煤用分级破碎机检测的重要性与核心内容
煤用分级破碎机作为煤炭加工行业中关键设备之一,承担着原煤破碎、粒度分级和高效处理的核心任务。其性能直接影响生产线的运行效率、能源消耗及成品质量。随着煤炭行业对设备安全性、环保性和智能化要求的提升,定期开展系统性检测成为保障设备稳定运行、延长使用寿命、降低故障风险的必要手段。通过科学规范的检测流程,可精准评估设备状态,及时发现潜在隐患,为优化工艺参数和维护计划提供数据支撑。
核心检测项目与技术要求
1. 机械结构完整性检测
重点检查破碎机机架焊接质量、传动轴同轴度、轴承座定位精度等关键部位。使用超声波探伤仪对焊接缝进行无损检测,确保无裂纹或气孔缺陷;通过激光对中仪测量转子与电机的同轴度偏差,要求误差≤0.05mm/m;采用三维坐标仪评估机架变形量,最大形变需控制在3‰以内。
2. 耐磨部件性能评估
针对锤头、衬板等易损件进行硬度测试(洛氏硬度HRC≥58)、金相组织分析和磨损量测量。采用电子显微镜观察表面磨损形貌,结合能谱分析判定材料成分是否符合GB/T 35052-2018标准,并计算单周期磨损率是否超出设计允许值(通常≤1.2mm/千吨处理量)。
3. 破碎效能验证试验
按照MT/T 1028-2006标准开展负荷运行测试,连续48小时监测以下指标:入料粒度>300mm比例<5%、出料合格率≥95%、单位能耗≤1.8kWh/t。同步记录瞬时处理量波动幅度,要求标准差控制在额定产能的±5%范围内。
4. 安全防护系统检测
全面测试过载保护装置、紧急制动系统和防护罩连锁功能。模拟超载工况验证液压保护系统响应时间(≤0.3秒),检测防护罩开闭信号与主电机联锁的同步精度(延迟<50ms),确保符合AQ 1090-2020矿山机械安全规范要求。
5. 振动与噪声水平检测
在额定转速下,使用振动分析仪测量轴承座处的振动速度有效值(需<4.5mm/s),噪声测试点距设备1m处声压级应≤85dB(A)。频谱分析需排除异常频率峰值,避免发生共振风险。
6. 电气控制系统检验
检测PLC程序逻辑准确性、传感器信号反馈延迟(≤10ms)、变频器输出频率稳定性(波动率<0.5%)。进行200次连续启停测试,验证控制系统的可靠性与抗干扰能力,故障率须为0。
检测周期与结果应用
建议新设备安装后进行72小时全负荷检测验收,运行中每季度开展常规检测,大修前后需实施全面性能测试。检测数据应建立动态数据库,通过趋势分析预判关键部件剩余寿命,指导预防性维护。对于检测发现的衬板偏磨、轴承温升异常等问题,需结合工艺参数调整和设备改造进行闭环处理,确保设备始终处于最佳运行状态。
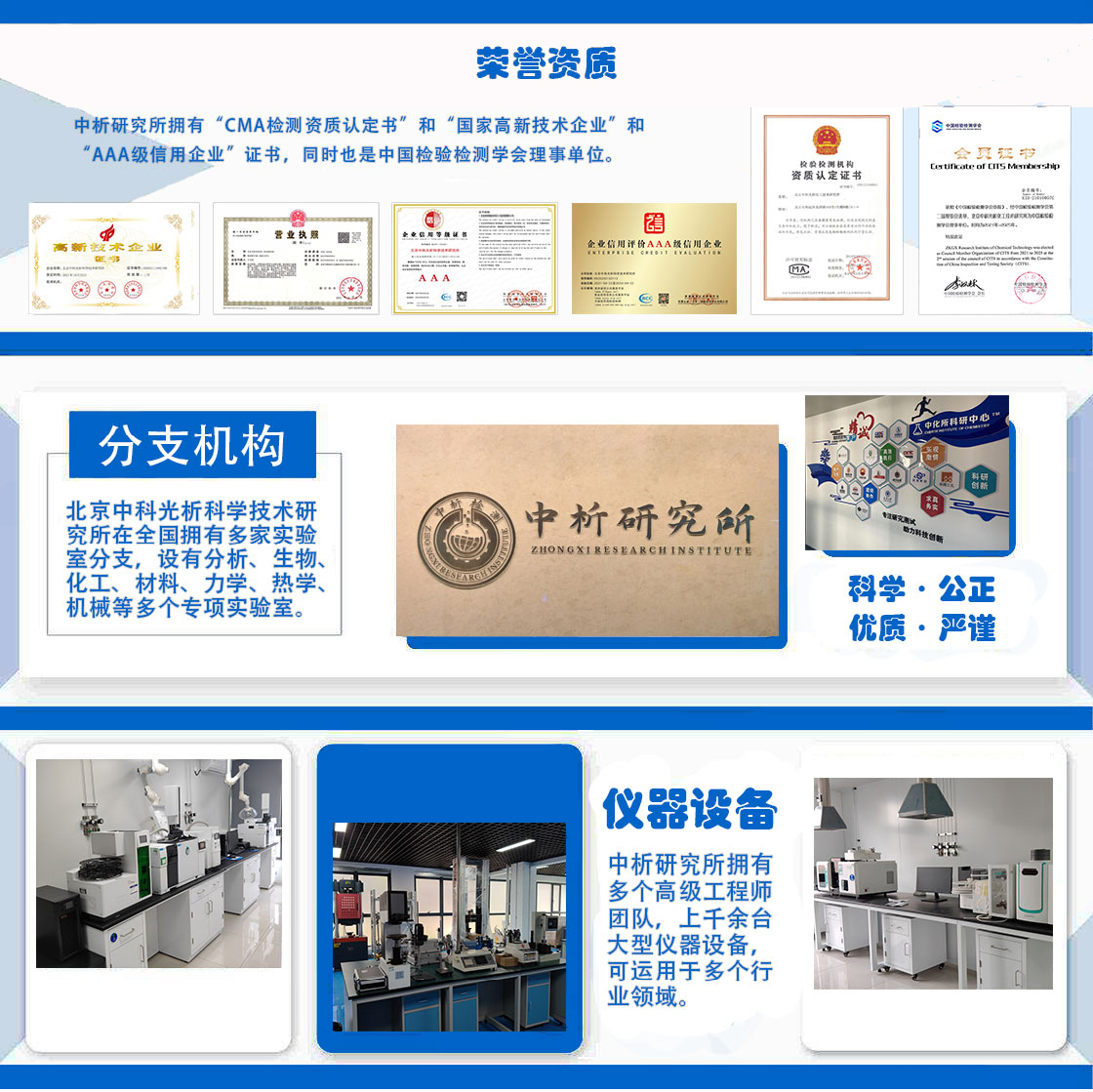
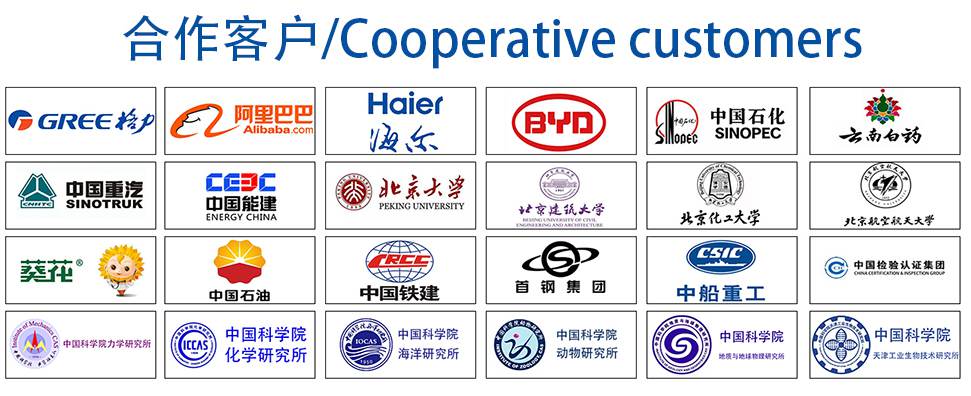