煤矿重要用途钢丝绳检测的重要性
在煤矿生产中,钢丝绳作为提升系统、运输设备及安全装置的核心部件,承担着人员、物料及设备的吊运任务,其性能直接关系到矿井作业的安全性和生产效率。由于煤矿环境复杂(高湿度、腐蚀性气体、重载荷冲击等),钢丝绳长期处于高强度磨损和疲劳状态,一旦出现断丝、变形或强度下降等问题,可能引发重大安全事故。因此,定期对钢丝绳进行系统性检测,是保障煤矿安全运行的必要措施。
核心检测项目及技术要求
1. 结构完整性检测
通过目视检查与仪器辅助,分析钢丝绳的捻距均匀性、绳股变形及外层钢丝排列状态。重点排查局部压扁、扭曲等结构异常,同时使用游标卡尺测量直径变化率,若直径缩减超过公称直径的7%(依据GB/T 34198-2017标准),需立即更换。
2. 断丝与磨损量化评估
采用磁粉探伤仪或超声波检测仪对表层和内部断丝进行定位统计。针对不同用途钢丝绳设定阈值:如提升人员用绳单捻距内断丝数不得超过5%,且同一截面断丝比例需低于10%。同时利用表面轮廓仪分析磨损深度,结合润滑状态评估磨损类型(如机械磨损或腐蚀磨损)。
3. 力学性能试验
通过拉伸试验机测定钢丝绳破断拉力,确保其实际破断力不低于标称值的90%。动态载荷测试则模拟运行中冲击载荷,检测应力集中区域的抗疲劳性能,记录伸长率变化曲线,预判潜在断裂风险。
4. 腐蚀与锈蚀等级判定
采用化学试剂法(如硫氰酸钾显色)检测内部腐蚀程度,结合硬度计测量钢丝表面硬度衰减值。对锈蚀面积占比超过30%或存在深度点蚀的区段,需进行局部更换或整体报废处理。
智能检测技术应用趋势
当前煤矿行业正逐步推广基于AI图像识别的在线监测系统,配合电磁感应传感器实时采集钢丝绳应力数据。通过建立数字孪生模型,可预测剩余使用寿命并实现故障预警,将传统定期检测升级为动态健康管理,显著降低突发断裂风险。
检测周期与维护规范
根据《煤矿安全规程》要求,提升人员钢丝绳应每6个月进行强制检测,物料运输绳检测周期不超过12个月。日常维护需重点关注绳端固定装置的变形情况,并建立每班次润滑记录,确保油脂渗透至绳芯。对于检测中发现局部损伤的钢丝绳,禁止采用焊接修补等临时措施,必须按标准进行科学处置。
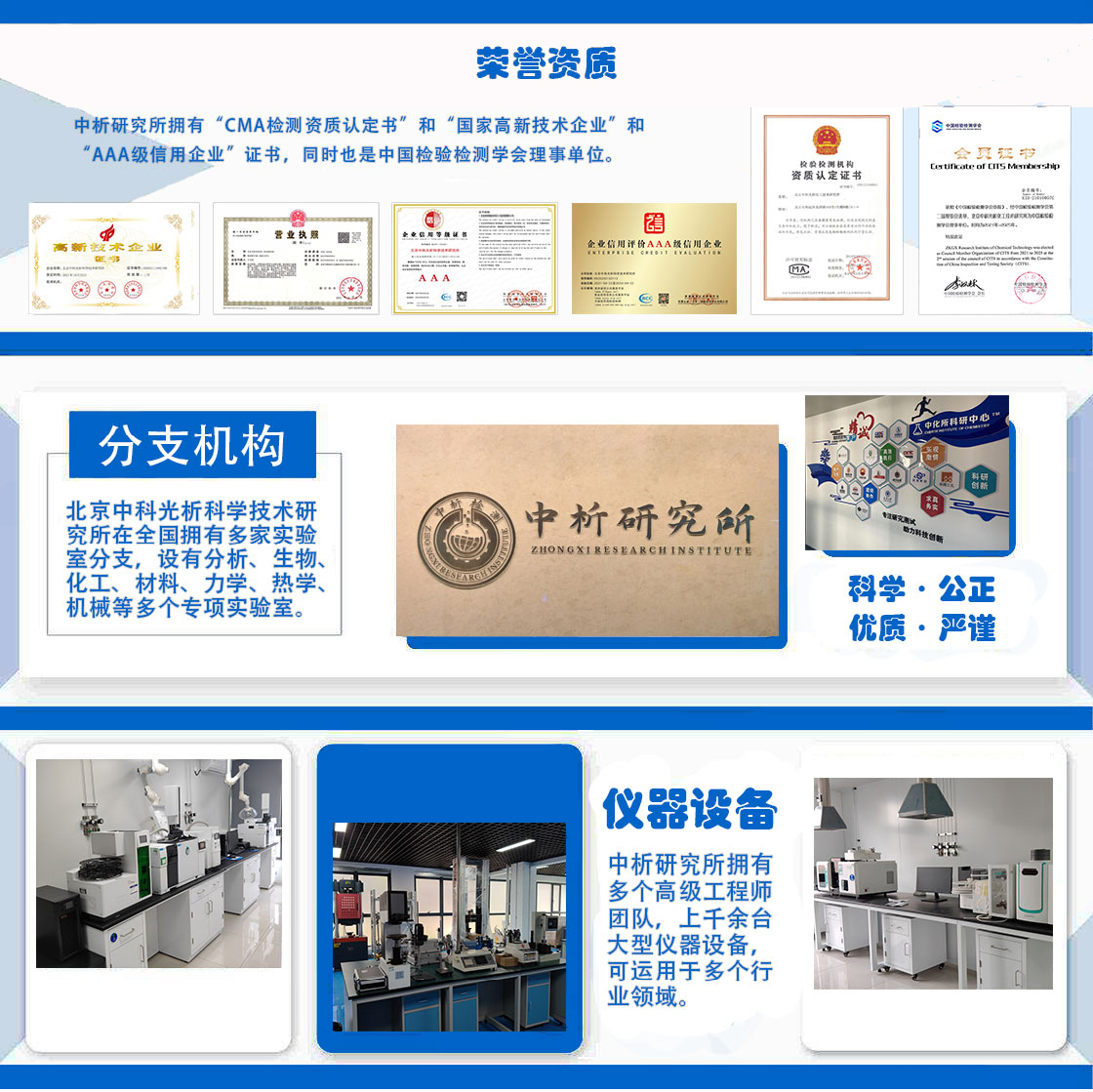
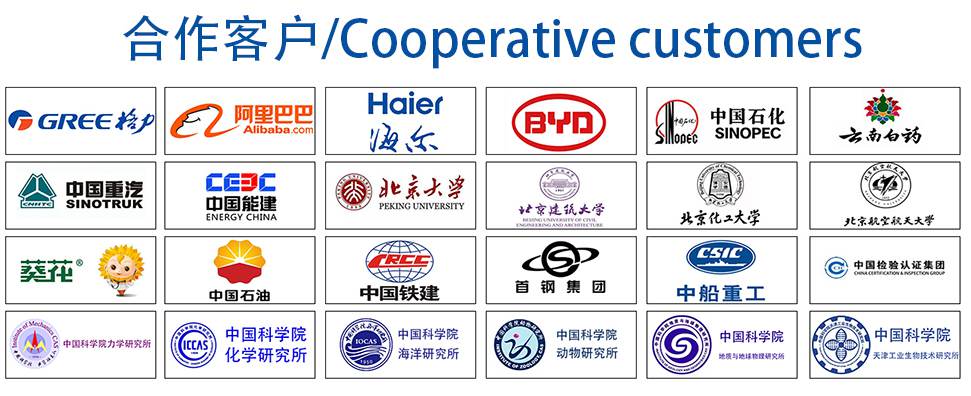