商用车辆和挂车制动系统检测的重要性
商用车辆及挂车作为公路运输的核心载体,其制动系统的可靠性直接关系到道路交通安全和人员生命财产安全。由于商用车普遍具有载重大、行驶里程长、工况复杂等特点,制动系统长期承受高负荷运行,极易因磨损、老化或部件失效导致性能下降。根据交通运输部统计数据,约23%的商用车事故与制动系统故障相关。因此,定期开展专业化的制动系统检测不仅是法规强制要求,更是预防重大交通事故的关键防线。
核心检测项目体系
1. 制动效能检测
通过滚筒式制动试验台或平板式检测仪,测量各轴制动力占总质量比例,要求空载车辆制动力总和≥60%,重点车辆(如危化品运输车)需达到≥65%。同步检测制动力平衡性,同一车轴左右轮制动力差不得超过15%。
2. 制动响应时间测试
使用专用计时装置测量制动迟滞时间,气压制动的牵引车从踏板动作到最远制动气室建立75%额定压力应≤0.6秒,挂车响应时间需≤0.4秒。电子制动系统(EBS)需验证信号传输延迟≤0.15秒。
3. 制动管路密封性检测
采用气压保持试验法,发动机停机后,双回路系统气压下降值10分钟内不得超出0.5bar,单回路系统5分钟内≤0.3bar。重点检查制动总泵、分泵、快放阀等关键部件的渗漏情况。
4. 驻车制动性能验证
在20%标准坡道上实施静态驻坡试验,车辆满载状态下需保持10分钟无移动。对鼓式制动器检测调节臂工作行程,盘式制动器测量摩擦片剩余厚度(新片厚度低于50%需更换)。
5. 辅助制动系统评估
针对缓速器、排气制动等辅助装置,在测试场地测量30km/h初速度下的减速度值,电涡流缓速器应提供≥1.5m/s²持续制动力,发动机辅助制动需满足坡度7%的控速要求。
6. 挂车制动协调性检测
使用五轮仪测试列车制动同步性,牵引车与挂车制动动作时间差应≤0.2秒。检查惯性制动系统的机械连接件磨损量,重点测量紧急继动阀的响应特性。
7. 制动热衰退试验
在台架试验中连续实施10次100km/h-0的紧急制动,记录摩擦材料温度变化曲线。要求第10次制动距离相对首次增长量不超过20%,制动器表面温度不得超过600℃。
8. 电子控制系统诊断
通过OBD接口读取ABS/EBS故障码,检测轮速传感器信号一致性(偏差<2%)。模拟单回路失效场景,验证系统能否自动调整制动力分配,确保车辆稳定性。
9. 制动液品质检测
采用红外光谱法测定DOT4制动液的含水量(需<3%),检测沸点下降幅度。对超过2年或10万公里的制动液必须进行强制更换。
10. 应急制动功能测试
在断开主制动管路条件下,验证机械式应急装置能否在5秒内建立≥30%额定制动力。检查断气保护装置能否在0.3秒内触发弹簧制动。
检测周期与标准依据
根据GB7258-2017《机动车运行安全技术条件》,营运货车应每12个月进行强制检测,危化品运输车辆检测周期缩短至6个月。检测机构需配备符合JJG906-2015要求的标定设备,检测人员必须持有特种设备检验资格证。检测数据需实时上传全国道路运输车辆技术服务系统,实现全生命周期管理。
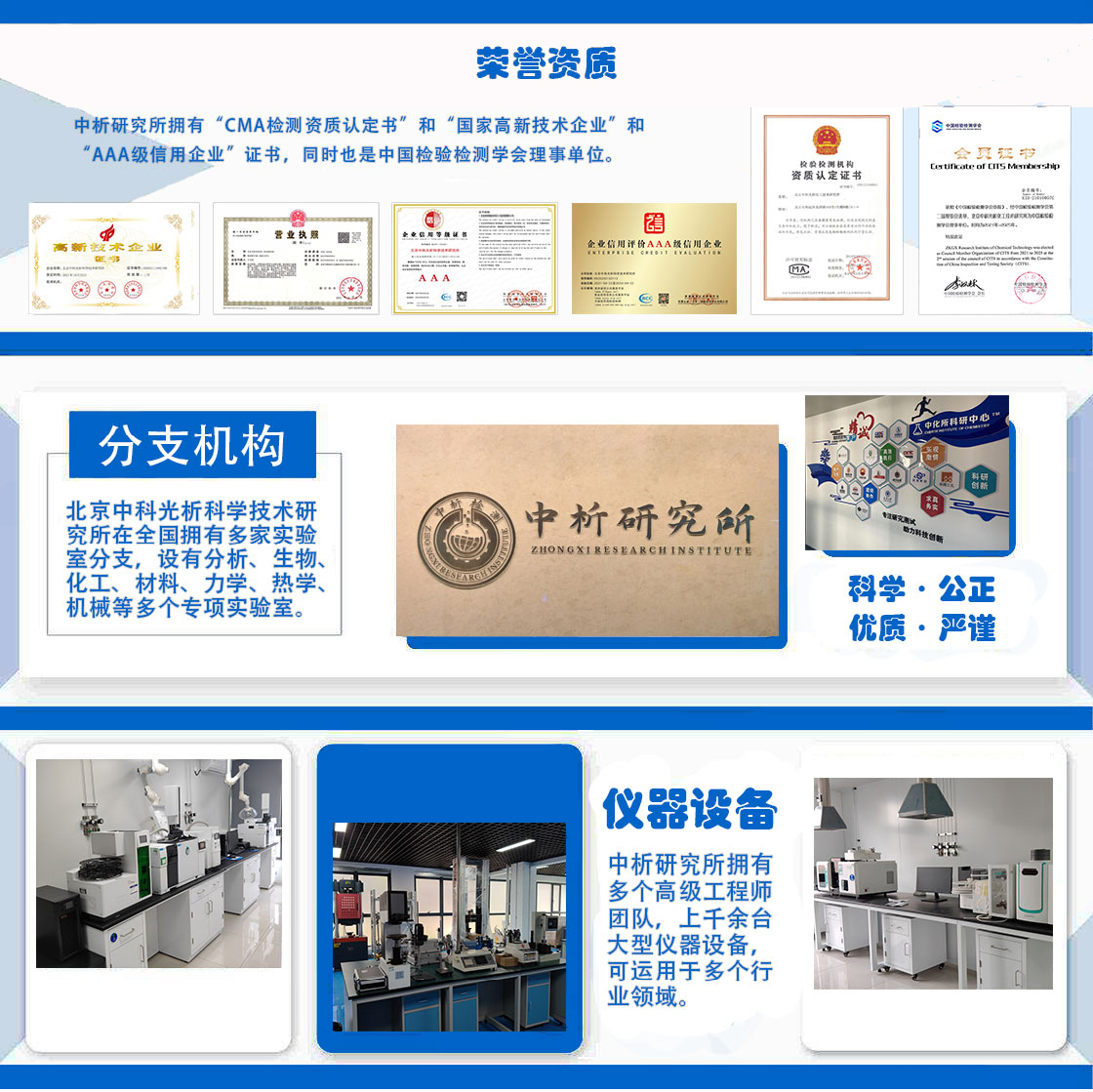
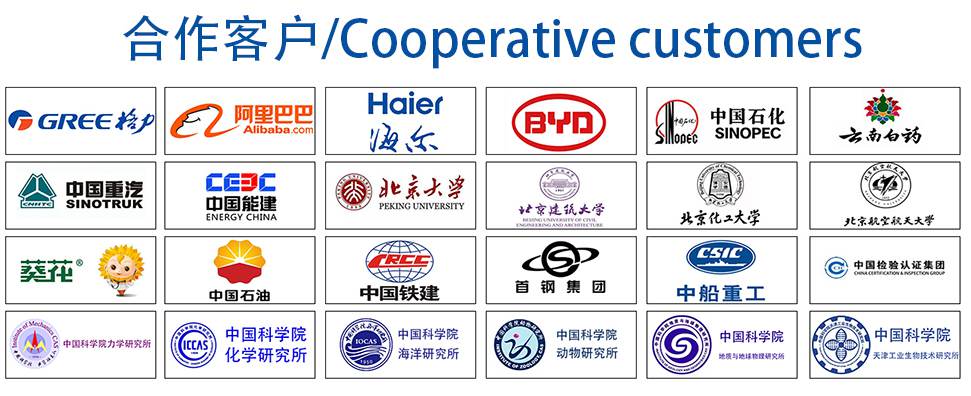