变流器供电的电动机及其控制系统检测概述
随着电力电子技术的快速发展,变流器供电的电动机系统已成为工业自动化、新能源发电和轨道交通等领域的核心动力装置。该系统通过变流器实现电能形式的高效转换,配合齐全控制算法可精准调节电动机的转速、转矩及动态响应特性。然而,由于电力电子器件的高频开关特性、谐波干扰以及复杂控制逻辑的影响,系统运行中可能面临电磁兼容性、绝缘性能劣化、热稳定性不足等问题。因此,针对变流器供电的电动机及其控制系统的全面检测,是保障设备安全运行、延长使用寿命和优化能效的关键环节。检测过程需覆盖硬件性能验证、控制策略匹配性分析以及系统级动态特性评估等维度。
核心检测项目与技术要点
1. 电气参数与绝缘性能检测
通过功率分析仪测量输入/输出电压、电流波形,验证变流器输出频率精度(误差≤0.5%)及电压谐波畸变率(THD<5%)。使用2500V兆欧表测试电动机绕组对地绝缘电阻(≥100MΩ),配合局部放电检测仪定位绝缘薄弱点。需特别关注IGBT模块的结温特性(红外热成像仪监控温升≤85℃)和电容器的等效串联电阻(ESR)变化。
2. 谐波与电磁兼容性(EMC)测试
采用符合IEC 61000-4-7标准的谐波分析仪,检测变流器在满载/轻载工况下的特征谐波(5/7/11次为主)。通过传导发射测试(频率范围150kHz-30MHz)和辐射发射测试(30MHz-1GHz),验证系统是否符合EN 55011 Class A限值要求。同时需进行静电放电(8kV接触放电)、电快速瞬变(4kV电源端口)等抗扰度试验。
3. 动态响应与控制性能验证
搭建半实物仿真平台(HIL),注入阶跃转矩指令(上升时间<5ms),记录转速超调量(≤10%)和调节时间(<100ms)。采用频谱分析仪检测电流环带宽(≥500Hz),验证磁场定向控制(FOC)的矢量解耦精度。通过突加负载测试(0-100%突变)评估系统抗扰动能力,要求转速波动恢复时间不超过200ms。
4. 保护功能与故障诊断测试
模拟过电压(120%Un)、欠电压(80%Un)、过电流(150%In)等异常工况,验证保护电路动作时间(<10μs)。通过注入定子绕组匝间短路故障信号(5%匝间短路率),测试故障特征提取算法的准确率(≥95%)。使用深度学习方法构建故障预测模型,要求剩余寿命预测误差≤8%。
5. 系统能效与热平衡分析
依据GB 30254能效标准,在25%-100%负载区间选取6个工况点,测试系统整体效率(要求≥94%)。采用热流密度传感器监测散热器温差(ΔT<15℃),结合计算流体力学(CFD)仿真优化风道设计。对于大功率系统(>500kW),需进行24小时连续温升试验,关键器件温度不超过绝缘等级限值。
检测技术发展趋势
随着数字孪生技术的应用,基于实时数据驱动的虚拟检测系统可实现故障预判准确率提升40%。新型宽禁带半导体器件(SiC/GaN)的普及,要求检测设备具备ns级时间分辨率和10MHz以上采样率。人工智能算法的引入使多参数关联分析效率提高5-8倍,推动检测模式向智能化、自适应方向发展。
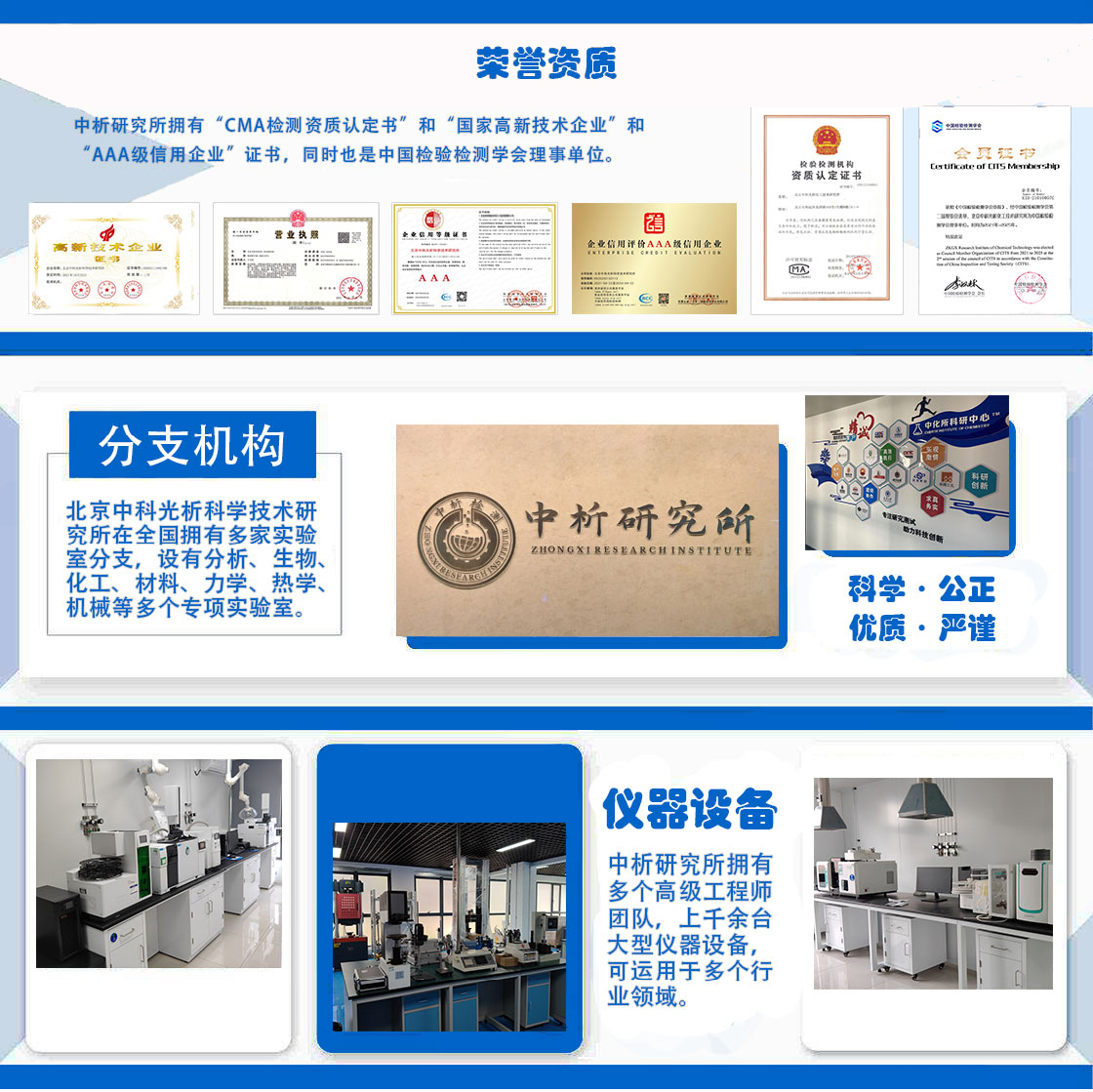
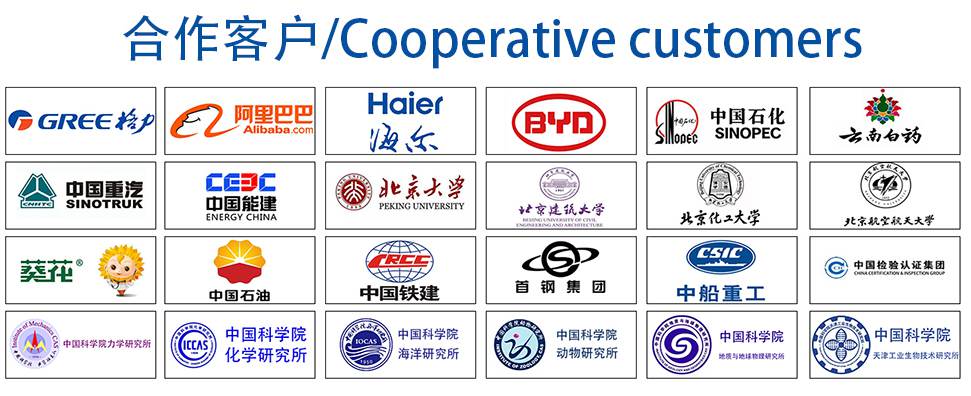