高度疲劳荷载钢结构焊接检测的核心要点
在桥梁、高压输电塔、大型工业设备等承受高频动荷载的钢结构中,焊接部位的质量直接关系到整体结构的抗疲劳性能。随着荷载循环次数的增加,焊缝及热影响区可能产生微小裂纹的萌生与扩展,最终引发灾难性失效。因此,针对高度疲劳荷载条件下的钢结构焊接质量检测,需采用多维度、高精度的检验技术体系,涵盖从材料性能到服役状态的全生命周期监测。
关键检测项目清单
1. 焊缝无损检测组合:采用UT(超声波探伤)与PAUT(相控阵超声)定位内部缺陷,配合磁粉检测(MT)筛查表面裂纹,X射线衍射(XRD)分析残余应力分布。对于复杂节点实施工业CT扫描,建立三维缺陷模型。
2. 材料性能验证:通过显微硬度测试确定HAZ硬化程度,夏比冲击试验评估低温韧性,金相分析确认微观组织是否符合AWS D1.1标准,光谱检测确保焊材成分匹配性。
3. 疲劳特性专项测试:开展高频疲劳试验机模拟实际荷载谱,采用DIC(数字图像相关)技术捕捉裂纹萌生过程,运用断裂力学计算临界裂纹尺寸,建立S-N曲线数据库。
4. 服役状态监测:安装光纤光栅传感器网络实时监测应力变化,运用声发射技术捕捉裂纹扩展信号,结合无人机搭载热成像仪进行定期巡检,构建结构健康监测(SHM)系统。
质量控制技术延伸
齐全检测需融合数字孪生技术,将检测数据与BIM模型动态关联,通过机器学习算法预测剩余寿命。严格执行EN 1993-1-9疲劳设计规范,对关键焊缝实施概率断裂力学分析(PFMA),同时建立全焊接参数追溯系统,确保每个节点的工艺合规性。
这类检测不仅需要符合ISO 5817焊接质量标准,更要关注ASTM E647疲劳裂纹扩展速率测试等专项指标。通过多尺度检测技术的协同应用,可有效提升高度疲劳荷载钢结构的服役安全系数,降低全生命周期维护成本。
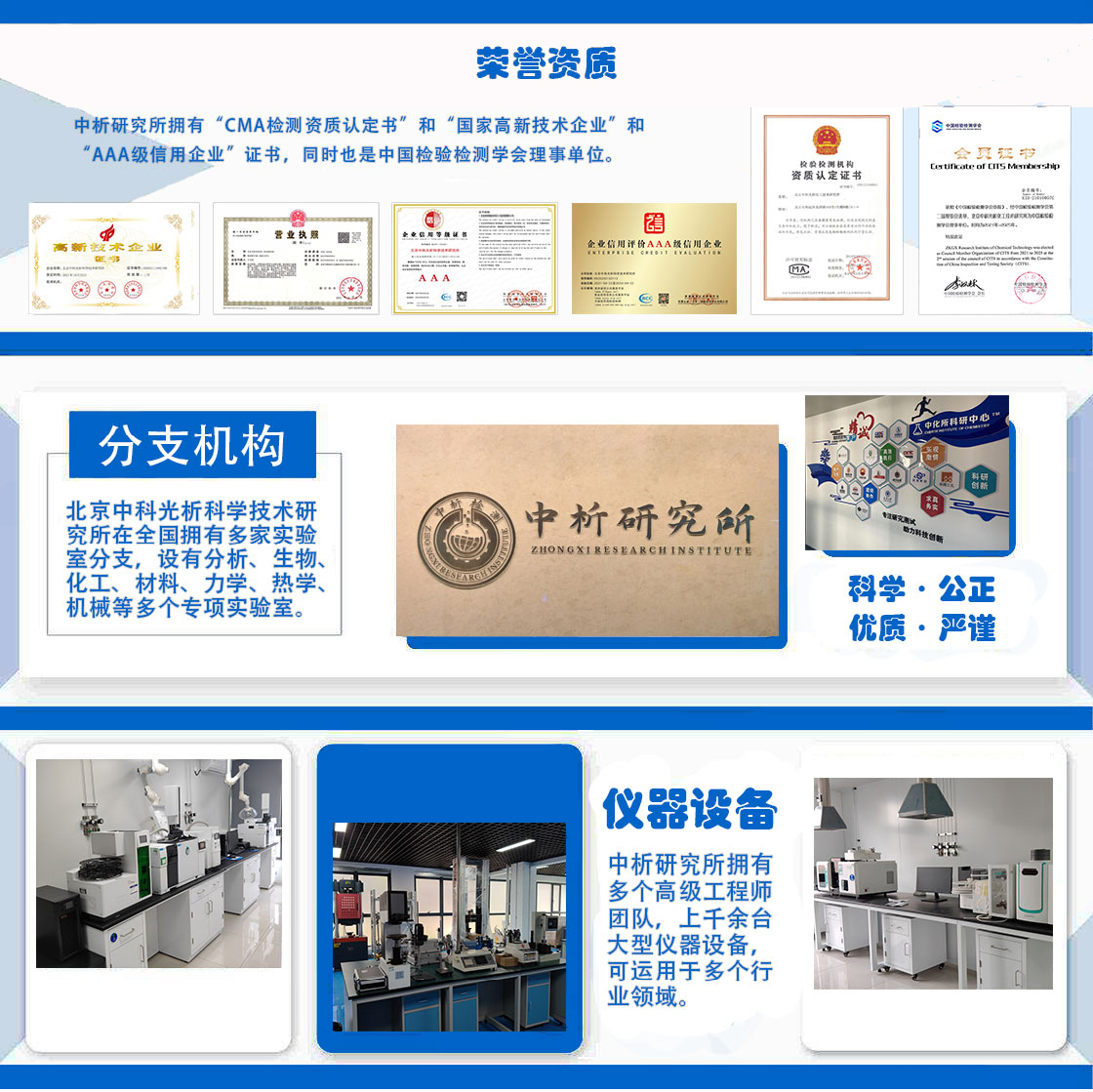
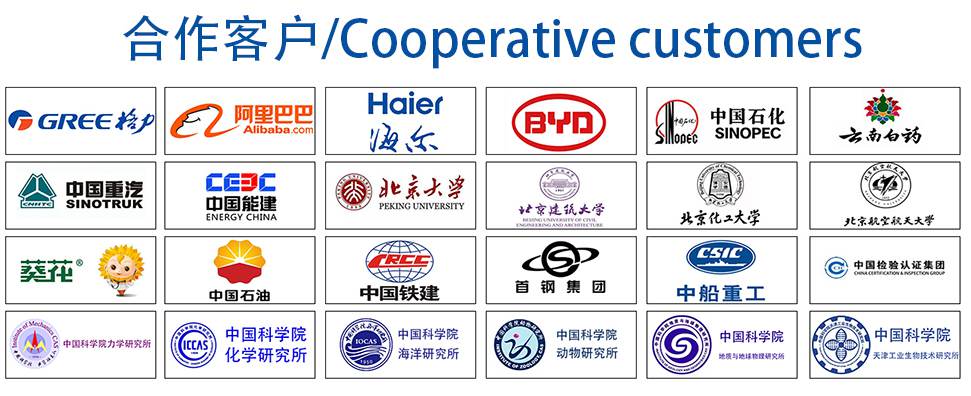