协作机器人检测的重要性与应用场景
协作机器人(Cobot)作为工业4.0时代的重要产物,已广泛应用于智能制造、医疗辅助、物流分拣等领域。与传统工业机器人不同,协作机器人需要与人类在同一空间内密切配合,这对安全性、精度和动态响应提出了更高要求。为确保协作机器人符合国际标准并满足实际使用需求,系统性检测成为产品研发、出厂验收和定期维护中的核心环节。目前ISO 10218-1/2、ISO/TS 15066等标准已明确规定了协作机器人需要满足的力控参数、运动轨迹偏差、人机交互安全等关键指标。
核心检测项目及技术要求
1. 安全功能验证
包括碰撞检测灵敏度测试(触发力阈值≤150N)、紧急停止响应时间(<500ms)、安全空间受限运动验证。需通过六维力传感器模拟人体不同部位碰撞场景,验证安全防护系统的实时性。
2. 运动性能检测
覆盖重复定位精度(±0.02mm)、轨迹跟踪误差(<0.5%)、最大速度限制(根据负载分级)。使用激光跟踪仪和动态捕捉系统进行三维空间轨迹分析,确保在复杂路径下的运动稳定性。
3. 负载能力测试
通过动态负载实验台模拟0-100%额定负载的快速切换,检测关节力矩输出平稳性,要求力矩波动率<5%。同时需验证过载保护机制的有效触发条件。
特殊场景专项检测
4. 环境适应性测试
包含IP防护等级验证(至少IP54)、电磁干扰耐受度(30V/m场强下无异常)、温湿度循环试验(-10℃~50℃)。针对医疗领域还需进行无菌环境兼容性检测。
5. 人机交互性能评估
重点测试语音指令识别准确率(>98%)、触觉反馈响应延迟(<80ms)、示教编程容错率。需构建多模态交互测试平台,模拟真实作业场景中的人机协作流程。
6. 数据安全检测
涉及通信协议加密强度测试(AES-256)、操作日志完整性校验、网络攻击防御能力验证。符合IEC 62443标准要求,防范生产数据泄露风险。
检测技术发展趋势
随着数字孪生技术的普及,基于虚拟现实的在线检测系统正逐步替代传统实验室检测。通过建立高精度动力学模型,可实现80%以上检测项目的数字化仿真验证。同时,AI驱动的自适应检测算法开始应用于异常工况预测,使检测效率提升40%以上,推动协作机器人检测进入智能化新阶段。
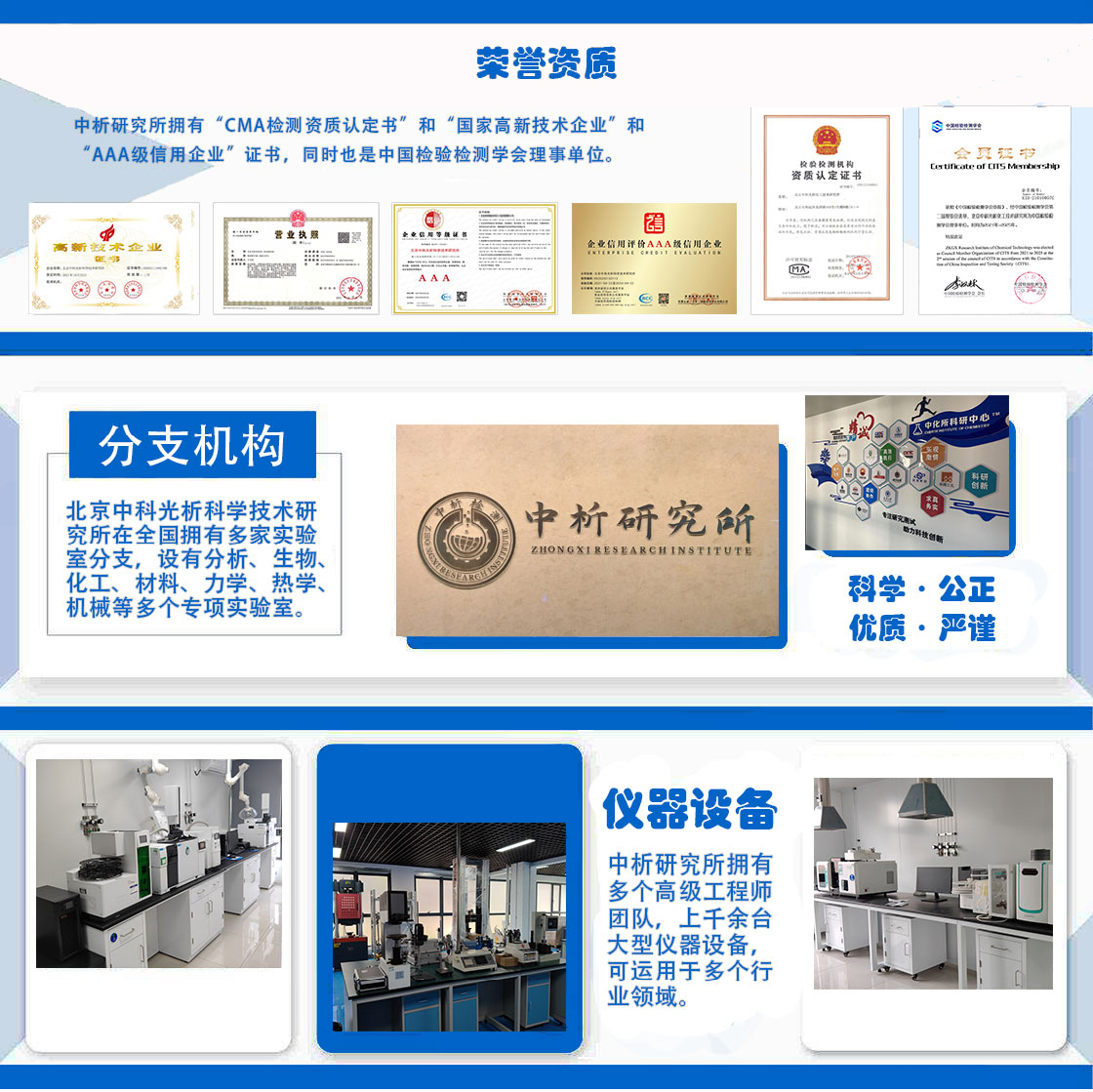
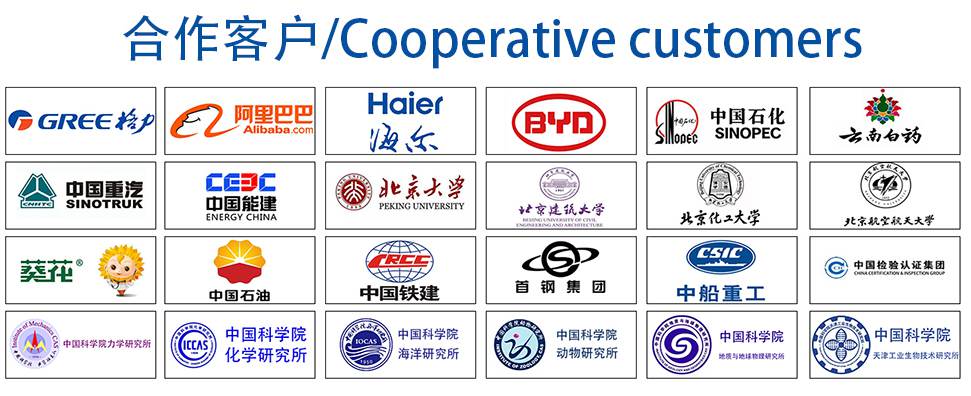