪能识别材料内部晶格缺陷,超声波探伤系统可检测深度达300mm的工件内部裂纹。最新的相控阵超声检测技术可对复杂几何部件进行多角度扫描,缺陷检出率达99.7%。
3. 材料性能检测
通过电子显微镜(SEM/EDX)进行微观组织分析,配合拉伸试验机、硬度计等设备验证材料力学性能。红外热像仪可检测材料导热均匀性,电磁涡流检测系统能发现导电材料中的隐性缺陷。针对复合材料,采用太赫兹成像技术可穿透非金属层检测内部脱粘缺陷。
4. 装配完整性验证
基于3D视觉的装配检测系统通过点云比对技术,可在0.3秒内完成复杂组件的装配精度验证。智能扭矩传感器实时监控螺栓预紧力,力反馈机械臂可检测插接件配合度。针对微电子元件,采用X射线实时成像技术可检测BGA焊点质量,缺陷识别精度达到10μm。
智能化检测系统发展趋势
当前缺陷检测正朝着多模态数据融合方向发展,通过整合视觉、声学、热力学等多维度检测数据,结合数字孪生技术构建预测性质量模型。基于5G网络的分布式检测系统可实现跨工厂数据共享,AI算法通过持续学习将检测误报率降低至0.02%以下,推动制造业进入零缺陷生产新阶段。
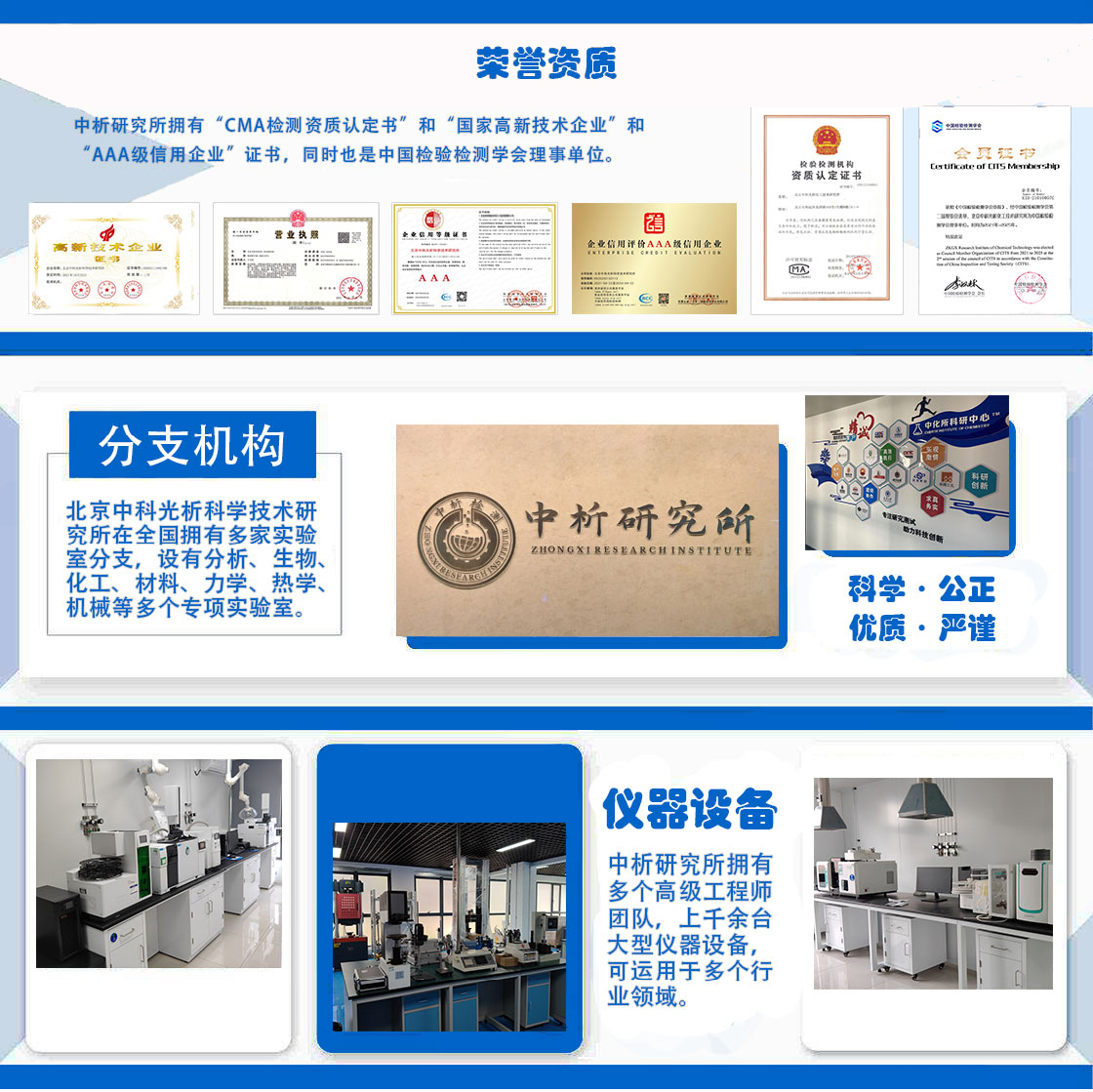
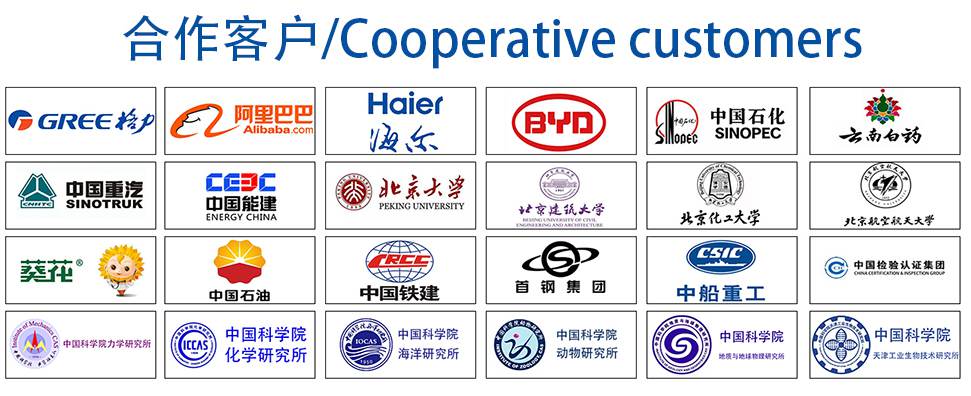