叉车检测项目全解析:保障安全运行的必备流程
叉车作为工业生产和物流仓储领域的核心搬运设备,其安全性和稳定性直接关系到人员安全和作业效率。根据《场(厂)内专用机动车辆安全技术规程》要求,叉车必须通过定期检测与强制性年检方可投入使用。专业化的叉车检测项目涵盖机械性能、安全装置、动力系统等关键环节,通过系统性检查可有效预防因设备故障引发的倾覆、失控等事故,同时延长设备使用寿命。
核心检测项目分类及标准
1. 动力系统专项检测
包含发动机/电动机输出功率测试、液压系统压力校验、传动装置磨损分析等项目。重点检查液压油管是否存在渗漏、起升链条是否达到安全余量(磨损不超过10%),以及变速箱换挡平顺性。电动叉车还需进行电池容量检测与充电系统绝缘测试。
2. 安全装置功能性验证
- 载荷保护装置:测试额定载重1.1倍时的自动限位功能
- 声光报警系统:验证倒车提示音≥85分贝、警示灯可视距离>15米
- 紧急制动装置:检测手柄触发后0.5秒内实现全制动
- 门架倾斜保护:校验前倾角≤6°、后倾角≤12°的机械限位
3. 关键结构件完整性评估
使用超声波探伤仪对货叉根部进行裂纹检测,测量货叉尖端厚度(磨损量需<原尺寸10%)。轮胎检测包含花纹深度(充气轮胎≥3.2mm,实心胎≥2mm)、轮毂螺栓预紧力测试(扭矩误差±5%)。转向系统需检查方向盘自由转角≤15°,全转向力≤30N·m。
特殊工况下的附加检测要求
对于冷库用叉车,需增加低温密封性测试(-25℃持续4小时无泄漏);防爆型叉车需通过Ex认证机构的气密性检测与电气元件防爆测试。改装叉车必须重新进行载荷曲线验证,确保重心偏移量不超过设计值的5%。
检测周期与档案管理规范
新购叉车首次检测须在投入使用前完成,年检周期不超过12个月。使用单位应建立包括日常点检(班前检查)、季度维护检测、年度强制检验的三级管理体系。检测报告需保留设备全生命周期记录,关键项目数据保存期限不得少于6年。
通过实施标准化的叉车检测流程,可降低设备故障率42%以上,同时使事故发生率减少68%。建议企业选择具备TSG检验资质的专业机构,结合物联网监测技术实现实时数据采集,构建完整的叉车安全管理生态。
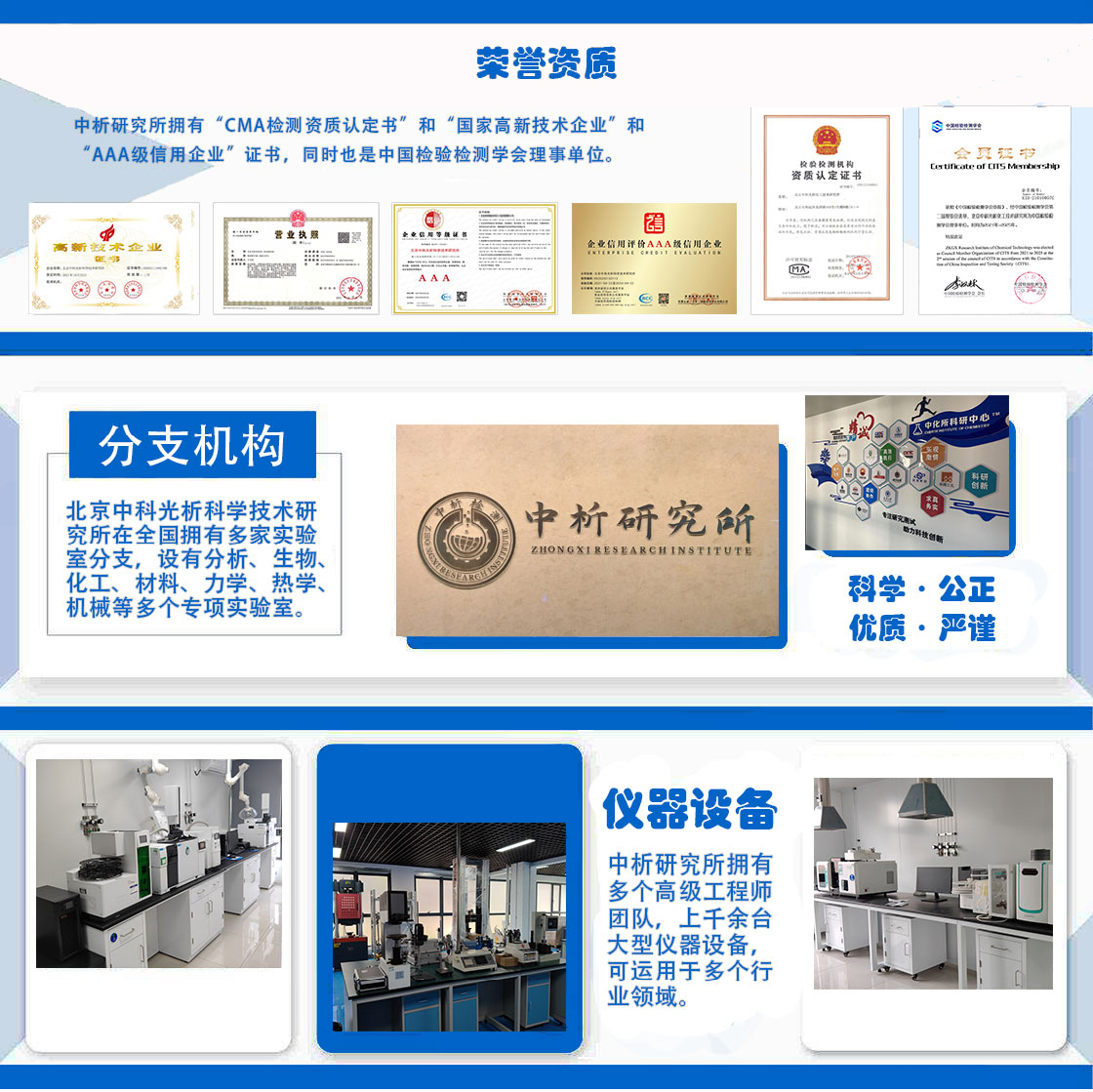
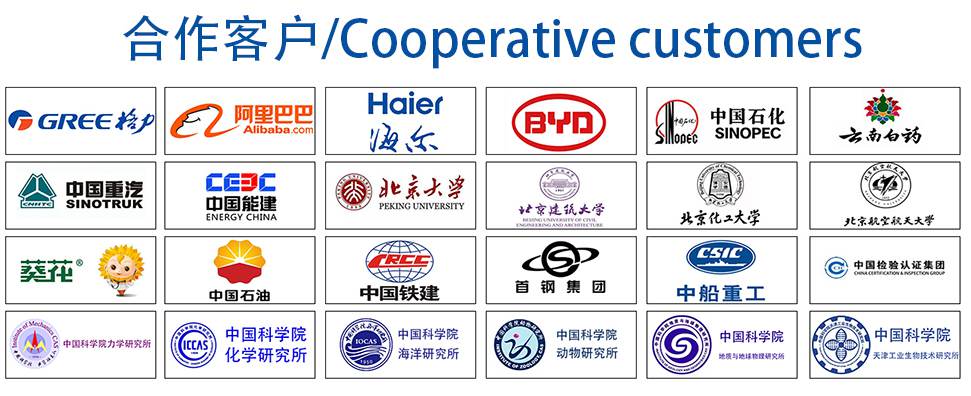