金属管材管件检测的全面解析
金属管材及管件作为工业、建筑、能源等领域的关键材料,其质量直接关系到工程安全和使用寿命。随着GB/T、ASTM、ISO等国内外标准的不断更新,金属管材管件的检测已成为生产、采购和验收过程中不可或缺的环节。通过系统化的检测项目,可有效评估材料的力学性能、化学成分、耐腐蚀性及工艺适配性,确保其在高压、高温或复杂环境下的可靠性。本文将从核心检测维度出发,深入解析金属管材管件的质量控制要点。
一、基础性能检测项目
1. 尺寸与几何精度检测
使用游标卡尺、激光测径仪及三坐标测量仪,对管材外径、壁厚、椭圆度、直线度进行测量,确保符合GB/T 21835-2020《焊接钢管尺寸及单位长度重量》等标准要求。管件需重点检测法兰孔径、螺纹精度和连接面平整度。
2. 力学性能测试
通过万能试验机完成拉伸试验(抗拉强度、屈服强度、断后伸长率)、弯曲试验和硬度测试(布氏/洛氏/维氏),验证材料是否满足ASTM A370标准。液压膨胀试验可模拟管材在极端压力下的变形能力。
二、材料特性分析项目
1. 化学成分检测
采用直读光谱仪(OES)和X射线荧光光谱仪(XRF),精确分析碳、锰、铬、镍等元素含量,比对GB/T 4336-2016标准判定材料牌号合规性,避免因成分偏差导致焊接开裂或耐蚀性下降。
2. 金相组织观测
通过金相显微镜观察晶粒度、夹杂物分布及热处理效果,依据GB/T 13298-2015评估材料微观结构是否均匀,发现过热过烧、脱碳层等缺陷。
三、环境适应性检测项目
1. 耐腐蚀性测试
采用盐雾试验(ASTM B117)、晶间腐蚀试验(GB/T 4334)和电化学工作站,模拟酸雨、海水等环境下的材料损耗速率。不锈钢管件需额外通过蓝点法检测敏化风险。
2. 低温冲击韧性试验
使用液氮制冷冲击试验机,在-40℃~-196℃条件下测试材料脆性转变温度,确保LNG管道等低温场景的使用安全。
四、无损检测与密封性验证
1. 缺陷探测技术
综合应用超声波探伤(UT)、涡流检测(ET)和工业内窥镜,定位管材内部裂纹、气孔等缺陷,检测灵敏度需达到GB/T 5777-2019规定的L2级别以上。
2. 压力密封性测试
通过水压试验(1.5倍工作压力保压10分钟)和氦气质谱检漏,验证管件连接处的密封性能,符合API 598阀门试验规范要求。
金属管材管件的质量检测贯穿原材料采购、生产过程控制及成品验收全流程。企业应根据应用场景选择检测组合方案,例如油气管道需加强腐蚀疲劳测试,而建筑结构管材则侧重尺寸精度和焊接质量。通过建立完善的检测体系,可显著降低工程事故风险,提升产品的市场竞争力。
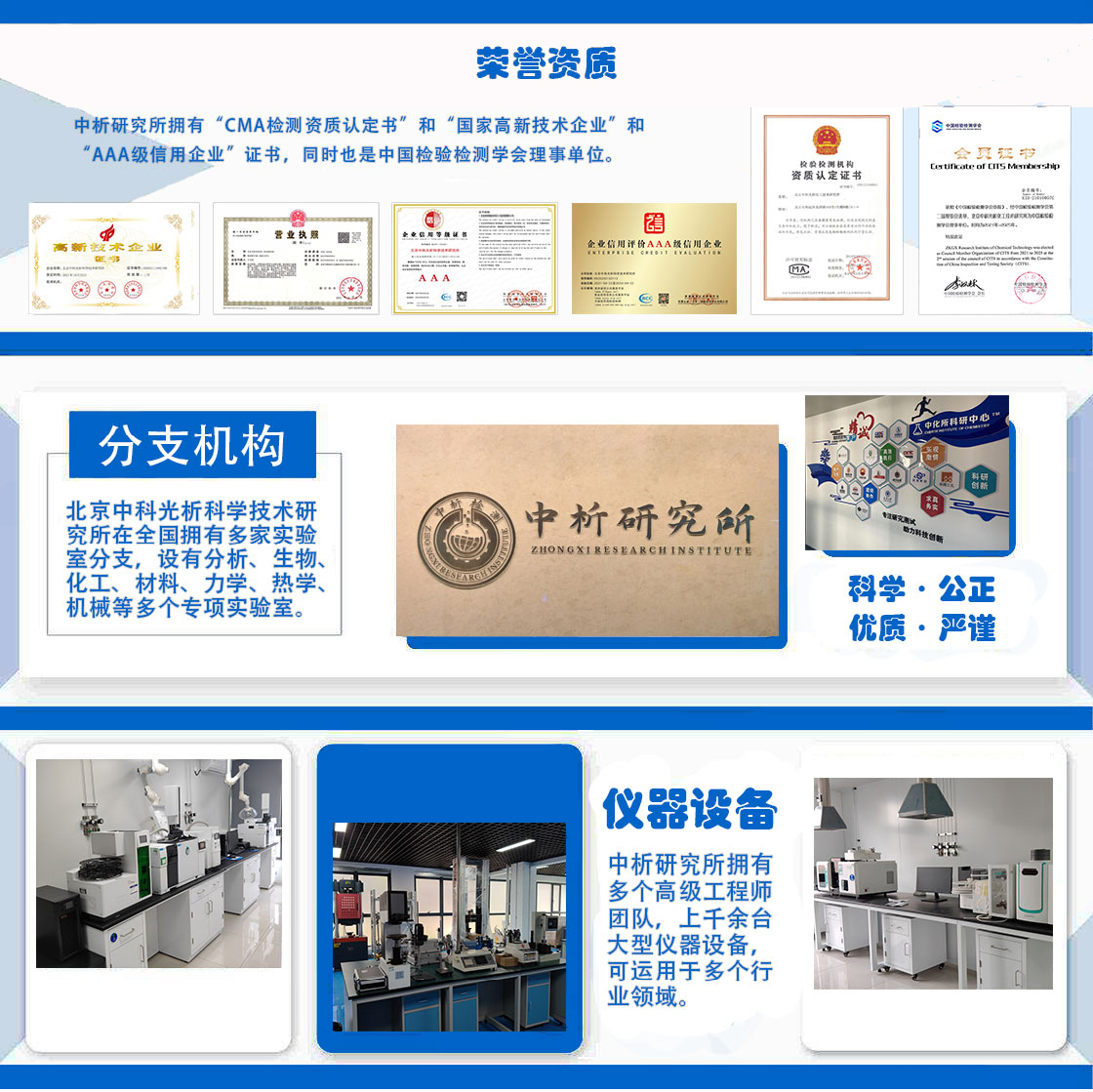
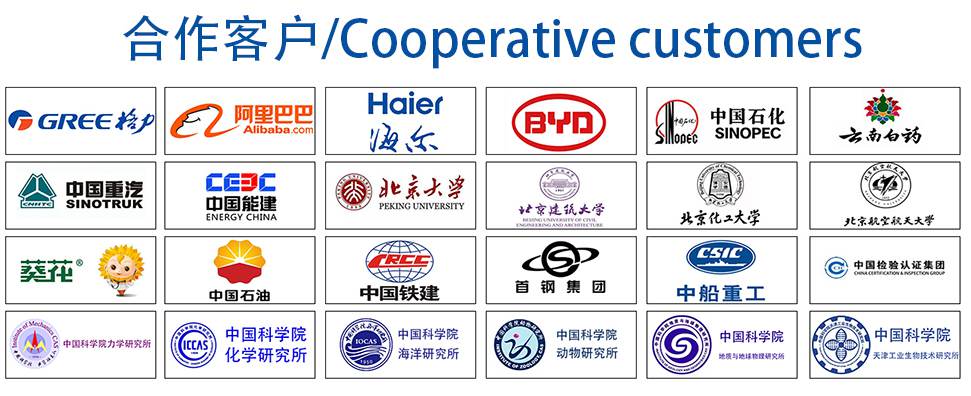