浸泡毛刷式玻璃瓶清洗机检测的重要性
在现代食品、药品及化工行业中,浸泡毛刷式玻璃瓶清洗机作为核心设备之一,承担着清除容器内外壁残留物、油脂及微生物的重要任务。其清洗效果直接影响产品安全性、包装质量及生产线效率。由于该设备涉及高温浸泡、机械刷洗、高压喷淋等多道工艺,长期使用易出现毛刷磨损、喷嘴堵塞、温控失效等问题,因此定期开展系统性检测是保障设备性能、降低质量风险的关键措施。通过科学的检测手段,不仅能验证清洗机是否符合GMP规范或行业标准,还能预判设备损耗趋势,延长使用寿命。
核心检测项目及实施要点
1. 清洗效果验证检测
采用标准污染样本(如人工涂抹油性物质或荧光示踪剂)模拟实际污染情况,通过目视检查、ATP生物荧光检测仪、残留物分析仪等设备,量化检测玻璃瓶内外的清洁度。重点评估以下指标:可见异物残留量≤0.5mm²/cm²、微生物残留量<1CFU/cm²、化学残留符合GB 14934标准。需在不同清洗周期(满载/半载)下重复测试,确保清洗稳定性。
2. 毛刷系统性能检测
使用游标卡尺测量毛刷直径损耗率(正常值<15%),通过扭矩传感器检测刷轴旋转阻力(标准值≤2.5N·m),同时评估毛刷与瓶壁的贴合度。建议采用频闪仪观测毛刷与瓶体的接触面积,确保达到90%以上有效覆盖率。对于可调速机型,需测试各档位转速偏差(±5r/min)及急停响应时间(<3秒)。
3. 清洁剂残留与温控检测
使用pH计和电导率仪监测清洗槽内溶液浓度波动(允许偏差±0.3%),采用红外热像仪检测各温区实际温度与设定值的偏差(±2℃)。重点验证加热系统的升温速率(≥3℃/min)、温度均匀性(±1.5℃)及超温保护功能。排水阶段需检测残留水量(≤50ml/批次),防止交叉污染。
4. 设备密封性与安全防护检测
通过0.5MPa气压测试验证设备密封性(泄漏率<3%),使用分贝仪检测运行噪音(≤75dB(A))。安全检测需包含急停按钮响应测试(全系统断电时间<2秒)、防护门联锁功能验证、漏电保护装置测试(动作电流≤30mA)等项目,确保符合GB 5226.1机械电气安全标准。
5. 自动化功能与能耗检测
采用模拟信号发生器测试PLC控制系统对各执行元件的响应精度(定位误差≤0.5mm),记录设备单位能耗(kW·h/千瓶)。同步检测光电传感器的识别准确率(≥99.8%)、传送带同步误差(±0.1s)等参数,通过300次连续运行测试验证系统稳定性。
检测周期与结果应用
建议每季度开展基础检测,年度进行深度检测,大修后必须执行全面检测。检测数据应建立趋势分析档案,对毛刷更换周期、喷嘴清洁频率等维护项目提供决策依据。对于关键参数偏差超过10%的情况,需立即启动设备校正程序并复检,确保生产质量体系持续合规。
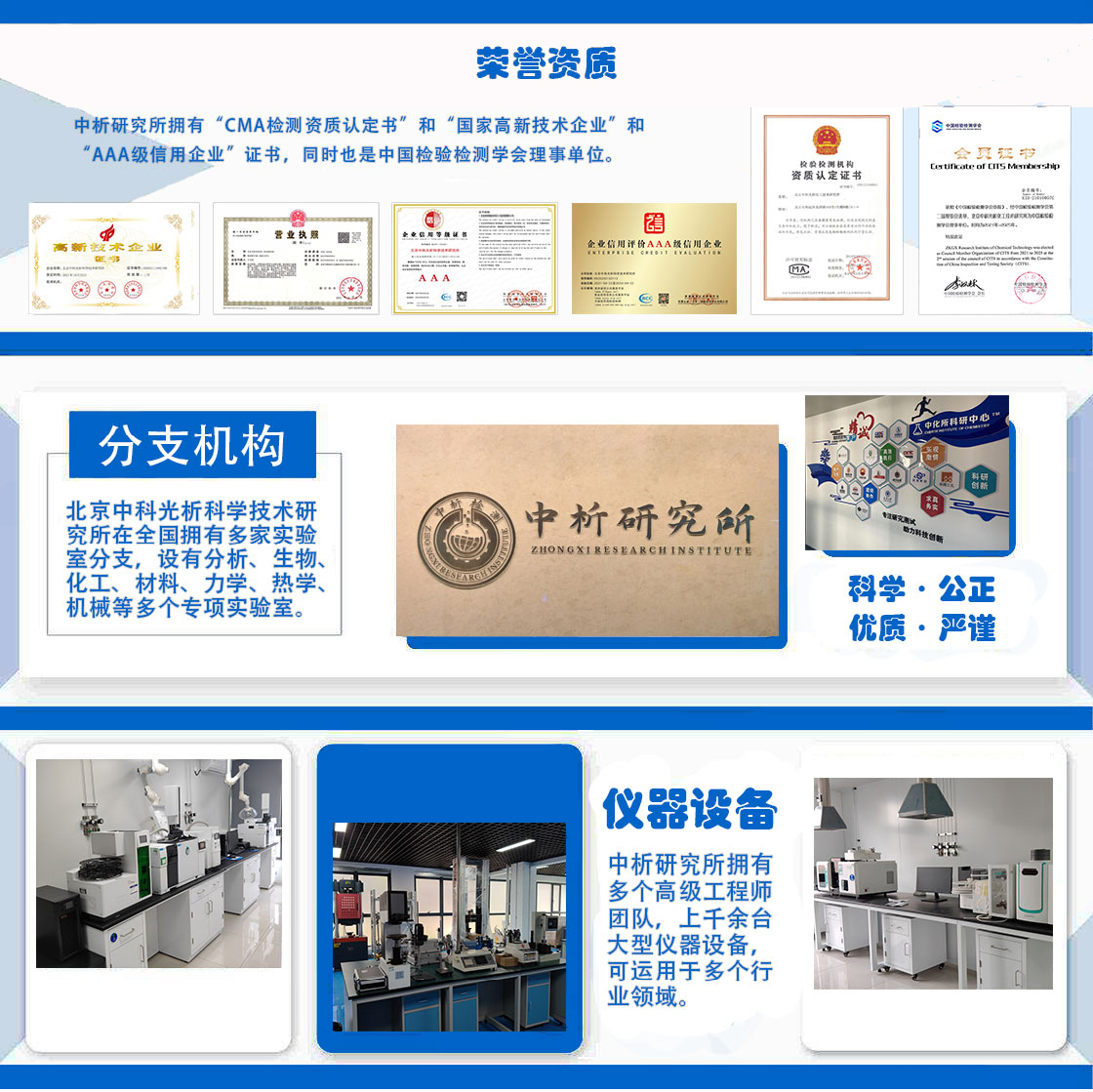
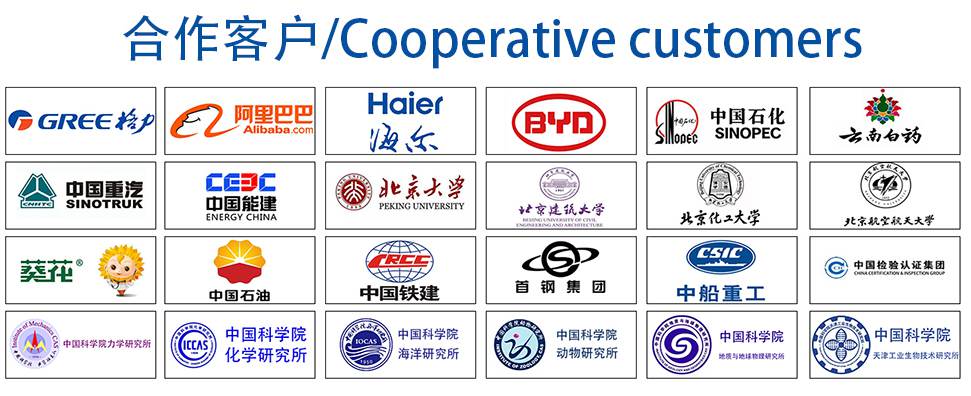