全自动一步法注拉吹成型机检测的重要性
全自动一步法注拉吹成型机是塑料容器生产领域的核心设备,广泛应用于食品、医药、日化等行业的高精度包装瓶生产。其通过注塑、拉伸、吹塑一体化工艺,能够高效完成从原料到成品的全流程加工。由于生产过程涉及高温、高压及精密控制,设备的性能稳定性、安全性和成品质量直接关系企业生产效率和成本控制。因此,针对该设备的全面检测成为确保生产连续性与产品合格率的关键环节。检测项目需覆盖机械结构、控制系统、工艺参数及成品质量等多个维度,以识别潜在故障风险并优化工艺参数。
核心检测项目分类与标准
1. 机械系统检测
包括模具对位精度、开合模机构同步性、液压/气动系统压力稳定性等。需使用激光测距仪检测模具闭合间隙(误差需≤0.05mm),通过压力传感器验证油缸/气缸输出压力是否满足工艺要求(如液压系统压力波动值需≤±1MPa)。此外,拉伸杆与吹气杆的同轴度需通过千分表测量,偏差应控制在±0.01mm以内。
2. 温控系统检测
注塑段的料筒温度、模温机循环水温及吹塑段模具温度是检测重点。采用红外测温仪与热电偶复合验证温控精度,要求各区段温度波动不超过±2℃。同时需检测加热元件的绝缘电阻(≥5MΩ)和PID控制响应速度,确保快速达到设定值且无超调。
3. 电气与安全检测
覆盖伺服电机扭矩输出稳定性、PLC程序逻辑正确性及安全保护装置(如急停按钮、防护门联锁)的响应灵敏度。需通过伺服调试软件监测电机动态负载曲线,确保其与工艺参数匹配。安全回路需进行强制触发测试,验证停机响应时间≤0.1秒。
4. 成品质量关联性检测
通过统计分析成品瓶的壁厚均匀性(壁厚差≤5%)、垂直度(偏差≤0.3mm)及密封性(氮气保压测试泄漏率≤0.5%),反向验证设备工艺参数的合理性。需使用三坐标测量仪、气密性检测仪等专业设备完成数据采集。
5. 效率与能耗评估
记录单模次循环时间、单位产量能耗(kW·h/kg)及原料利用率(废料率≤3%),结合设备铭牌参数评估运行效率。同时需检测噪声水平(≤75dB)和振动强度(≤4.5mm/s),确保符合职业健康标准。
检测周期与优化建议
建议每季度开展预防性检测,并在设备大修或工艺调整后增加专项检测。检测数据应建立趋势分析模型,对磨损部件(如模具导柱、液压密封件)进行寿命预测。优化方向可包括:升级闭环温控模块、引入视觉定位系统提升对位精度、通过物联网平台实现实时状态监控等。
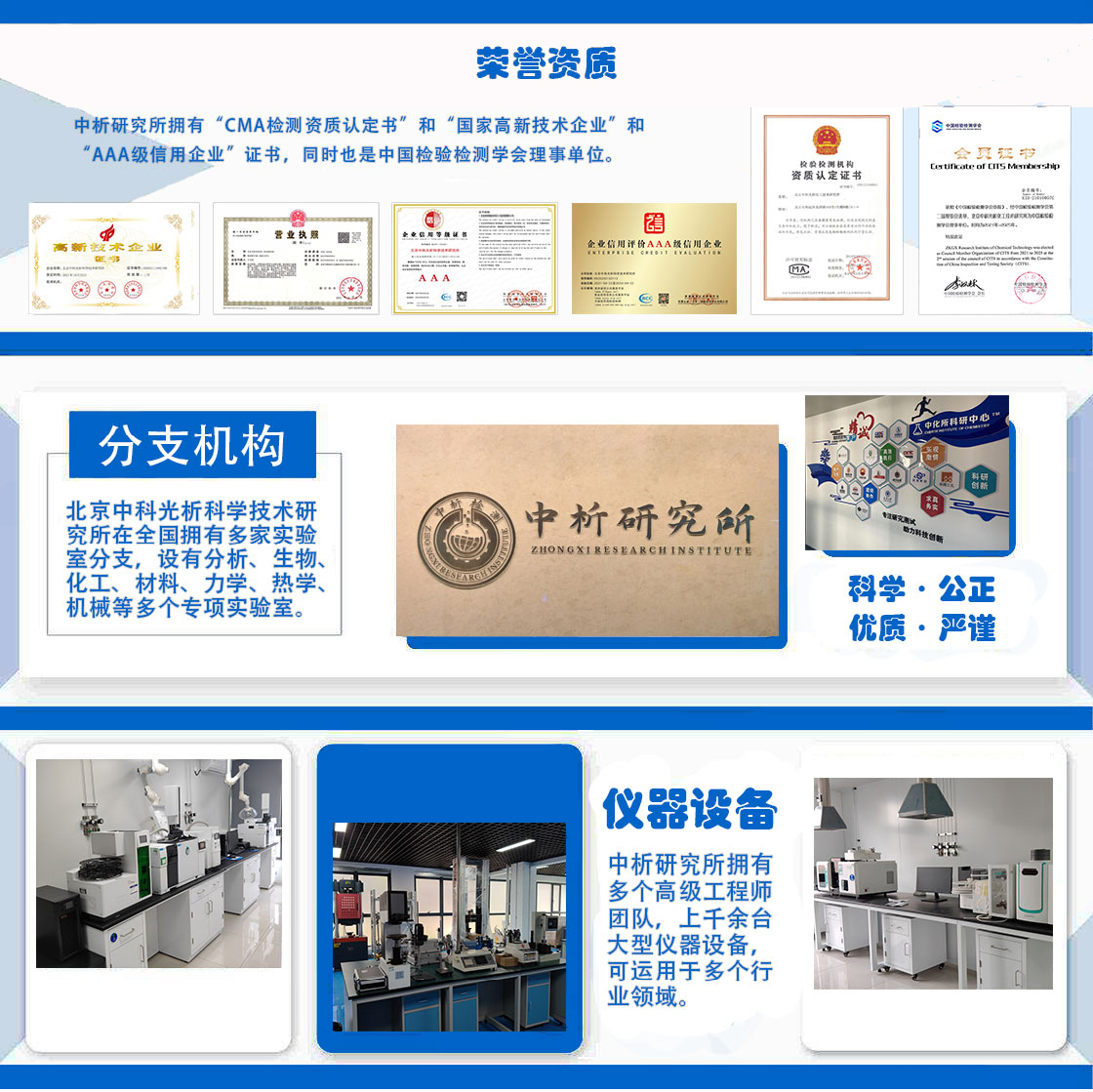
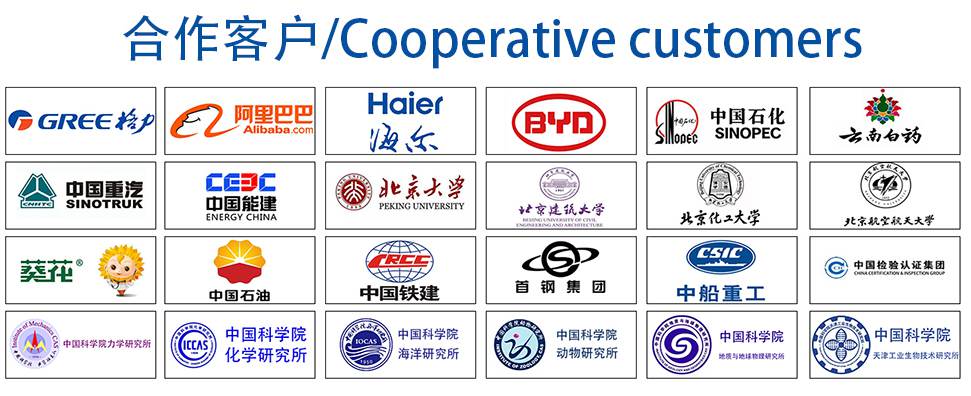