汽车与挂车气压控制装置检测的重要性
汽车与挂车的气压控制装置是保障车辆安全运行的核心系统之一,广泛应用于制动系统、悬挂系统及辅助设备(如气动门控装置)中。该装置通过压缩空气的储存、分配和压力调节,确保车辆在行驶、制动和装卸过程中保持稳定性和可靠性。由于气压系统的故障可能导致制动失效、悬挂异常甚至重大交通事故,因此对其性能的定期检测与维护至关重要。根据《机动车运行安全技术条件》(GB 7258)及行业标准要求,气压控制装置的检测需涵盖密封性、响应速度、压力稳定性等多项关键指标,以确保符合国家法规和实际使用需求。
检测项目一:气密性测试
气密性是气压控制装置的核心检测指标。通过专用气压表与泄漏检测仪,对储气罐、管路、阀体及连接部位的密封性进行静态与动态测试。静态测试要求在额定压力下保压5分钟,压力下降不得超过10kPa;动态测试需模拟实际工况,检测制动频繁操作时的压力波动是否超出允许范围。发现泄漏点需立即修复,避免空气流失导致制动力不足。
检测项目二:压力响应速度检测
压力响应速度直接影响制动系统的灵敏性。通过设备记录气压从0升至额定工作压力(通常为8-10bar)所需时间,同时测试紧急制动时气压释放速度是否符合标准(如GB 12676要求)。对挂车气压控制装置还需验证牵引车与挂车之间的压力同步性,确保制动动作无延迟,防止拖拽失控。
检测项目三:安全阀与调压阀校准
安全阀是防止气压过载的最后屏障,需检测其开启压力是否与标定值一致(误差不超过±5%),并在超压后能否自动复位。调压阀的检测包括输出压力精度测试(如稳压偏差≤0.2bar)和异常工况下的失效保护功能验证,确保系统压力始终处于安全范围。
检测项目四:管路与接头耐久性检查
针对气压管路的老化、磨损及接头松动问题,需进行目视检查与机械强度测试。使用内窥镜探测管路内部腐蚀情况,并通过震动台模拟车辆颠簸环境,验证接头抗疲劳性能。对橡胶软管需检测其耐压能力(爆破压力≥4倍工作压力)和抗臭氧老化特性,防止突发性破裂。
检测项目五:电控系统功能验证
现代气压控制装置多集成电子控制单元(ECU),需通过诊断仪读取故障码,测试压力传感器、电磁阀及ABS/EBS系统的协同工作能力。重点验证紧急制动信号触发时,ECU能否准确调节气压分配,并检查CAN总线通信是否稳定,避免电控失效导致机械部件误动作。
检测项目六:环境适应性测试
针对极端温度、湿度环境对气压系统的影响,需进行高低温循环试验(-40℃~80℃)与盐雾腐蚀测试。检测橡胶密封件在低温下的脆化风险,以及金属部件在潮湿环境下的防锈性能,确保装置在不同气候条件下均能可靠工作。
检测项目七:挂车连接装置专项检测
针对挂车特有的气压耦合装置(如制动接头、紧急制动管路),需测试其快速断连功能与自密封性能。通过模拟牵引车与挂车意外分离场景,验证紧急制动管路能否在0.2秒内自动触发驻车制动,并检查耦合器的磨损量是否符合SAE J318标准。
总结
汽车与挂车气压控制装置的检测需结合机械性能、电子控制与环境适应性进行全方位评估。通过标准化检测流程,可及时发现储气罐裂纹、阀体卡滞、传感器漂移等潜在风险,从而有效预防因气压系统故障引发的安全事故,保障道路运输的高效与安全。
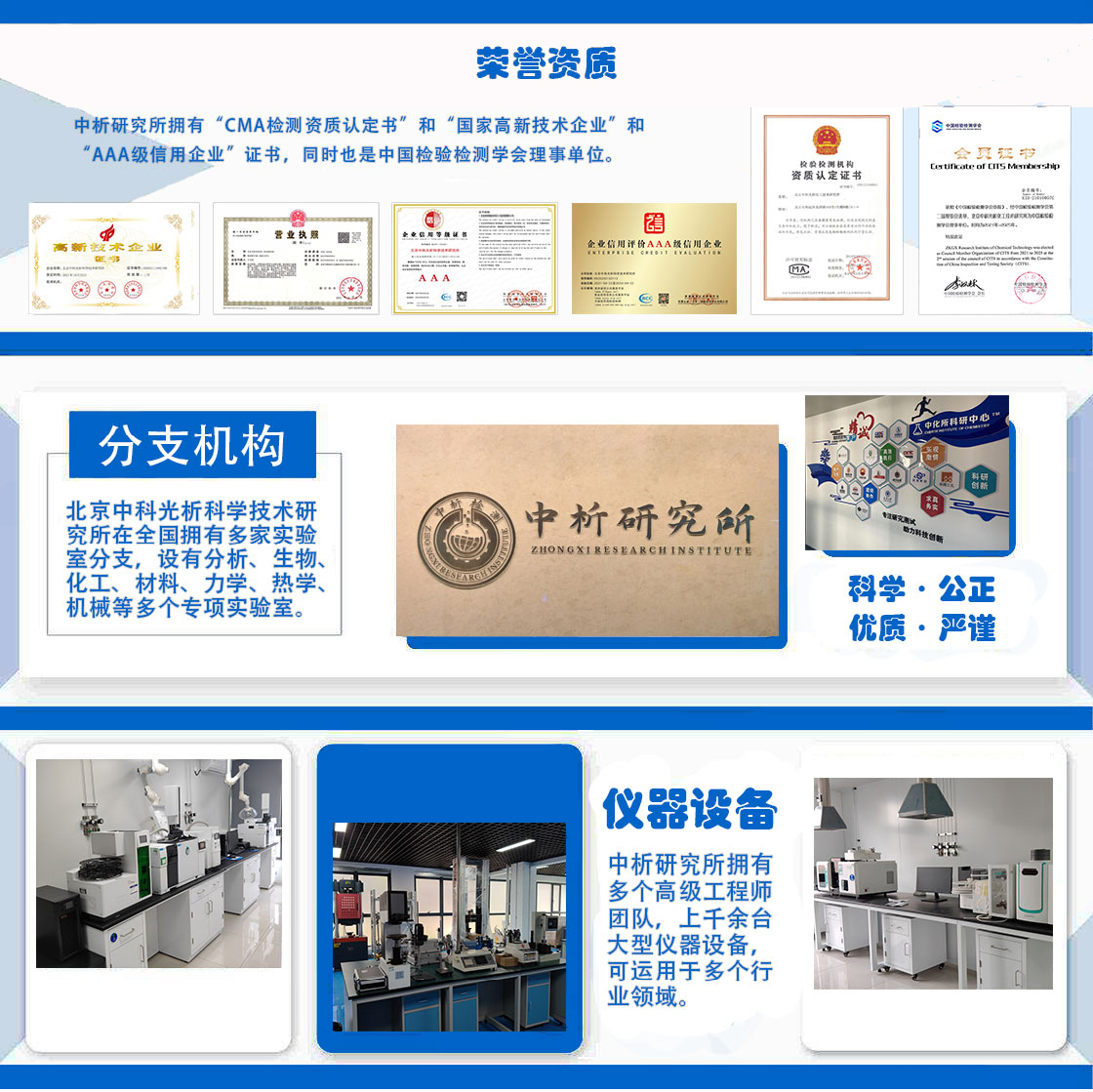
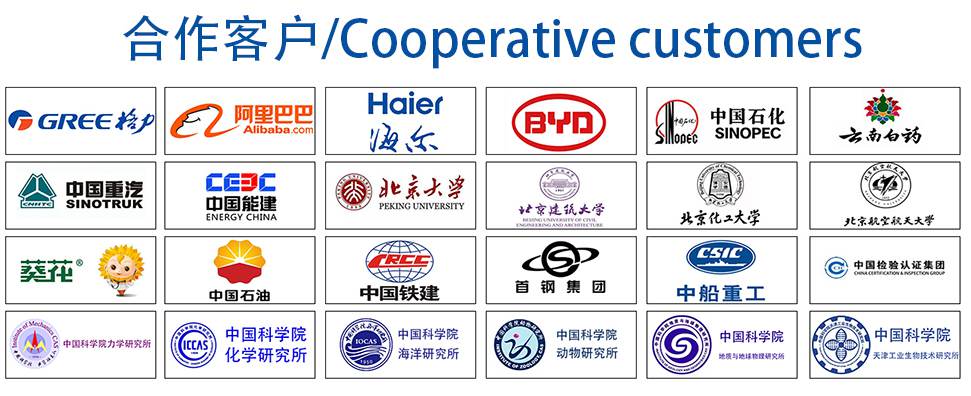