商用车辆行车制动器检测:安全运输的核心保障
商用车辆作为物流运输和人员载运的支柱工具,其制动系统的可靠性直接关系到道路交通安全。据统计,超过30%的商用车交通事故与制动系统故障相关,而行车制动器作为制动系统的核心部件,其性能检测成为车辆年检、日常维保及故障排查的关键环节。根据GB 7258《机动车运行安全技术条件》和JT/T 1094《营运客车安全技术条件》等标准要求,商用车辆行车制动器需定期开展系统性检测,涵盖静态参数、动态效能、密封性及功能性四大类检测项目,确保制动力分配均衡、响应灵敏且无泄漏风险。
一、静态检测项目
静态检测侧重于制动器基础结构的完整性评估,包括制动盘/鼓厚度测量、摩擦片磨损量检测以及制动间隙校准。使用游标卡尺或激光测厚仪对制动盘厚度进行多点位测量,若低于制造商标定值的80%则需更换。摩擦片剩余厚度需≥3mm(鼓式)或≥1.5mm(盘式),同时检查是否存在裂纹或油污污染。制动间隙调整需符合车辆技术手册要求,气压制动的推杆行程误差应控制在±2mm内。
二、动态制动力测试
通过滚筒式制动试验台或平板式检测仪进行动态测试,测量各轴制动力占比及平衡性。依据GB 38900标准,总制动力需≥车辆整备质量的60%,且同轴左右轮制动力差值≤20%。对于挂车,主挂车制动力传递延迟应<0.4秒。测试时需记录制动响应时间(踩下踏板至制动力达到峰值的时间),商用车要求≤0.6秒。
三、气压/液压系统密封性检测
针对气压制动的商用车辆,使用气压表监测储气筒压力降:关闭发动机后,压力降低值在10分钟内应≤0.1MPa;液压系统则通过制动踏板保压测试,保持500N踩踏力时,10秒内踏板下沉量≤3mm。同时检查制动管路接头、分泵及主缸是否存在漏油/漏气现象,使用泡沫检漏剂辅助定位微小泄漏点。
四、电子控制系统功能验证
配备ABS/EBS的车辆需通过诊断仪读取故障码,并执行轮速传感器信号测试。在低附着力路面进行紧急制动,观察车轮是否出现抱死现象,ABS作动频率应达到6-12次/秒。对于AEBS(自动紧急制动系统),还需验证毫米波雷达与制动执行机构的协同响应性能,测试碰撞预警触发距离是否符合设计要求。
通过上述多维度的检测,可显著降低商用车因制动失效引发的安全事故风险。建议每5万公里或6个月进行一次全面制动系统检测,尤其注重山区高频制动工况下的摩擦材料热衰退特性评估,为道路运输安全构筑坚实防线。
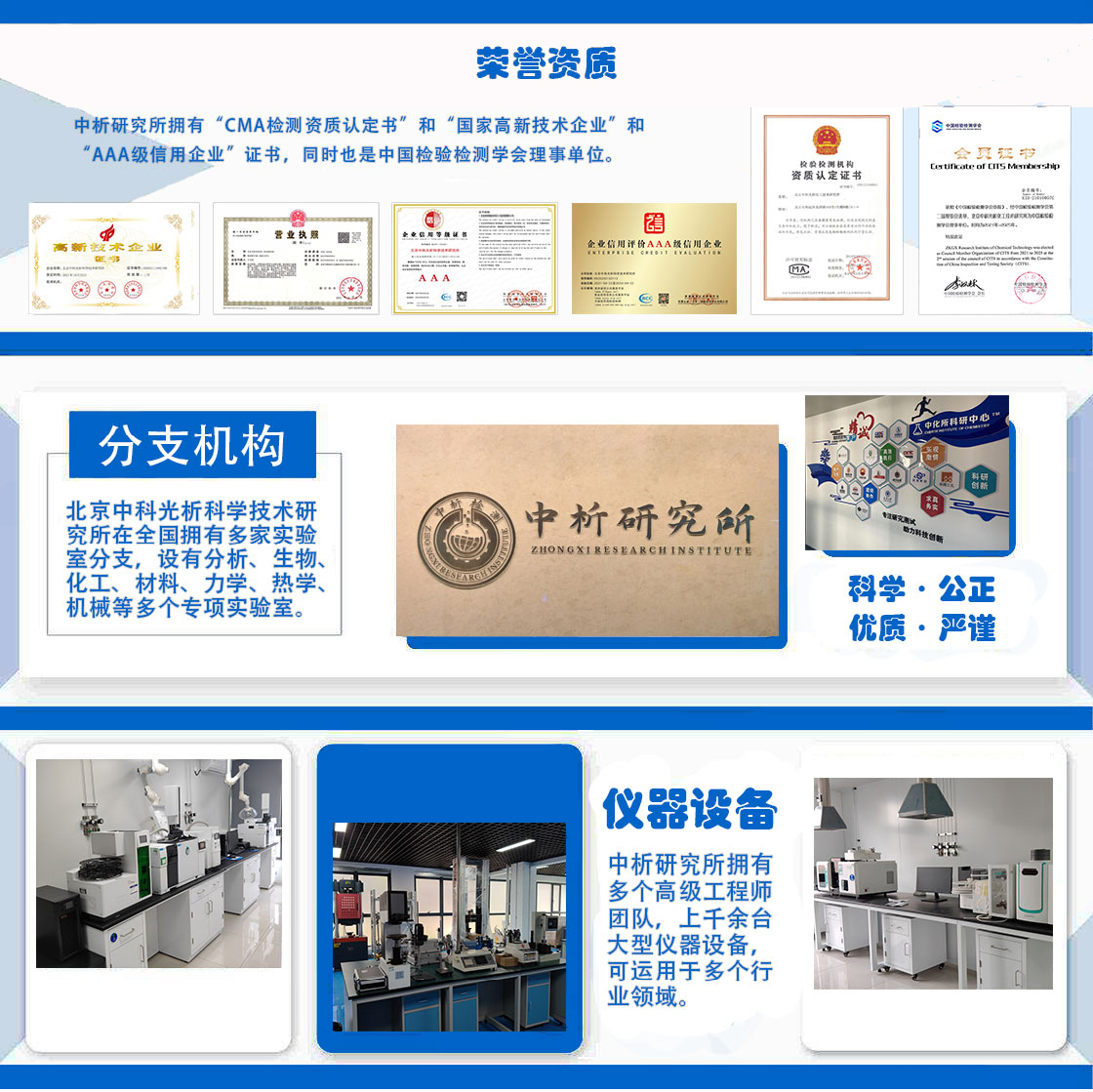
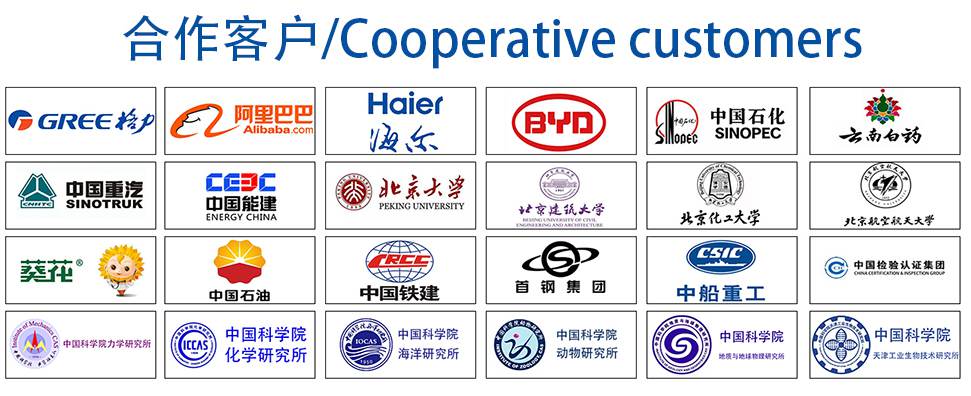