客车液力缓速器检测的重要性
液力缓速器作为客车辅助制动系统的核心部件,在长下坡或频繁制动场景中发挥着关键作用,能够有效减少传统摩擦制动器的磨损与热衰退风险,保障车辆行驶安全。随着客车运营里程的增加和环境复杂性的提升,缓速器的性能衰减、液压系统泄漏、控制逻辑异常等问题可能直接影响制动效能。因此,定期对液力缓速器进行系统性检测,既是行业法规的硬性要求,也是预防事故、延长设备寿命的核心举措。
液力缓速器检测的主要项目
1. 结构密封性检测
重点检查缓速器油路接口、散热器及液压泵的密封状态,通过加压测试观察是否出现渗漏。同时利用超声波探伤仪对壳体焊缝进行无损检测,排除裂纹或变形隐患,确保高温高压工况下的结构完整性。
2. 液压系统性能测试
使用专用诊断设备测量液压油压力、流量及油温变化曲线,验证油泵输出功率是否满足标定值。对比缓速器在不同转速下的制动力矩响应,判断是否存在内部阀体卡滞或油液污染导致的性能下降。
3. 控制系统功能验证
模拟车辆运行工况,检测ECU对缓速器的控制逻辑是否正常,包括制动档位切换、故障代码触发及CAN总线通讯状态。同时需检查手控开关、车速传感器等外围设备的信号传输稳定性。
4. 温度适应性测试
在高温(>80℃)和低温(-30℃)环境下分别运行缓速器,监测油液粘度变化对制动响应时间的影响,评估散热系统在极限温度下的工作效能,防止因过热导致制动失效。
5. 耐久性试验
通过台架连续加载试验,模拟缓速器长期高频次使用场景,统计关键部件(如叶轮、轴承)的磨损程度,分析其使用寿命是否达到行业标准(如JT/T 1178.2)。
检测依据与结果处理
检测过程需严格参照《汽车制动系统技术要求》(GB 21670)及车辆制造商技术规范。对检测中发现的不合格项目,如密封圈老化、控制阀响应延迟等,须立即更换配件并重新标定系统参数。检测完成后应生成包含原始数据、问题清单及维修建议的完整报告,作为车辆安全档案的重要组成部分。
总结
客车液力缓速器检测需要综合运用机械检测、电子诊断和工况模拟等手段,覆盖从硬件状态到软件控制的全面维度。通过科学规范的检测流程,能够显著提升客车制动系统的可靠性,为道路运输安全提供有力保障。
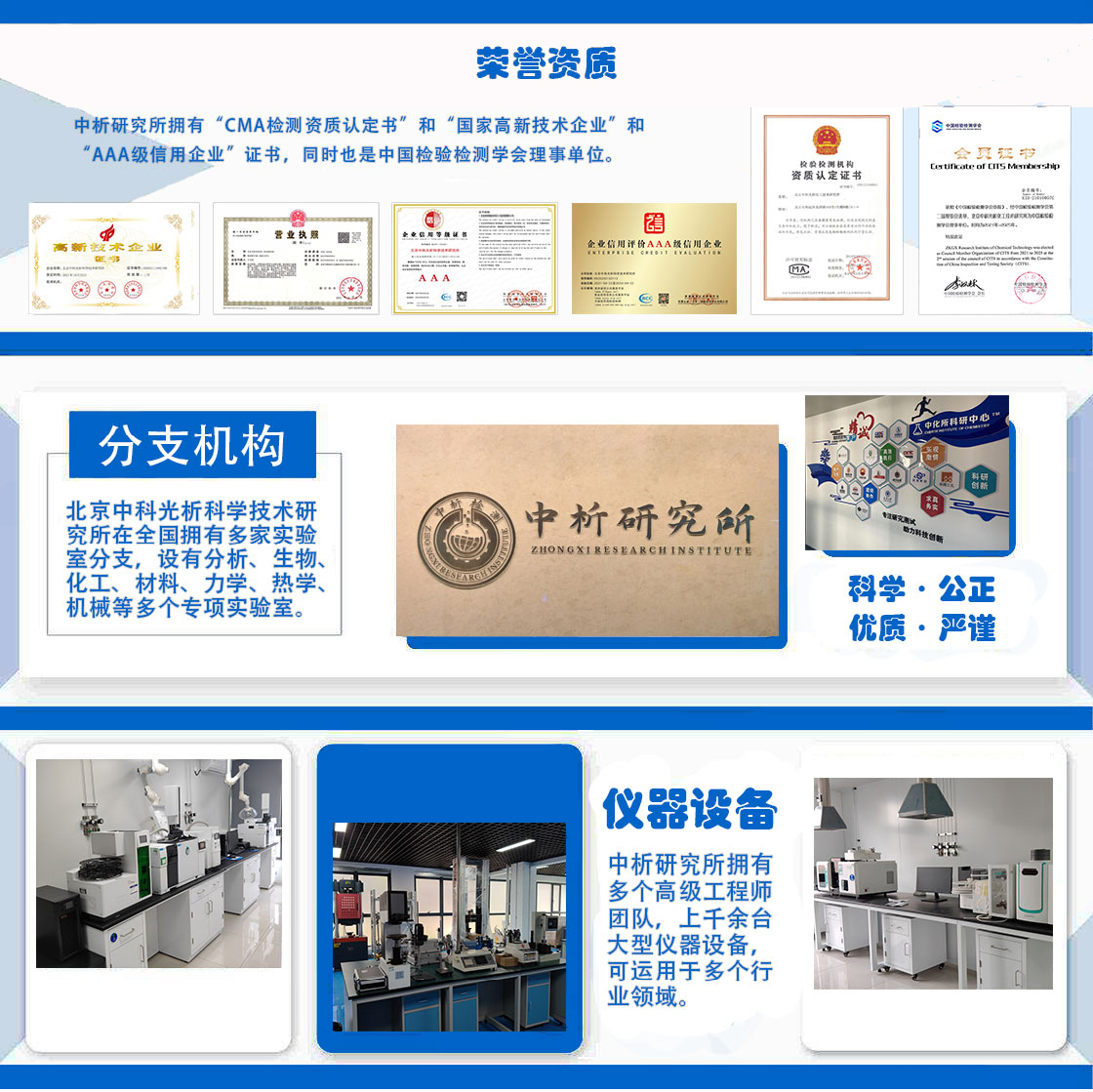
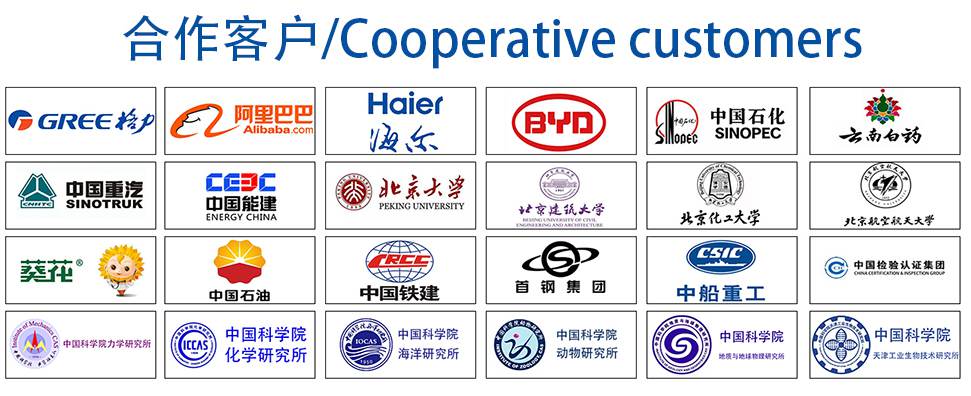