锰及合金检测的重要性
锰及合金作为现代工业中不可或缺的金属材料,广泛应用于钢铁冶炼、电池制造、航空航天等领域。锰的加入能显著提升材料的强度、耐磨性和耐腐蚀性,但其性能的稳定性直接取决于化学成分、物理结构及加工工艺的精准控制。因此,锰及合金的检测是确保材料质量、优化生产工艺和保障应用安全的核心环节。通过科学的检测手段,可以全面评估材料的成分均匀性、力学性能、微观组织特征及环境适应性,避免因材料缺陷导致的产品失效或安全隐患。
主要检测项目及方法
1. 化学成分分析
化学成分是决定锰及合金性能的基础。检测项目包括锰(Mn)主含量、碳(C)、硅(Si)、磷(P)、硫(S)等杂质元素,以及合金中添加的镍(Ni)、铬(Cr)、铜(Cu)等微量元素。常用方法包括电感耦合等离子体光谱法(ICP-OES)、X射线荧光光谱法(XRF)和化学滴定法。精确的化学成分分析可确保材料符合GB/T 5682、ASTM A99等国内外标准要求。
2. 物理性能测试
物理性能检测涵盖硬度(布氏、洛氏)、密度、拉伸强度、屈服强度、延伸率和冲击韧性等指标。通过万能材料试验机、硬度计等设备,模拟材料在实际工况下的力学响应,验证其是否满足不同应用场景的载荷需求。例如,高铁轨道用锰钢需具备高抗冲击性和疲劳强度,而电池用锰合金则需关注导电性和热稳定性。
3. 金相组织分析
通过金相显微镜、扫描电镜(SEM)观察材料的显微组织,包括晶粒尺寸、相组成、夹杂物分布及热处理效果。例如,锰钢中奥氏体与马氏体的比例直接影响其耐磨性能。金相分析可揭示材料在铸造、轧制或热处理过程中可能产生的偏析、裂纹等缺陷,为工艺优化提供依据。
4. 耐腐蚀性评估
采用盐雾试验、电化学极化曲线法、浸泡腐蚀试验等方法,模拟酸性、碱性或海洋环境对材料的侵蚀作用。锰合金的耐蚀性与其表面氧化膜致密性及合金元素配比密切相关,检测结果可指导材料在化工设备或海洋工程中的选型。
5. 无损检测技术
针对成品或半成品,使用超声波探伤(UT)、磁粉检测(MT)、渗透检测(PT)和X射线探伤(RT)等手段,在不破坏材料的前提下识别内部裂纹、气孔等缺陷。尤其在航空航天领域,无损检测是保障关键部件可靠性的必要环节。
检测标准与规范
锰及合金检测需遵循ISO 4945、ASTM E353、GB/T 223等国际及国家标准,同时结合行业特定要求(如汽车工业的IATF 16949)。实验室需通过 或CMA认证,确保检测数据的权威性和可比性。
结语
随着新材料技术的快速发展,锰及合金的检测需求日益精细化。通过多维度、高精度的检测手段,不仅能够提升产品质量,还能推动材料设计的创新。未来,人工智能与大数据技术的应用将进一步优化检测流程,实现从“事后检测”到“过程控制”的转型升级。
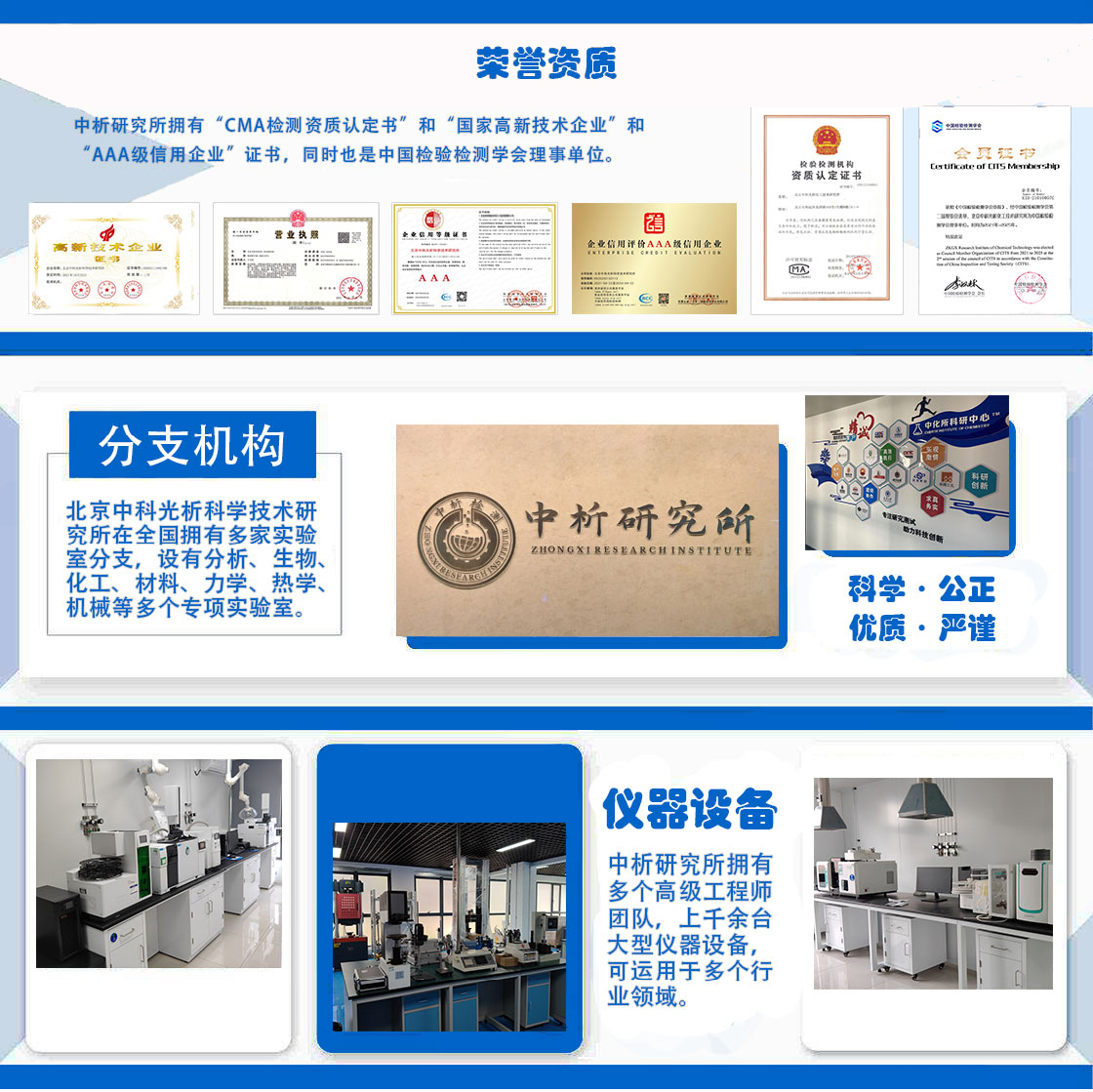
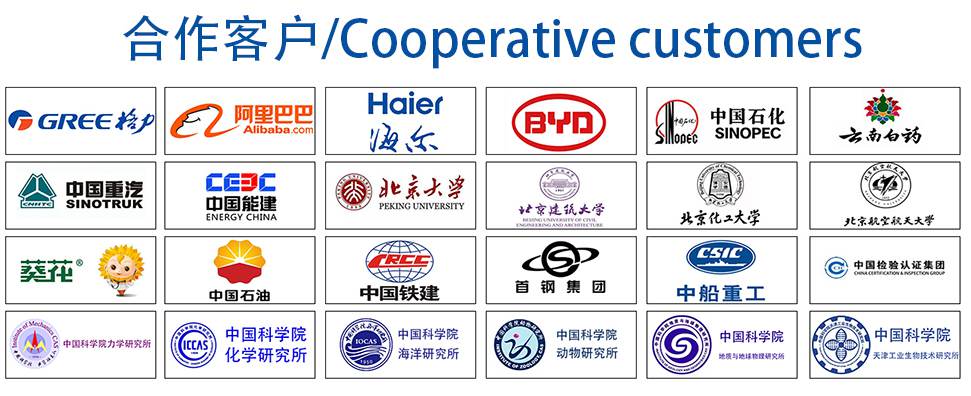