聚合物基复合材料因其优异的比强度、耐腐蚀性和可设计性,在航空航天、交通运输、新能源等领域得到广泛应用。其中,无支持工作段结构作为复合材料典型应用形式,在承受压缩载荷时易发生剪切失稳破坏,对材料性能检测提出了特殊要求。剪切加载条件下的压缩性能检测是评估该类材料结构完整性的关键环节,需从材料力学响应、界面结合强度、损伤演化机制等多维度开展系统性检测分析。
一、剪切加载下的压缩性能测试
通过设计专用夹具实现0°-90°可调剪切角加载,采用位移控制模式进行准静态压缩试验。重点监测材料在0.2%偏移屈服强度、压缩弹性模量及断裂韧性值等关键参数,同步采集应变场分布数据。使用高速摄像机记录试样从层间开裂到纤维断裂的全过程破坏形貌,结合数字图像相关技术分析破坏起始位置与扩展路径。
二、材料各向异性评估
针对复合材料层合板正交各向异性特征,分别沿0°、45°、90°方向制备试样进行对比测试。采用三点弯曲法测定面内剪切模量,通过X射线衍射分析纤维取向分布,结合显微CT技术观测材料内部孔隙率及纤维排布均匀性。建立各向异性指数评价体系,量化材料方向性对压缩性能的影响规律。
三、界面结合强度测试
采用短梁剪切试验(SBS)测定层间剪切强度(ILSS),使用双悬臂梁试验(DCB)测试模式I型断裂韧性。通过纳米压痕技术测量树脂基体与增强纤维的微观界面强度,结合扫描电镜(SEM)观察界面脱粘形貌。建立界面性能与宏观压缩破坏模式的相关性模型,优化纤维表面处理工艺参数。
四、湿热环境影响试验
模拟实际工况环境,在温度(-55℃至120℃)和湿度(50-95%RH)交变条件下开展加速老化实验。测定材料压缩强度保留率、吸湿膨胀系数等关键参数,通过动态力学分析(DMA)研究玻璃化转变温度(Tg)变化。建立湿热-力学耦合模型,评估环境因素对材料压缩性能的衰减机制。
五、动态力学性能分析
采用高频疲劳试验机进行10^4-10^7次循环加载,获取S-N曲线和剩余强度衰减规律。通过动态机械分析仪测试储能模量、损耗模量随频率变化曲线,结合DIC技术观测动态载荷下的损伤累积过程。建立基于能量耗散的疲劳寿命预测模型,为结构耐久性设计提供数据支持。
六、无损检测技术应用
采用超声C扫描检测内部缺陷分布,应用红外热像仪监测加载过程的热量释放特征。通过声发射技术捕捉损伤产生时的特征频率信号,结合模式识别算法实现破坏类型分类。开发多源数据融合的在线监测系统,实现压缩试验过程的实时状态评估与失效预警。
通过上述系统化检测方案,可获得无支持工作段聚合物基复合材料在剪切加载条件下的完整性能图谱。检测数据不仅为材料选型提供依据,还可通过逆向优化指导材料配方改进和铺层结构设计,显著提升复合材料结构的安全服役性能。
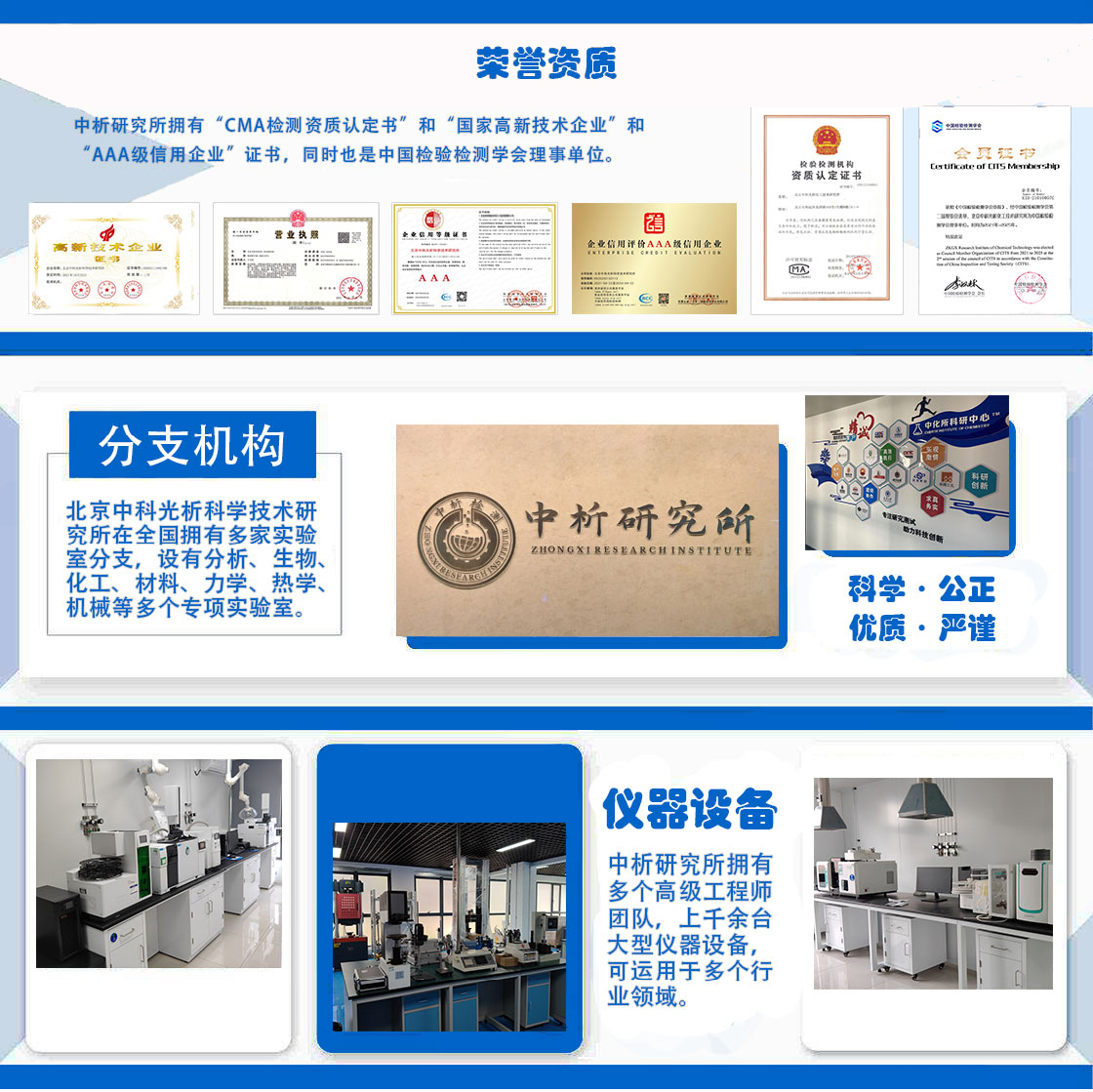
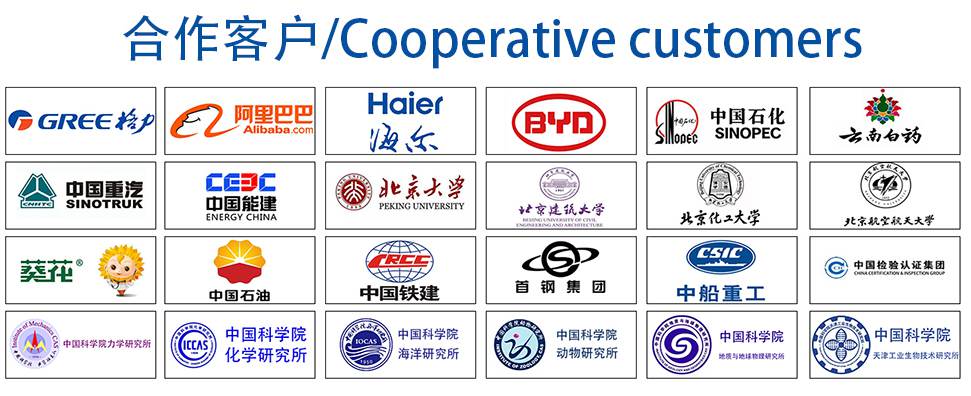