平面度检测技术的核心原理与应用场景
平面度作为几何公差中的关键指标,是衡量机械零件、电子元件和精密设备表面平整程度的重要参数。随着智能制造和精密加工技术的快速发展,平面度检测已从传统的接触式测量发展为融合光学、激光和AI算法的综合技术体系。现代工业对平面度的精度要求可达微米甚至纳米级,尤其在半导体制造、航空航天等高精尖领域,平面度误差可能导致设备性能下降甚至失效。
主流平面度检测技术分类
当前主流的平面度检测技术可分为接触式与非接触式两大类。传统接触式检测采用平台检测法,利用标准平台与工件表面的透光间隙判断平面度,适用于大尺寸工件粗检。精密检测则多使用激光平面干涉仪,通过分析干涉条纹计算表面偏差,精度可达λ/20(约30nm)。新兴的激光三维扫描技术通过点云数据重构表面形态,在汽车覆盖件检测中实现0.05mm级精度。
智能化检测系统的技术突破
基于机器视觉的自动化检测系统正在革新平面度测量领域。采用高分辨率CCD相机配合多轴运动平台,可实现300mm×300mm范围内±1μm的重复测量精度。深度学习算法的引入使系统能自动识别表面缺陷并分类,如华为开发的SmartFlat系统可将检测效率提升400%。工业级在线检测设备集成温度补偿模块,有效消除环境因素对测量结果的影响。
行业应用与标准规范
在半导体行业,晶圆平面度检测要求达到0.1μm/m²,采用白光干涉仪配合真空吸附平台确保测量稳定性。航空航天领域依据ASME B89.3.7标准,使用激光跟踪仪对飞机蒙皮进行全场测量。医疗器械行业遵循ISO 2768标准,通过蓝光三维扫描实现人工关节表面0.01mm级检测。各行业普遍采用基于最小二乘法的平面度评价算法,确保测量结果符合国际规范。
技术挑战与发展趋势
面对异形曲面和复合材料的检测需求,多传感器融合技术成为研发重点。德国蔡司最新推出的COMET系统整合结构光与热成像技术,可同时获取几何形貌与应力分布数据。量子测量技术的突破使原子力显微镜实现原子级平面度分析,为芯片光刻机台研发提供支持。未来5年,基于5G的远程校准系统和数字孪生检测平台将重构平面度质量控制体系。
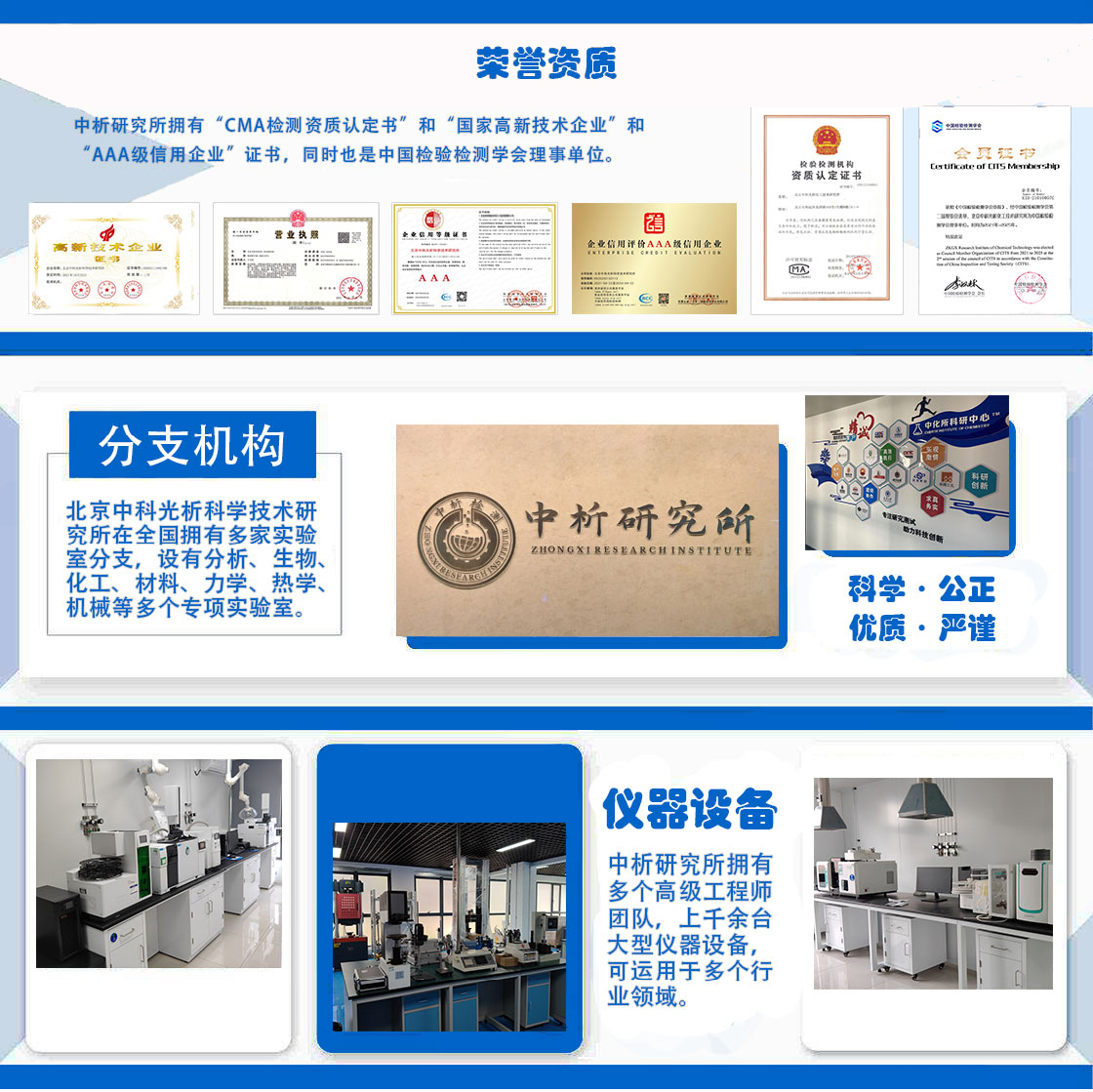
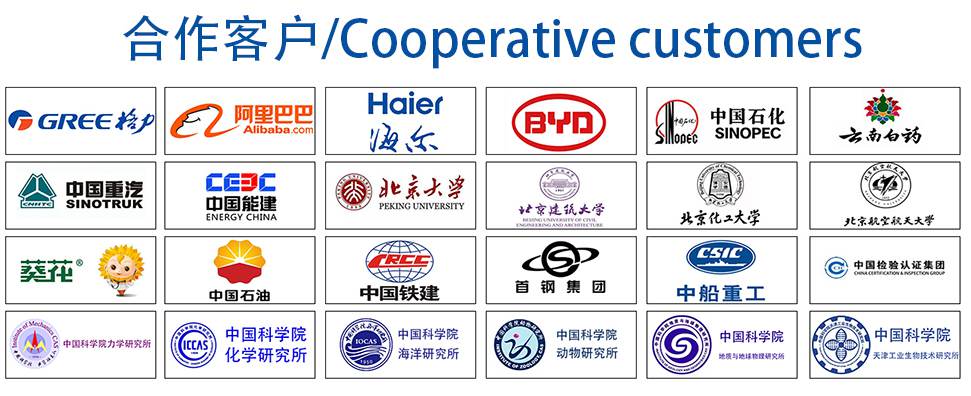