高温适应性试验检测的重要性与实施流程
在工业制造、电子设备、汽车及航空航天等领域,产品的高温适应性是衡量其可靠性和耐久性的关键指标。高温适应性试验检测通过模拟极端温度环境,验证材料、零部件或整机在高温条件下的性能稳定性、结构完整性和功能可靠性。随着气候变暖及设备运行工况的复杂化,此类检测已成为产品研发、质量控制和认证环节中不可或缺的一部分。通过科学规范的检测流程,企业能够提前发现潜在缺陷,优化设计参数,降低高温环境下的故障率,从而提升产品市场竞争力。
高温适应性试验的核心检测项目
高温适应性试验通常包含以下核心检测内容:
1. 温度梯度测试
通过高精度恒温箱或环境试验舱,对被测样品施加阶梯式升温(如25℃→50℃→75℃→100℃),监测其在不同温度节点下的性能变化。重点关注电路板焊接强度、塑料件形变阈值、润滑剂蒸发速率等参数,记录材料热膨胀系数与温度变化的关联性。
2. 高温运行耐久性测试
将样品置于额定高温环境(如85℃±2℃)连续工作500小时,实时监测关键性能指标。例如:
- 电子元器件:信号传输稳定性、功耗波动范围
- 机械设备:轴承磨损量、密封件老化程度
- 涂层材料:色差变化、附着强度衰减率
3. 热冲击试验
采用两箱式冷热冲击试验箱,模拟极端温度骤变场景(-40℃←→125℃)。每个循环包含30分钟高温暴露和15分钟快速转换,完成100次循环后检测:
- 金属件疲劳裂纹
- 复合材料层间剥离
- 电子线路虚焊脱落
- 橡胶密封件脆化失效
4. 高温环境功能验证
在模拟高温工况下进行全功能测试,包括:
- 车载ECU在发动机舱75℃环境中的通信响应时间
- 光伏逆变器在沙漠地区50℃户外条件下的转换效率
- 航空航天传感器在高速飞行时表面温度180℃的测量精度
检测标准与设备技术要求
试验需依据IEC 60068-2-2、GB/T 2423.2等国际/国家标准执行,关键设备需满足:
- 温控精度±0.5℃
- 升降温速率≥3℃/min
- 温场均匀性≤2℃(有效工作区)
- 数据采集系统采样频率≥1Hz
通过系统的检测数据与失效模式分析,企业可建立产品高温适应性的量化评价模型,为改进散热设计、优选耐高温材料提供科学依据。定期进行高温适应性复检还能监控生产工艺稳定性,确保产品全生命周期的质量一致性。
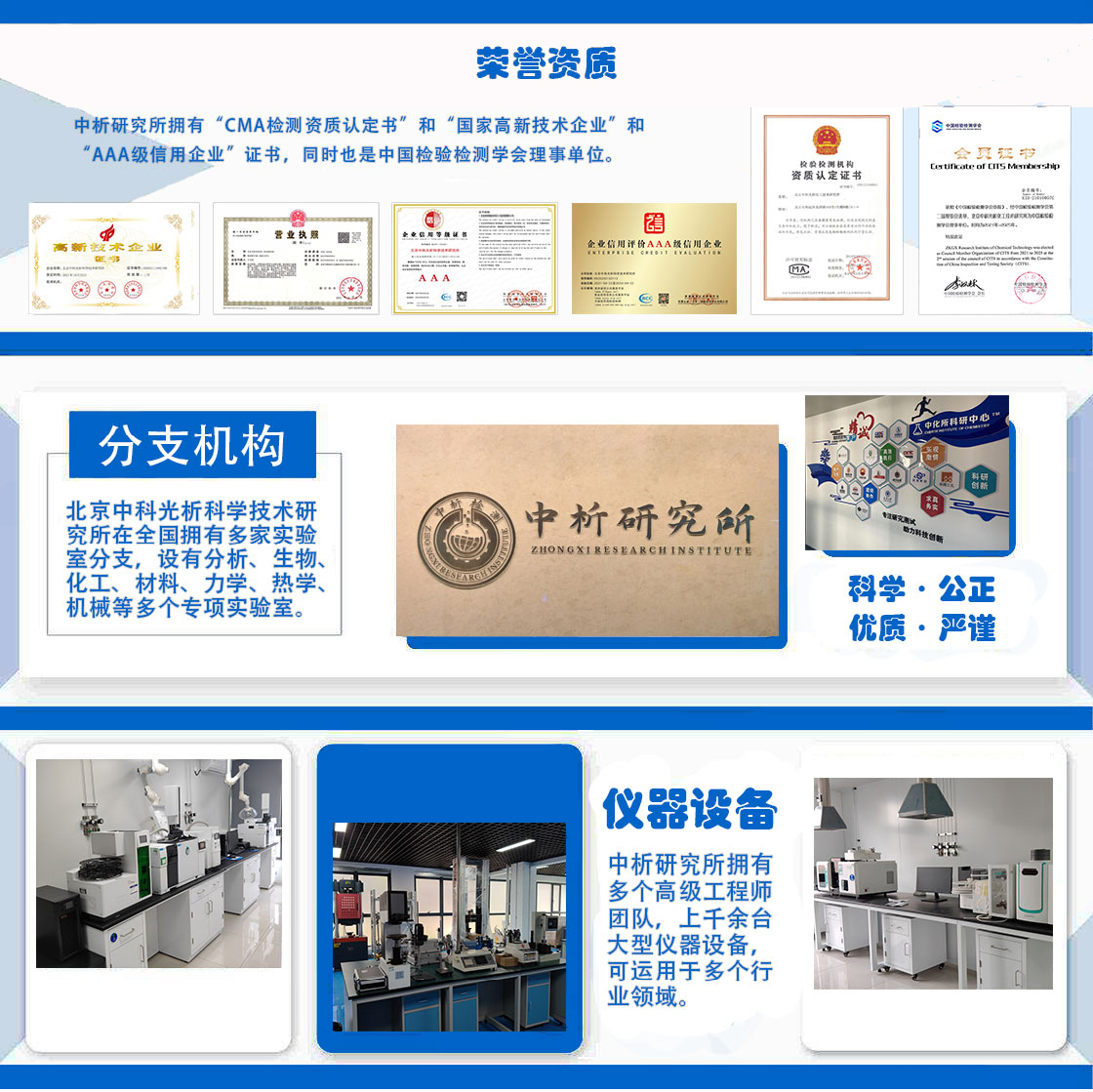
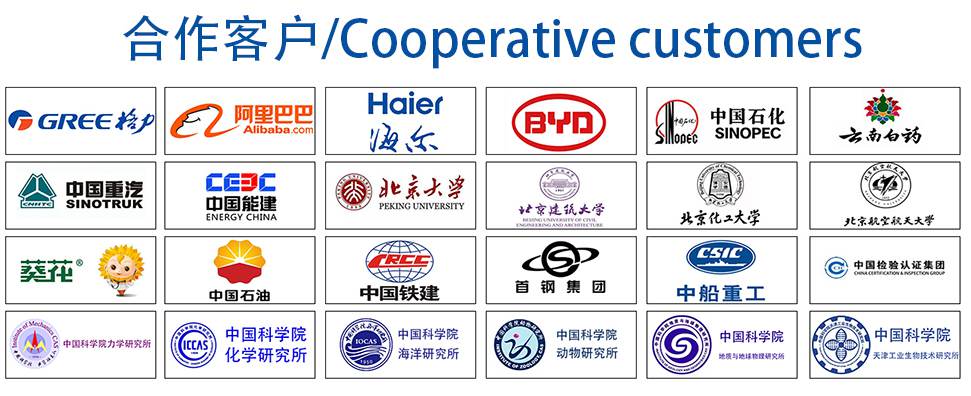