机器人用齿轮传动装置(试验方法)检测
实验室拥有众多大型仪器及各类分析检测设备,研究所长期与各大企业、高校和科研院所保持合作伙伴关系,始终以科学研究为首任,以客户为中心,不断提高自身综合检测能力和水平,致力于成为全国科学材料研发领域服务平台。
立即咨询机器人用齿轮传动装置(试验方法)检测
随着机器人技术的快速发展,齿轮传动装置作为其核心动力传输部件,其性能直接影响机器人的运动精度、可靠性和使用寿命。为确保齿轮传动装置满足高负荷、高精度及长时间稳定运行的要求,需通过科学的试验方法进行全面检测。检测项目需覆盖静态特性、动态响应、耐久性及环境适应性等多个维度,并结合国际标准(如ISO、GB等)与行业规范,形成系统化的测试体系。
1. 传动精度检测
传动精度是衡量齿轮传动装置性能的核心指标之一。检测内容包括齿轮副的背隙(Backlash)、传动误差(Transmission Error)及回程误差。通过高精度编码器或激光干涉仪进行动态测试,记录输入轴与输出轴的转角偏差,分析其线性度与重复性。同时需模拟不同负载条件下的传动精度变化,评估其对机器人定位精度的影响。
2. 承载能力与疲劳试验
齿轮传动装置的承载能力决定了其在机器人高速、重载工况下的可靠性。检测需开展静态极限载荷试验和动态疲劳试验:静态测试通过逐步增加扭矩至额定值的1.5-2倍,监测齿轮齿面是否发生塑性变形或断裂;动态疲劳试验则以额定载荷连续运行数万次循环,观察齿面磨损、点蚀及裂纹扩展情况,评估其寿命预测模型的有效性。
3. 噪声与振动测试
噪声和振动水平直接影响机器人运行的平稳性及用户体验。检测需在消音室内进行,使用声级计采集齿轮箱在不同转速和负载下的噪声频谱,分析主要噪声源(如啮合频率、轴系共振)。振动测试则通过加速度传感器监测齿轮箱外壳的振动幅值,结合FFT分析识别异常频率成分,优化齿轮修形参数以降低振动能量。
4. 温度特性与润滑性能验证
齿轮传动装置的温升和润滑效果直接影响其长期稳定性。试验需模拟极端温度环境(-20℃至80℃),连续运行后测量齿轮箱表面温度分布,评估散热设计是否合理。同时,通过润滑油采样分析金属磨粒含量、黏度变化及添加剂损耗,验证润滑系统在高低温、高速条件下的持续保护能力。
5. 材料与表面处理检测
齿轮材料的强度、韧性及表面处理工艺是保障传动性能的基础。试验包括齿轮材料的金相分析、硬度梯度测试(如渗碳层深度)及残余应力检测。针对表面涂层(如DLC、氮化处理),需通过摩擦磨损试验机评估其抗胶合能力和耐磨性,确保在高接触应力下的性能稳定性。
6. 动态响应特性测试
针对机器人快速启停、变速等动态工况,需测试齿轮传动装置的响应速度与跟随精度。通过施加阶跃扭矩或正弦扫频激励,采集输出轴的动态响应曲线,计算其带宽、共振频率及相位延迟,为机器人运动控制算法提供参数补偿依据。
综上所述,机器人用齿轮传动装置的试验方法需围绕精度、强度、寿命、环境适应性四大核心目标展开,结合齐全的测试设备与数据分析技术,形成覆盖设计验证、生产质控及故障诊断的全生命周期检测体系,为高性能机器人开发提供可靠保障。
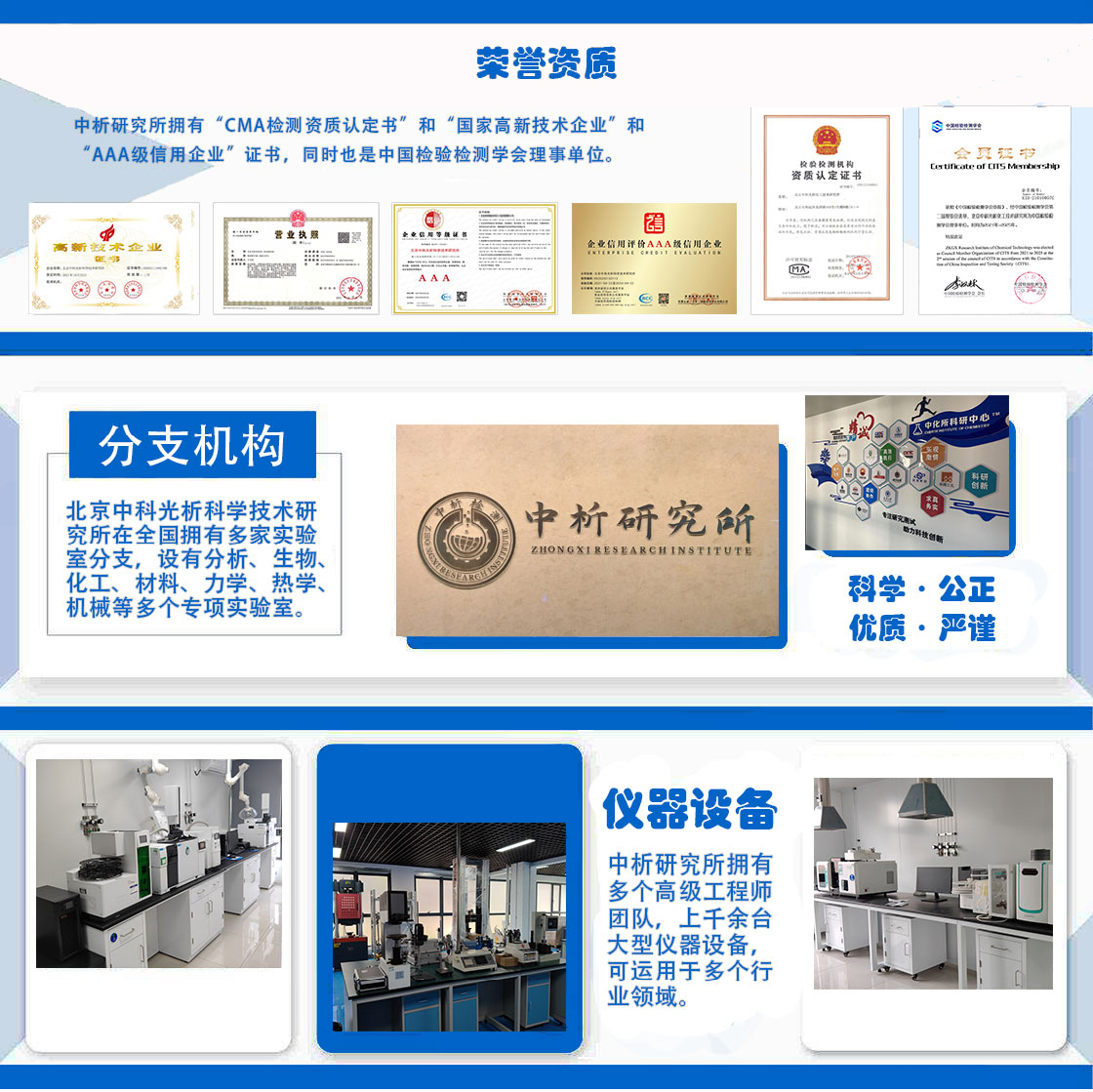
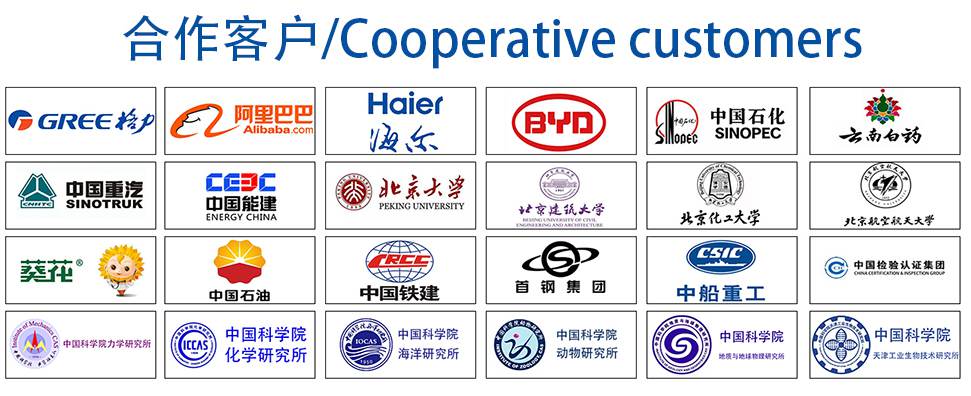