纳滤膜元件检测
实验室拥有众多大型仪器及各类分析检测设备,研究所长期与各大企业、高校和科研院所保持合作伙伴关系,始终以科学研究为首任,以客户为中心,不断提高自身综合检测能力和水平,致力于成为全国科学材料研发领域服务平台。
立即咨询纳滤膜元件检测:关键项目与技术要求解析
纳滤膜元件作为水处理、医药分离、食品浓缩等领域的核心材料,其性能直接关系到系统运行效率与产品质量。随着膜技术应用场景的扩展,纳滤膜检测已成为保障膜元件可靠性、延长使用寿命的重要环节。本文针对膜元件的关键检测项目展开分析,涵盖物理性能、化学稳定性及功能性指标,为行业用户提供检测流程与评价依据。
一、核心物理性能检测
1. 膜表面结构分析:通过扫描电子显微镜(SEM)观察膜孔径分布及表面形貌,评估制造工艺一致性;
2. 厚度与均匀性测试:采用非接触式测厚仪检测膜层厚度偏差,确保不超过±5%的行业标准;
3. 机械强度验证:利用抗拉试验机测量断裂伸长率和抗压强度,模拟实际工况下的机械应力。
二、化学稳定性评价体系
1. 耐酸碱性测试:将膜片分别浸泡在pH=2和pH=12溶液中500小时,观察通量衰减率与脱盐率变化;
2. 氧化耐受性试验:以200ppm次氯酸钠溶液进行循环冲击,检测膜材料氧化损伤程度;
3. 有机溶剂兼容性:针对特定应用场景测试乙醇、丙酮等溶剂接触后的溶胀率。
三、功能性指标验证流程
1. 截留性能检测:采用标准氯化钠(2000ppm)和硫酸镁(1000ppm)溶液,在0.5MPa压力下测定截留率;
2. 产水通量测试:记录25℃恒温条件下单位时间单位面积的产水量(LMH);
3. 跨膜压差分析:建立压力-通量曲线,评估膜元件抗污染能力与长期运行稳定性。
四、特殊环境适应性检测
1. 高温耐受性实验:在45-60℃区间内连续运行100小时,监测膜通量恢复率;
2. 微生物挑战测试:接种特定浓度菌群,验证膜元件抗菌涂层有效性;
3. 极端水质模拟:采用高硬度(Ca²⁺≥500mg/L)、高浊度(NTU≥50)原水进行加速老化测试。
通过系统性检测可明确纳滤膜元件的性能边界,建议企业依据ISO 9001质量管理体系建立全生命周期检测档案,重点关注初始性能衰减曲线的斜率变化。对于工业级应用场景,还需补充第三方机构认证,确保检测结果符合GB/T 30307-2013《纳滤膜元件检测方法》等行业规范要求。
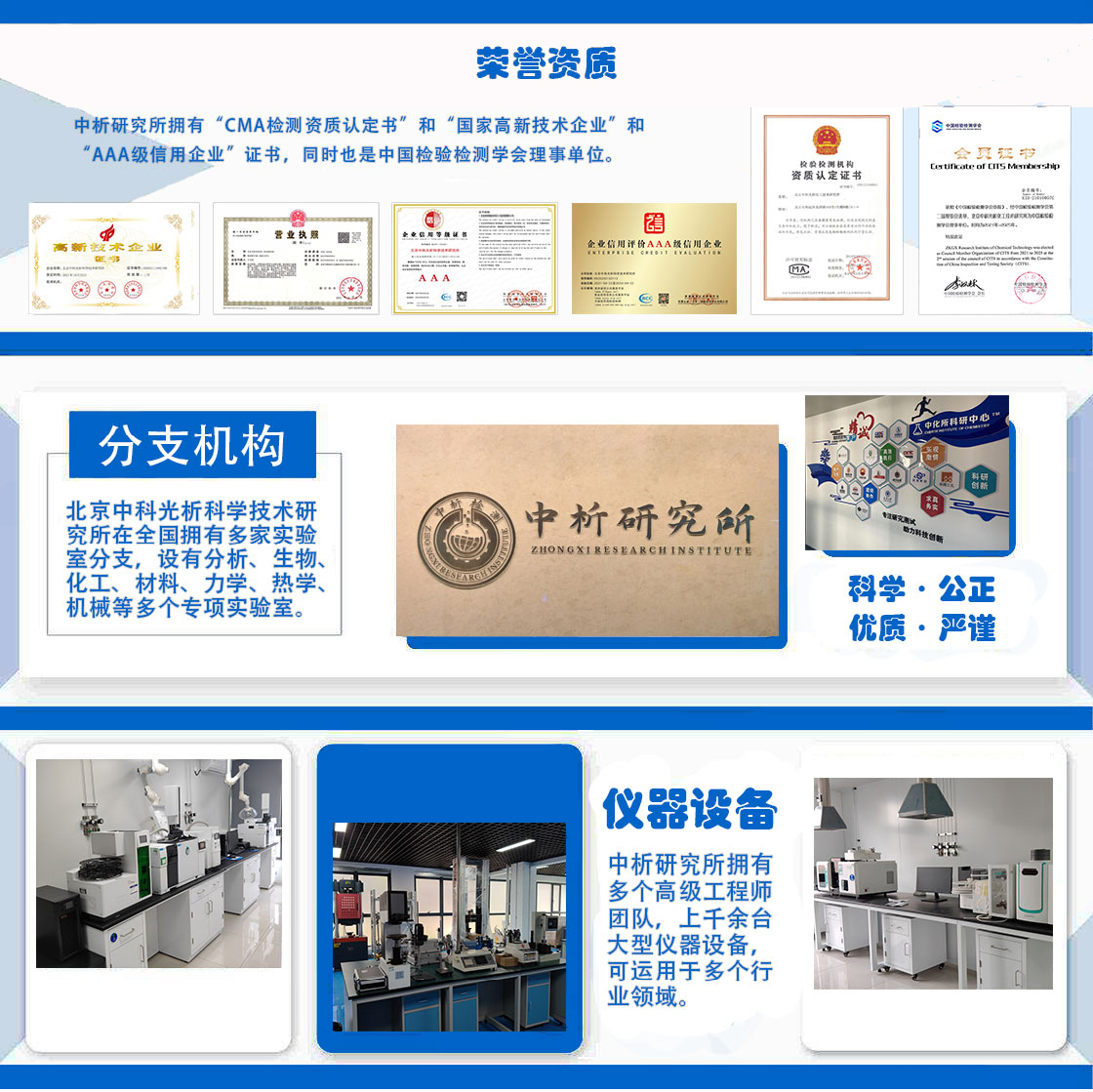
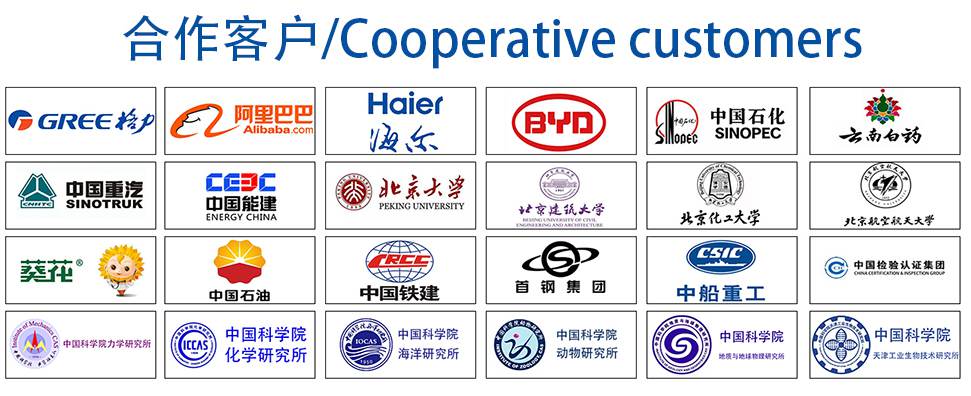