结构钢焊接检测的重要性与检测体系
在建筑、桥梁、压力容器等工程领域,结构钢焊接质量直接影响着整体工程的安全性与使用寿命。焊接过程中可能存在的未熔合、气孔、裂纹等缺陷,若未被及时发现,将导致结构强度下降、应力集中等问题,严重时可能引发灾难性事故。根据GB 50661《钢结构焊接规范》和AWS D1.1《钢结构焊接规范》要求,建立完整的焊接质量检测体系包含六大核心检测模块,通过多维度技术手段确保焊缝质量符合设计标准。
主要检测项目及技术要点
1. 外观质量检测
使用10倍放大镜与焊缝检验尺进行目视检测,重点检查焊缝余高(0-3mm)、焊脚尺寸偏差(±1.5mm)、咬边深度(≤0.5mm)、表面裂纹等缺陷。特别关注T型接头角焊缝的焊喉厚度,需达到钢板厚度的0.7倍以上。记录焊缝表面气孔直径(单个≤3mm,总长≤焊缝长度5%)并评估表面成形质量。
2. 无损检测技术应用
包括超声波检测(UT)、射线检测(RT)、磁粉检测(MT)、渗透检测(PT)四大方法:
• 超声波检测采用2-5MHz探头,可发现≥Φ2mm的埋藏缺陷,适用于厚度8-400mm的对接焊缝
• 射线检测按NB/T 47013标准评定,II级合格要求单个气孔≤4%壁厚且密集气孔区≤20mm
• 磁粉检测灵敏度达0.1mm,可检出表面及近表面裂纹
• 渗透检测用于非磁性材料表面开口缺陷检测,观察时间控制在10-30分钟
3. 力学性能试验
按GB/T 2650-2654系列标准执行:
• 拉伸试验:测得焊缝抗拉强度不低于母材标准值的下限,断后伸长率≥20%
• 弯曲试验:180°侧弯试验后,试样受拉面裂纹长度≤3mm
• 冲击试验:-20℃条件下KV2值≥34J(Q345钢),取样位置包含焊缝中心、熔合线、热影响区
4. 化学成分分析
采用光谱分析仪检测焊缝金属的C、Mn、Si、S、P五大元素含量,碳当量Ceq需控制在0.45%以下(IIW公式)。重点关注S、P含量(≤0.035%),避免产生热裂纹。异种钢焊接时需检测Cr、Ni、Mo等合金元素的稀释率。
5. 宏观与微观检验
通过金相显微镜(100-500倍)分析:
• 宏观检验:刻槽试样检测熔深、熔合比,要求根部熔深≥2mm
• 微观检验:观察焊缝区柱状晶形态,热影响区粗晶区宽度≤0.5mm,无马氏体异常组织
6. 几何尺寸检测
使用激光扫描仪或三维坐标测量:
• 直线度偏差≤L/1000且≤5mm
• 角变形量≤3°或高度差≤2mm/m
• 错边量≤10%板厚且≤2mm
• 焊后整体尺寸公差±3mm(跨度≤30m时)
现代检测体系已融合数字化技术,如相控阵超声波、DR数字射线实时成像、焊接过程监控系统等,实现了从"结果检测"到"过程控制"的转变。检测人员需持有特种设备检验人员证书(UT/RT II级),严格执行工艺评定(PQR)和焊接工艺规程(WPS),确保检测数据的可追溯性和可靠性。
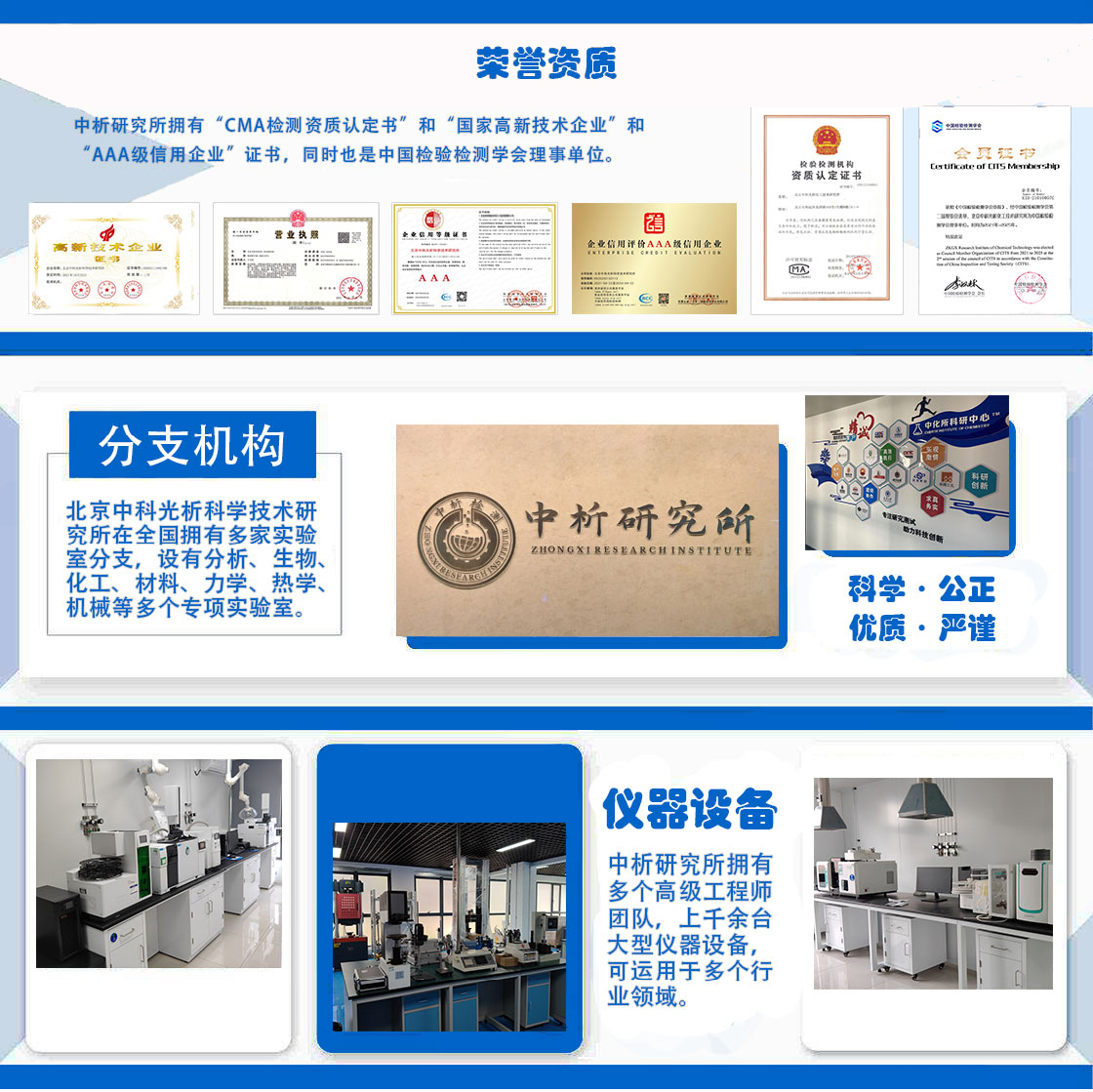
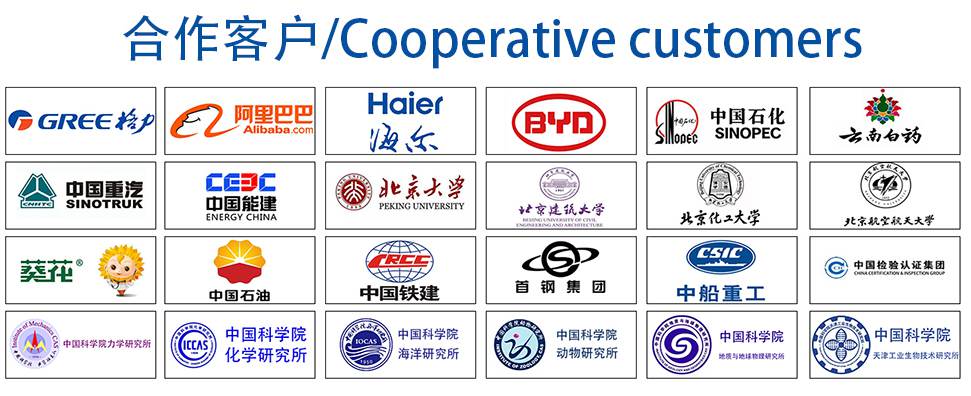