产品质量可靠性检测:保障企业核心竞争力的基石
在当今化竞争的市场环境中,产品质量的可靠性已成为决定企业生存与发展的关键要素。可靠性检测作为质量管理的核心环节,通过模拟产品在实际使用场景中的表现,系统地评估其性能稳定性、寿命周期及故障风险。从汽车零部件到消费电子,从医疗器械到工业设备,可靠性检测不仅关乎产品本身的功能实现,更直接影响品牌声誉、售后成本以及用户安全。国际标准化组织(ISO)、国际电工委员会(IEC)等机构已制定数十项检测标准,要求企业建立从设计验证到量产监控的全流程检测体系,以应对高温、振动、腐蚀等复杂环境对产品造成的潜在威胁。
核心检测项目解析
1. 环境适应性测试
通过温湿度循环试验(-40℃~85℃)、盐雾腐蚀测试(ASTM B117)、IP防护等级验证等项目,评估产品在极端气候或特殊工况下的耐受能力。例如新能源汽车电池需通过200次高低温冲击测试以验证热管理系统的可靠性。
2. 寿命加速老化试验
采用MTBF(平均无故障时间)计算模型,结合HALT(高加速寿命试验)技术,在短时间内模拟产品数年使用损耗。某品牌服务器经500小时85℃高温老化测试后,硬盘故障率下降37%,充分体现该检测的价值。
3. 机械应力测试
包含振动测试(ISTA 3A标准)、跌落测试(1.2m多角度跌落)、疲劳强度试验等,重点关注产品结构设计缺陷。工业机器人关节部件需完成10万次往复运动测试,确保传动系统寿命达标。
4. 电性能可靠性验证
通过静电放电测试(IEC 61000-4-2)、浪涌抗扰度试验、电源波动模拟等,评估电子设备在电磁干扰环境中的稳定性。智能家居产品须通过±8kV接触放电测试,方可在欧洲市场获得CE认证。
数字化检测技术的突破
随着物联网与AI技术的应用,可靠性检测正经历智能化转型。基于数字孪生技术的虚拟测试可将物理检测时间缩短60%,而大数据分析能精准定位90%以上的潜在失效模式。某航空企业通过部署智能传感器网络,实现了发动机叶片应力分布的实时监测,使检测效率提升4倍。
构建全生命周期质量防线
卓越的可靠性检测体系需要贯穿产品研发、生产、交付全流程。采用FMEA(失效模式与影响分析)工具预测设计风险,结合SPC(统计过程控制)监控生产波动,最终通过ORT( Ongoing Reliability Testing)实现市场投放后的持续质量追踪。数据显示,完善实施可靠性检测的企业,其产品召回率可降低52%,客户满意度提升28%以上。
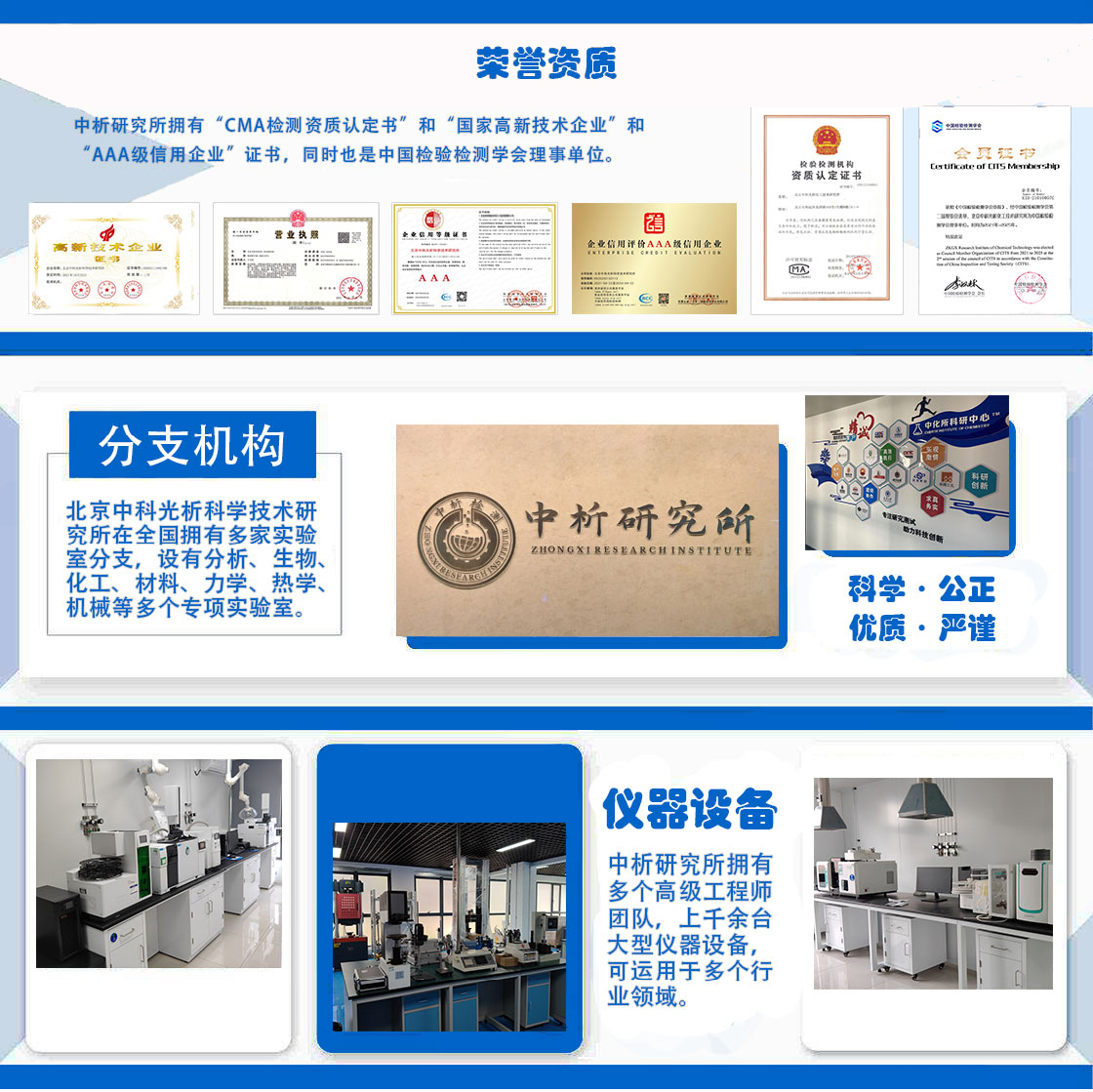
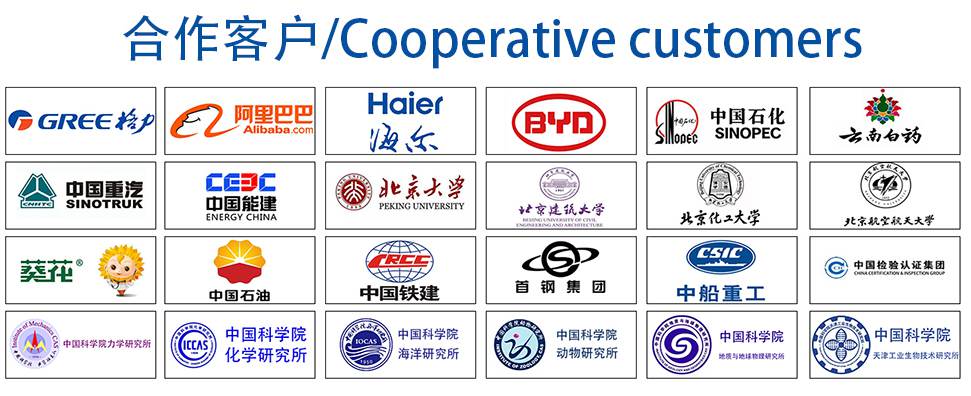