铝用炭素材料检测关键项目解析
铝用炭素材料是电解铝生产的核心原料,主要用于制造电解槽的阳极和阴极部件。随着铝工业对生产效率与环保要求的提升,炭素材料的质量控制已成为保障电解工艺稳定运行的关键环节。通过科学的检测手段对材料性能进行全面评估,可有效预防电解槽早期损坏、电压波动等问题,降低生产成本。本文系统梳理铝用炭素材料的主要检测项目及其技术要点。
一、物理性能检测
1. 机械强度测试:通过三点弯曲法测定抗折强度(标准GB/T 1431),使用万能试验机检测抗压强度(标准GB/T 5072),评估材料在高温环境下的结构稳定性
2. 体积密度与真密度:采用水银置换法(ASTM D2638)测量真密度,结合体积密度计算孔隙率,直接影响材料的抗渗透性和导电效率
3. 电阻率测定:使用四探针法(YS/T 587.5)在特定温度下测试,确保阳极材料导电性能满足电解工艺需求
二、化学组分分析
1. 灰分检测:按照GB/T 1429标准进行高温灼烧,控制灰分含量≤0.5%,避免杂质影响电流效率
2. 微量元素检测:采用ICP-OES分析Fe、Si、V等金属元素含量(ISO 12980),防止有害元素引发阳极过度消耗
3. 硫含量测定:通过库仑滴定法(GB/T 214)精确检测硫化物,硫超标会导致SO₂排放增加
三、结构特性表征
1. X射线衍射分析(XRD):检测石墨化程度(C/H值),晶格参数偏差应小于0.005nm
2. 扫描电镜(SEM)观察:评估骨料与粘结剂相界面结合状态,要求孔隙率≤18%
3. 热膨胀系数测定:使用膨胀仪(ISO 14420)测试20-600℃区间的CTE值,确保与电解槽结构的匹配性
四、使用性能模拟测试
1. 氧化失重试验:在800℃空气氛围中测试12小时,质量损失率需≤20mg/cm²·h
2. CO₂反应性检测:参照YS/T 63.20标准,反应残余率应>85%
3. 钠膨胀试验:模拟电解环境测定体积变化率,合格阈值≤1.2%
现代检测技术已实现从原料煅烧到成品应用的全程监控,结合大数据分析可建立质量预测模型。2019年新修订的ISO 20203标准新增了15项检测指标,推动铝用炭素材料检测向智能化、精准化方向发展。企业建立完善的检测体系,不仅能提升产品合格率,更能为电解槽节能改造提供数据支撑。
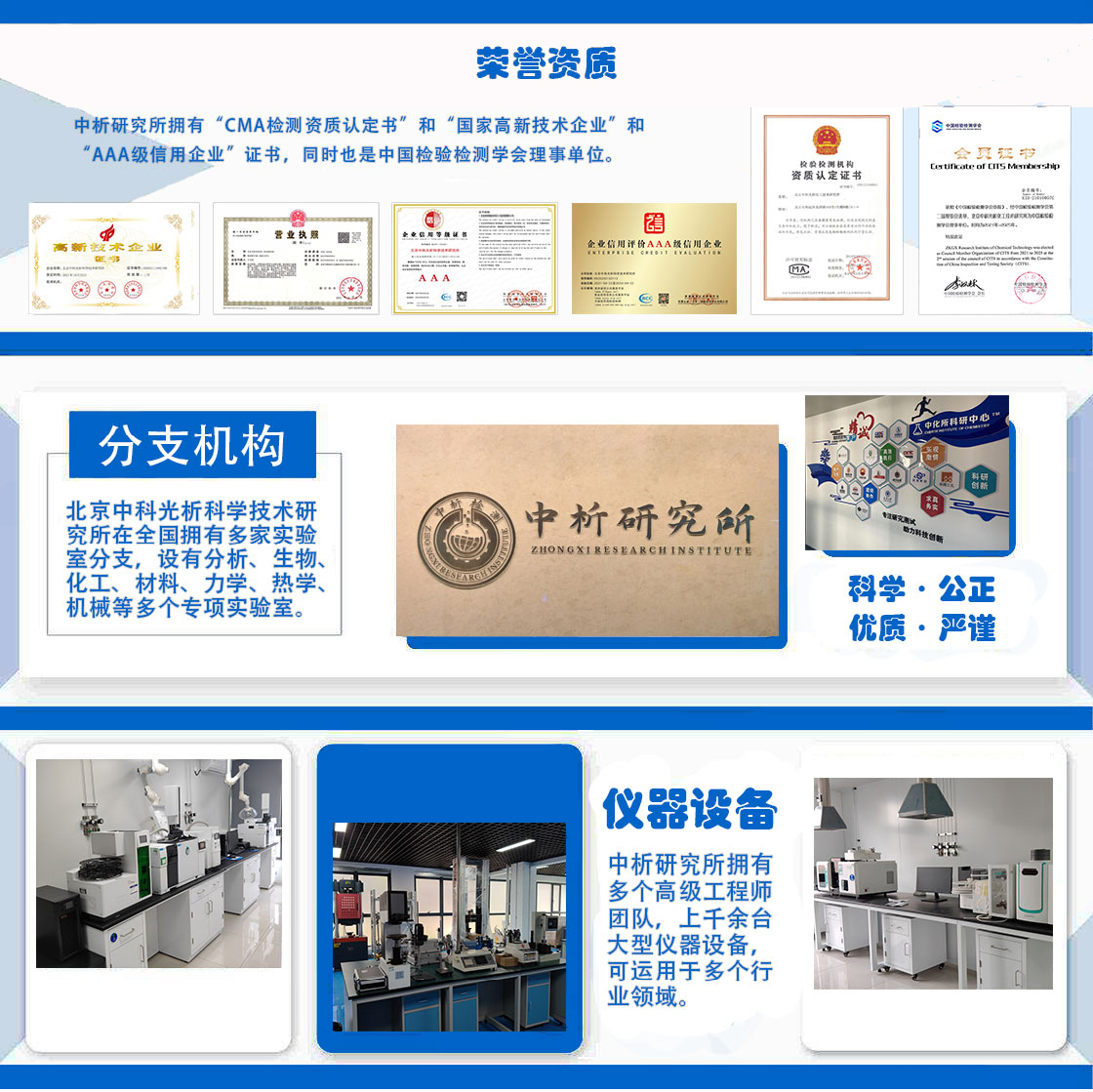
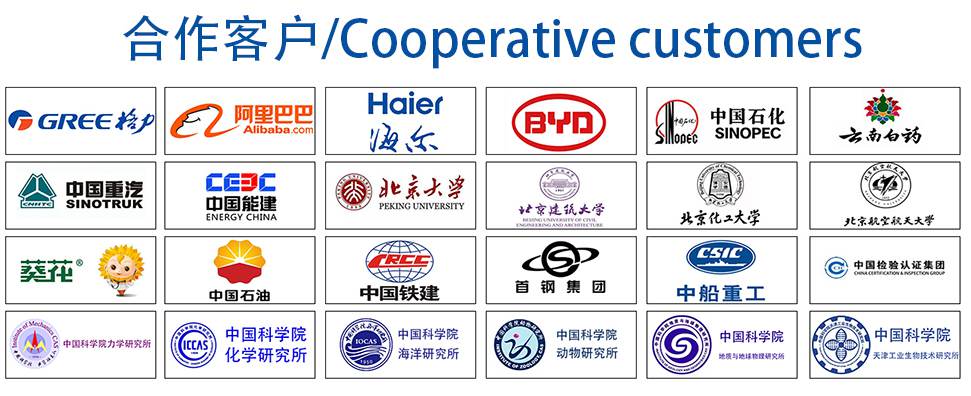