产品质量维护性检测的重要性及实施要点
在现代化工业生产和消费品制造领域,产品质量的维护性已成为衡量产品全生命周期价值的关键指标。维护性检测聚焦于产品在使用过程中保持或恢复其功能的能力,直接影响用户的运维成本、产品可用性及品牌忠诚度。据统计,维护性良好的产品可降低30%以上的全周期维护费用,同时延长设备平均使用寿命1.5-2倍。国际标准化组织(ISO 55000系列)已将维护性纳入资产管理体系要求,突显其对现代制造业的战略意义。
核心检测项目体系
1. 模块化设计评估
通过拆解分析评估产品的模块划分合理性,检测功能单元是否具备独立更换能力。重点验证模块接口标准化程度、拆装工具通用性以及故障定位隔离机制,要求单个模块更换时间不超过总维护时间的40%。
2. 故障诊断能力测试
构建典型故障模型库,考核产品自诊断系统的准确率和响应速度。包含故障代码识别、预警阈值设置、远程诊断接口等维度,要求一级故障识别准确率达到98%以上,二级故障定位时间控制在15分钟内。
3. 备件更换便捷性评估
模拟现场维护场景,量化评估备件可达性、拆装复杂度等指标。使用MTTR(平均修复时间)指标衡量,涉及操作空间设计、紧固件类型标准化、防误装结构等20余项细分参数,优质产品应实现90%常规备件单人30分钟内更换。
4. 技术文档完整性检查
系统审查维护手册、电路图册、BOM清单等技术资料的完整性和易用性。依据IEC 82079标准,重点检测故障树索引完备性、图解说明清晰度、多语言版本同步率等要素,要求关键维护步骤视频化覆盖率达100%。
5. 维护工具适配性验证
建立专用工具清单,测试标准工具套件的覆盖率及特殊工具的必要性。评估工具接口兼容性、人体工学设计等指标,优秀产品应保证85%以上维护操作使用通用工具完成。
检测方法创新趋势
随着数字孪生技术的普及,维护性检测正从物理样机测试向虚拟仿真延伸。通过构建产品的三维数字模型,可提前预测维护可达性问题,优化设计方案。行业数据显示,采用虚拟检测技术可使维护性设计迭代效率提升60%,潜在问题发现率提高45%。
维护性检测作为产品质量控制的重要环节,需要贯穿产品研发、生产、售后全流程。企业应建立包含12个一级指标、38个二级指标的评估体系,结合智能检测装备和数据分析平台,持续提升产品的可维护性水平,最终实现客户价值与企业效益的双赢。
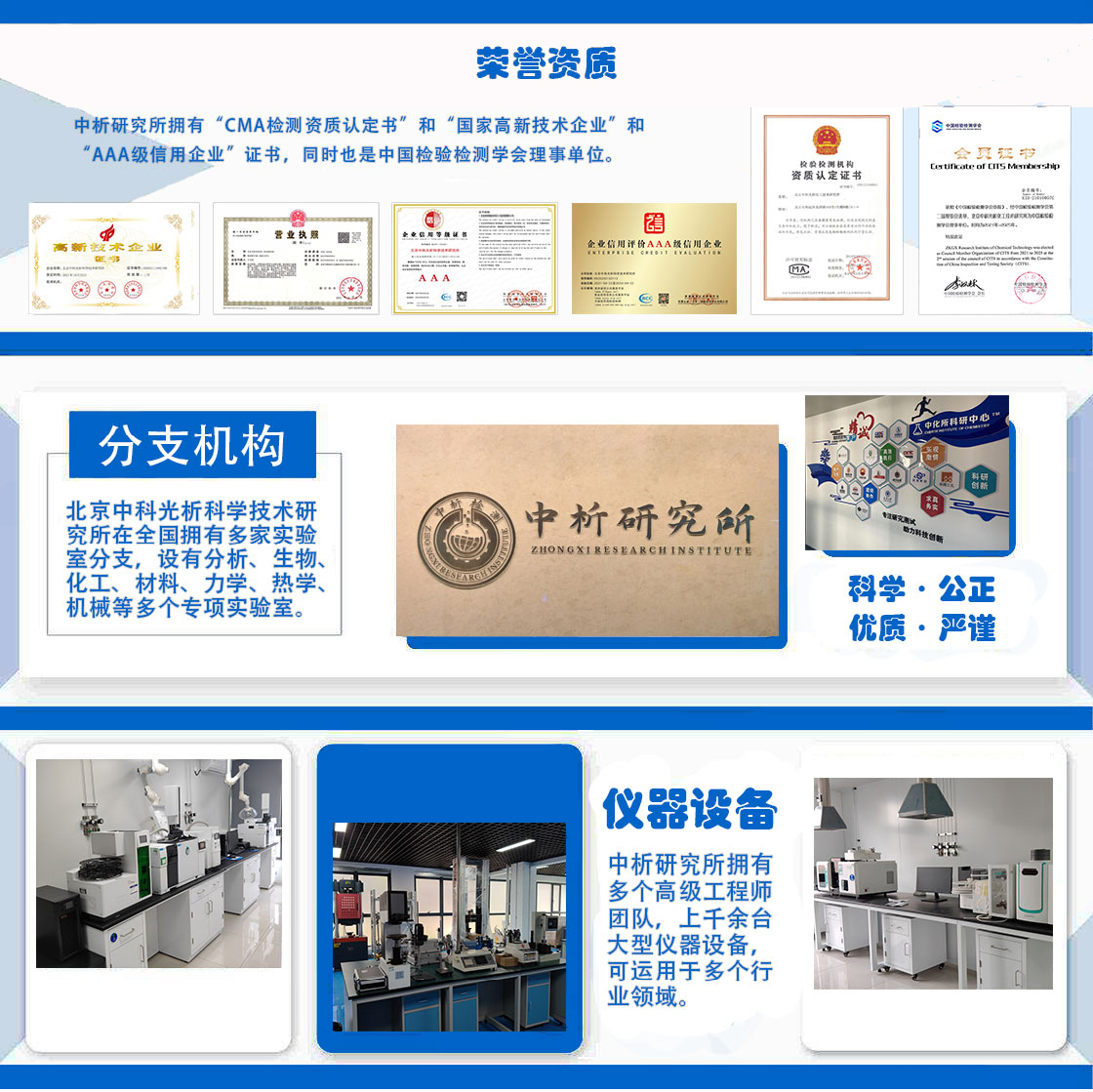
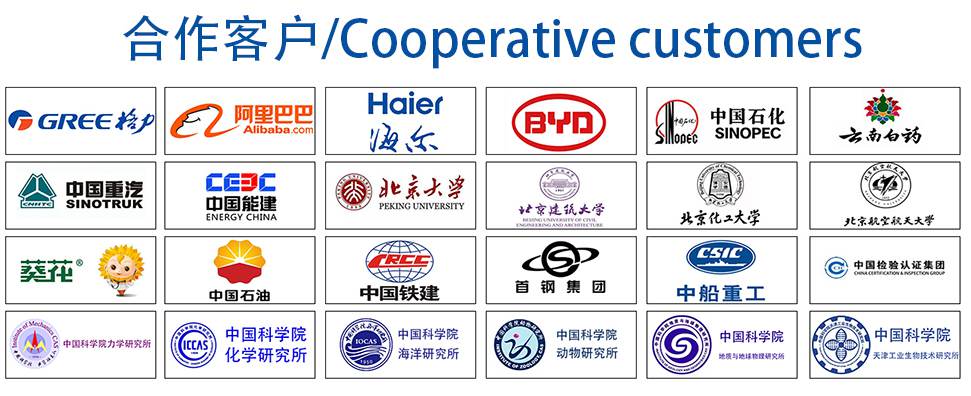