铁路蒸汽机车用给水胶管检测的重要性
铁路蒸汽机车作为历史悠久的动力设备,其给水系统是保障锅炉正常运行的核心部件。给水胶管作为连接水泵与锅炉的关键传输介质,承担着高压、高温水流的输送任务。由于长期暴露在振动、高温、水压波动等复杂工况下,胶管易出现老化、裂纹、变形等问题,可能导致漏水甚至爆管事故。因此,定期对给水胶管进行全面检测是确保蒸汽机车安全运行、延长部件寿命的重要措施。目前,检测工作需依据TB/T 3135-2006《机车车辆橡胶软管》及GB/T 5563-2013《橡胶和塑料软管及软管组合件静液压试验方法》等行业标准执行。
主要检测项目及方法
1. 外观与尺寸检测
通过目视检查和量具测量,评估胶管表面是否存在划痕、鼓包、龟裂等缺陷,同时检查内径、外径、长度是否符合设计要求。重点观察接头部位加固层是否完整,金属接头腐蚀情况。
2. 物理性能测试
采用拉力试验机进行拉伸强度、断裂伸长率测试,验证胶管材料韧性;利用硬度计测量邵氏硬度值,确保胶管在高压环境下的抗变形能力;通过低温弯折试验(-25℃环境下保持4小时)判断耐寒性能。
3. 耐压与爆破试验
使用液压试验台按1.5倍工作压力进行静压试验(持续10分钟),观察是否渗漏;逐步加压至3倍工作压力进行爆破试验,记录破坏压力值,评估安全余量。
4. 化学稳定性检测
通过光谱分析检测胶料成分,确认耐高温添加剂含量;模拟锅炉水质环境(pH 8-10,温度90℃)进行168小时浸泡试验,测定体积膨胀率及力学性能变化。
特殊工况适应性检测
5. 脉冲疲劳试验
模拟实际工作压力波动(0-2.5MPa循环),以1Hz频率进行20万次脉冲试验,检测胶管结构是否出现分层、脱粘等疲劳损伤。
6. 振动老化测试
在振动试验台上模拟机车运行中的多向振动(频率5-50Hz,加速度3g),持续72小时后检查胶管接头密封性及内部增强层状态。
检测周期与结果判定
根据铁道部相关规定,新胶管入库前需完成全项检测,在用胶管每运行5000公里或1年需进行强制性检测。检测数据需对照标准阈值进行分级判定:A级(继续使用)、B级(限时监控)、C级(立即更换)。所有检测过程应留存影像记录,建立数字化档案以实现全生命周期管理。
通过系统化的检测体系,可有效预防因胶管失效导致的锅炉缺水、蒸汽压力异常等安全隐患,为铁路文化遗产的保护和蒸汽机车旅游线路的安全运营提供技术保障。
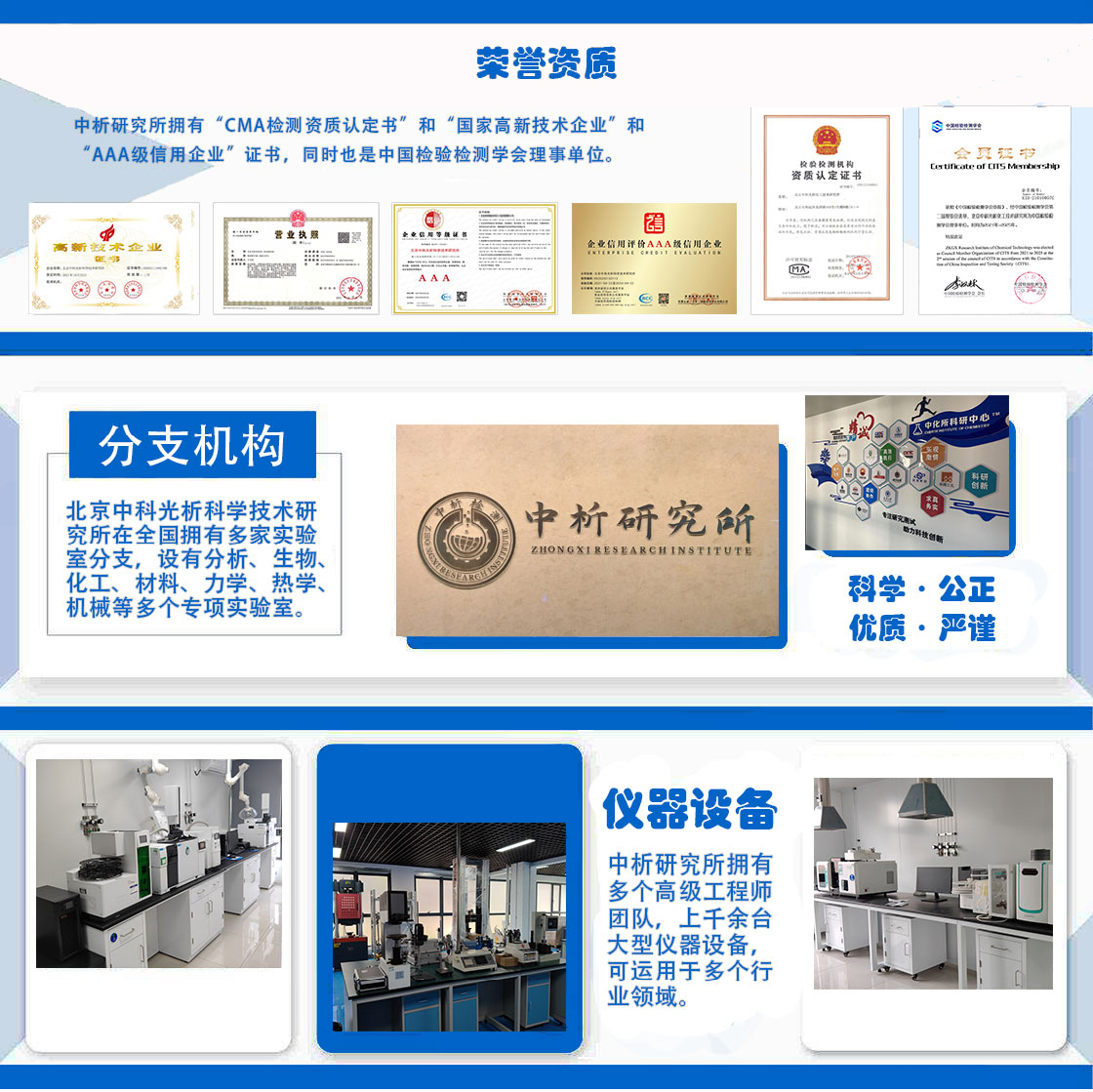
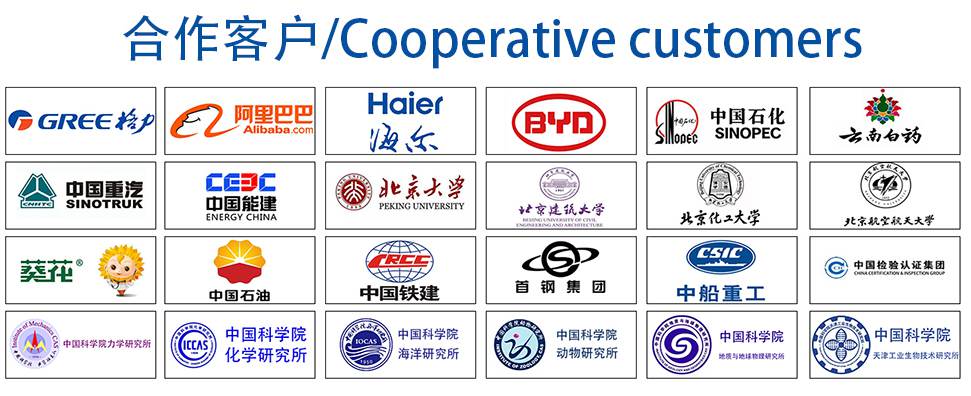