装配机器人检测:保障智能制造的核心环节
随着工业自动化技术的快速发展,装配机器人已成为现代制造业中不可或缺的关键设备。从汽车生产线到电子元器件组装,这些高精度机械系统通过复杂动作实现零部件的高速精准装配。然而,由于长期运行、负载变化及环境因素的影响,机器人性能可能逐渐偏离设计指标。因此,系统性检测成为确保装配质量、预防故障和维护生产效率的重要保障。通过科学的检测手段,不仅能够验证机器人是否符合技术规范,更能提前发现潜在风险,为智能化工厂的稳定运行提供数据支持。
核心检测项目与技术要点
1. 机械结构完整性检测
通过三维激光扫描仪对机器人关节间隙、零部件磨损量进行精密测量,结合振动传感器监测传动系统(如谐波减速器、同步带)的运行状态。重点检测高速运动时机械臂的变形量,确保结构刚度满足±0.02mm的定位精度要求。
2. 运动控制系统检测
采用激光跟踪仪对重复定位精度进行动态验证,测试范围需覆盖X/Y/Z三轴±180°工作空间。同步记录伺服电机扭矩波动曲线与编码器反馈数据,分析轨迹跟踪误差是否超出ISO 9283标准规定的0.15mm阈值。
3. 视觉识别系统校准
使用标准标定板对工业相机的畸变率、分辨率进行量化评估,通过多光源模拟测试验证图像处理算法在不同光照条件下的识别准确率。重点关注微小零件(<1mm)的抓取成功率及视觉引导定位响应时间。
4. 安全防护功能验证
依据ISO 10218安全标准,系统化测试急停响应时间(<500ms)、安全围栏互锁机制和碰撞检测灵敏度。通过模拟异常负载(超额定值20%)检验力矩限制功能的有效性,确保人机协作时的操作安全性。
5. 通信与集成兼容性测试
验证PLC、MES系统的数据交互协议(如Profinet、EtherCAT)兼容性,检测信号传输延时(≤5ms)与抗电磁干扰能力。特别关注多机器人协同作业时的时序同步精度,避免因通信延迟导致的装配工序错位。
6. 环境适应性评估
在温湿度试验箱中模拟-10℃至50℃极端工况,连续运行48小时监测润滑系统效能与电气元件稳定性。同时进行IP54防护等级验证,确保粉尘环境下关键部件的长期可靠运行。
检测数据驱动的优化策略
基于检测结果建立机器人性能衰退模型,通过振动频谱分析预测齿轮箱寿命周期,运用热成像技术优化散热设计。将检测数据与数字孪生系统结合,实现预测性维护与工艺参数动态调整,提升整体设备效能(OEE)3%-5%。
通过涵盖机械、电气、软件的多维度检测体系,企业可构建装配机器人的全生命周期健康管理方案。这不仅直接影响产品装配质量,更能降低30%以上的意外停机损失,为智能制造转型提供坚实的技术保障。
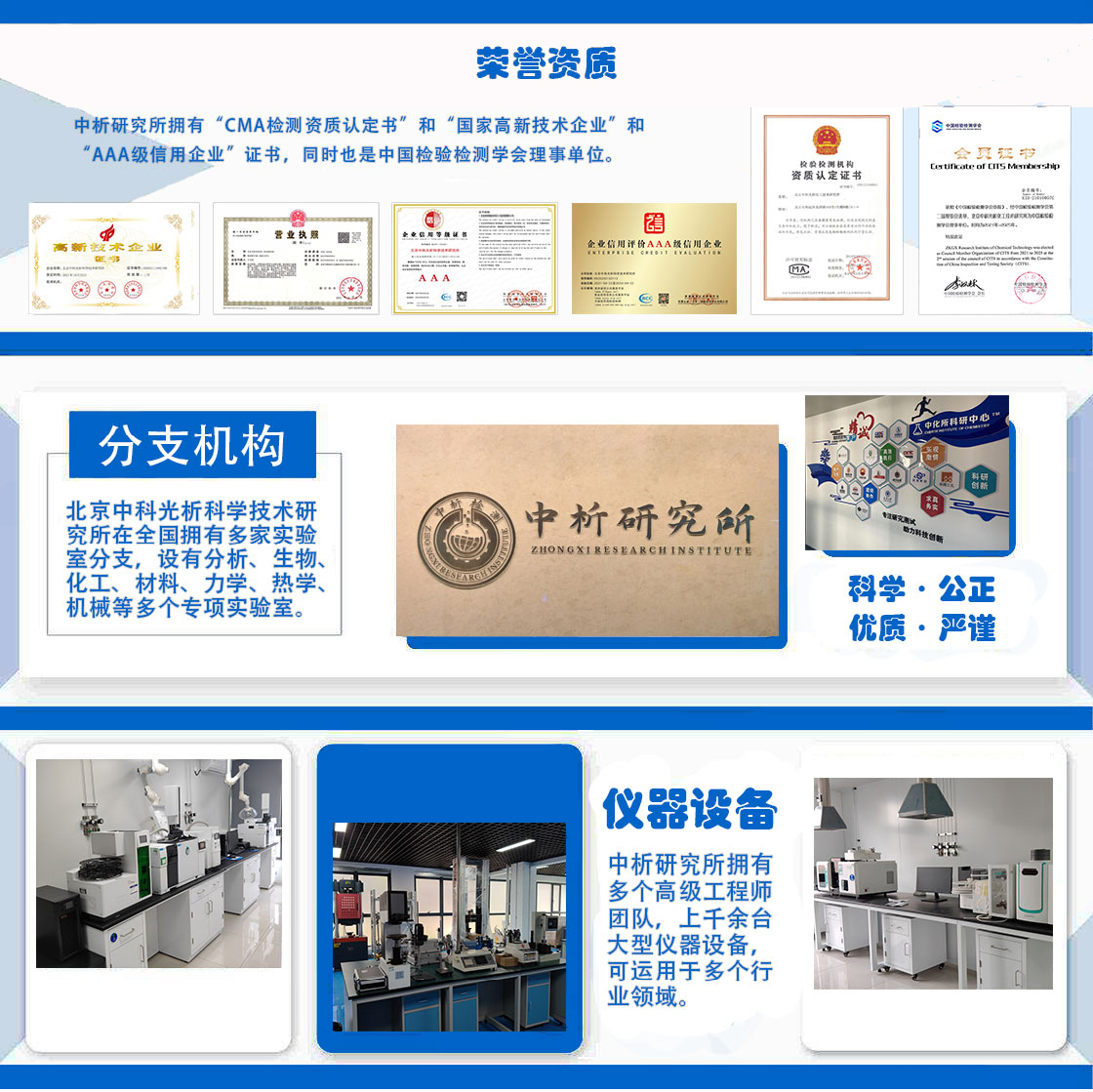
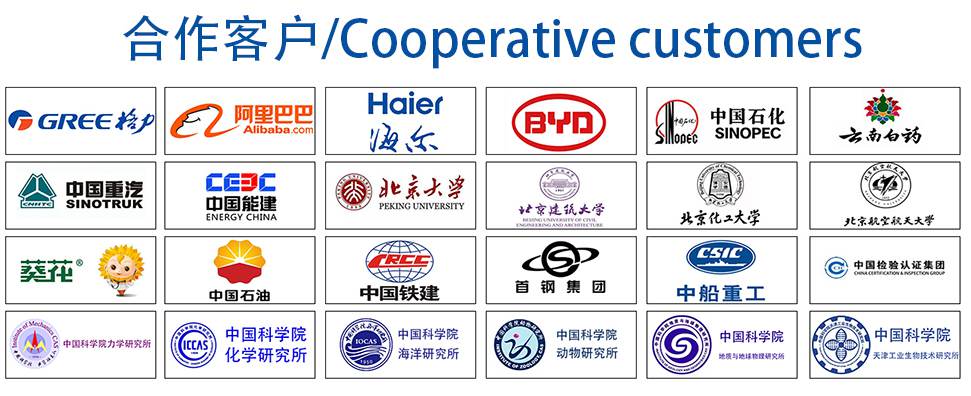