数控加工生产线检测的重要性与核心项目解析
随着制造业智能化升级的加速,数控加工生产线已成为精密零部件生产的核心载体。为确保加工精度、设备稳定性和产品质量,系统化的检测流程成为生产线运行中不可或缺的环节。数控加工检测不仅涉及机床本身的性能验证,还包括加工过程的全方位监控,通过多维度数据采集与分析,能够有效预防批量性缺陷、降低设备损耗率,并实现生产过程的持续优化。
一、几何精度检测
作为检测体系的基础环节,几何精度检测包含机床定位精度、重复定位精度及运动轴垂直度等关键指标。通过激光干涉仪、球杆仪等专业设备,对X/Y/Z轴的位置偏差进行微米级测量,同时检测主轴径向跳动和端面跳动误差。近年引入的激光跟踪仪技术,可在动态条件下实时监测多轴联动精度,确保复杂曲面加工的几何一致性。
二、动态性能测试
该检测项目重点关注机床在高速运转状态下的稳定性。通过振动传感器监测主轴轴承、导轨等关键部件的异常振荡,利用热成像仪分析设备温升对加工精度的影响。切削力测试系统可实时采集不同工艺参数下的受力变化,为优化切削参数提供数据支撑。典型案例显示,动态性能检测能使刀具寿命提升15%-20%。
三、工件质量分析
基于三坐标测量机(CMM)的成品检测构成质量控制核心,重点检测尺寸公差、形位公差及表面粗糙度。针对特殊材料加工件,采用工业CT进行内部结构无损检测。最新研发的在线检测系统已实现加工过程中实时尺寸反馈,结合机器学习算法可自动调整补偿值,将废品率控制在0.3%以下。
四、系统功能验证
涵盖数控系统、伺服驱动单元及传感器网络的综合检测,通过模拟信号测试验证各模块的响应速度和协同性。重点检查急停保护、刀具破损检测等安全功能的可靠性,同时评估通信协议的稳定性和抗干扰能力。智能制造环境下,还需对设备接入工业物联网的平台兼容性进行专项测试。
五、环境与安全检测
包括车间温湿度对加工精度影响的量化分析,切削液浓度监测及废气排放检测。安全方面重点关注设备接地电阻、漏电保护装置有效性,以及防护门联锁系统的响应速度。欧盟CE认证要求下的噪声水平检测(通常需≤75dB)也属于必检项目。
六、数据追溯与管理
基于MES系统的检测数据集成平台,实现从原材料到成品的全流程追溯。通过SPC统计过程控制技术,对关键质量特性进行趋势预测和异常预警。最新实践表明,结合区块链技术的检测数据存证系统,可使质量追溯效率提升40%以上。
在工业4.0背景下,数控加工检测正向智能化、网络化方向加速演进。通过构建检测数据与数字孪生模型的实时交互,企业不仅能提升质量控制水平,更能实现预防性维护和工艺自主优化。未来,随着5G通信和AI视觉检测技术的深度应用,数控加工检测将进入全要素感知、全流程闭环的新阶段。
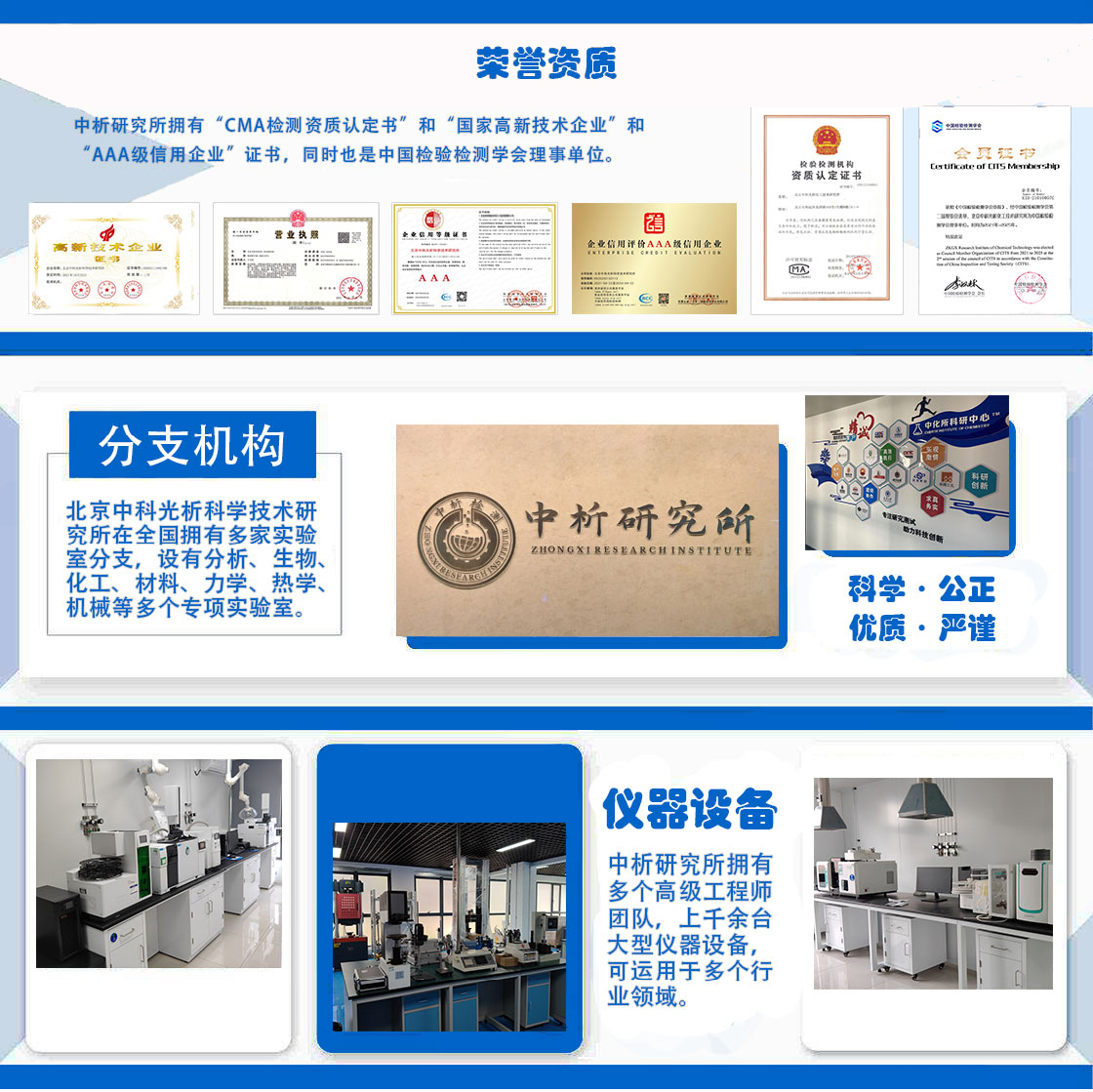
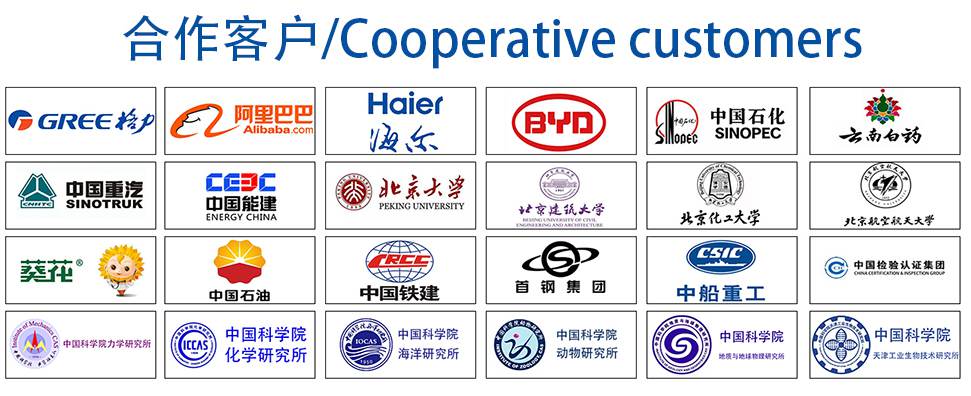