容量分析检测:关键技术与应用场景解读
容量分析检测作为现代工业生产和科研实验中的核心质量控制环节,主要通过定量测量物质体积、空间占比或能量存储能力,为产品性能评估提供关键数据支撑。该技术广泛应用于锂电池制造、化工容器设计、医疗设备校准、食品包装优化等二十余个领域,采用高精度传感器、流体动力学模型与自动化检测设备相结合的复合型技术路线,在保障产品安全性和合规性方面发挥着不可替代的作用。
核心检测项目体系
完整的容量分析检测体系包含六大关键指标验证模块,构成从基础参数到复杂场景的全维度检测网络:
1. 绝对容量精度测试
采用国家计量认证的标准容器进行对比测量,运用激光扫描和重力补偿技术,将检测误差控制在±0.05%以内。重点验证检测设备在满量程、半量程及临界值等关键点的线性响应特性,确保量值传递的可追溯性。
2. 重复性稳定性验证
通过连续200次循环测试获取容量离散系数,使用过程能力指数(CPK)评估设备长期稳定性。典型应用场景包括注射器容积检测(要求CPK≥1.67)和储氢罐体疲劳测试,可有效预测设备使用寿命。
3. 环境适应性检测
搭建温控精度达±0.1℃的模拟实验舱,在-40℃至85℃温度梯度下测试材料热膨胀系数对容量精度的影响。针对新能源电池组等特殊应用场景,需同步进行湿度(5%-95%RH)和压力(0.1-10MPa)多变量耦合测试。
4. 动态响应特性分析
采用高速摄像(1000fps)与粒子图像测速(PIV)技术,捕捉液体灌注过程中气液界面的动态变化。建立三维流场仿真模型,优化检测系统对非牛顿流体、多相混合介质等复杂物料的测量适应性。
5. 兼容性验证矩阵
构建包含酸/碱溶液、有机溶剂、纳米流体等12类介质的测试样本库,评估检测设备材质耐腐蚀性。同步测试RS485、Profinet等工业通讯协议的响应延迟,确保与自动化产线的无缝对接。
6. 数据算法验证系统
开发基于机器学习的异常值识别算法,通过注入式测试验证数据处理模型的可靠性。使用蒙特卡洛法进行3000次仿真实验,确保容量计算模型在95%置信区间内的结果有效性。
当前行业前沿的智能化检测系统已实现0.01μL级分辨率,配合数字孪生技术可构建虚拟检测环境。随着ASTM E542和ISO 8655等国际标准的更新迭代,容量分析检测正朝着多模态感知、自主决策的第三代检测系统演进,为智能制造提供更精准的质量控制方案。
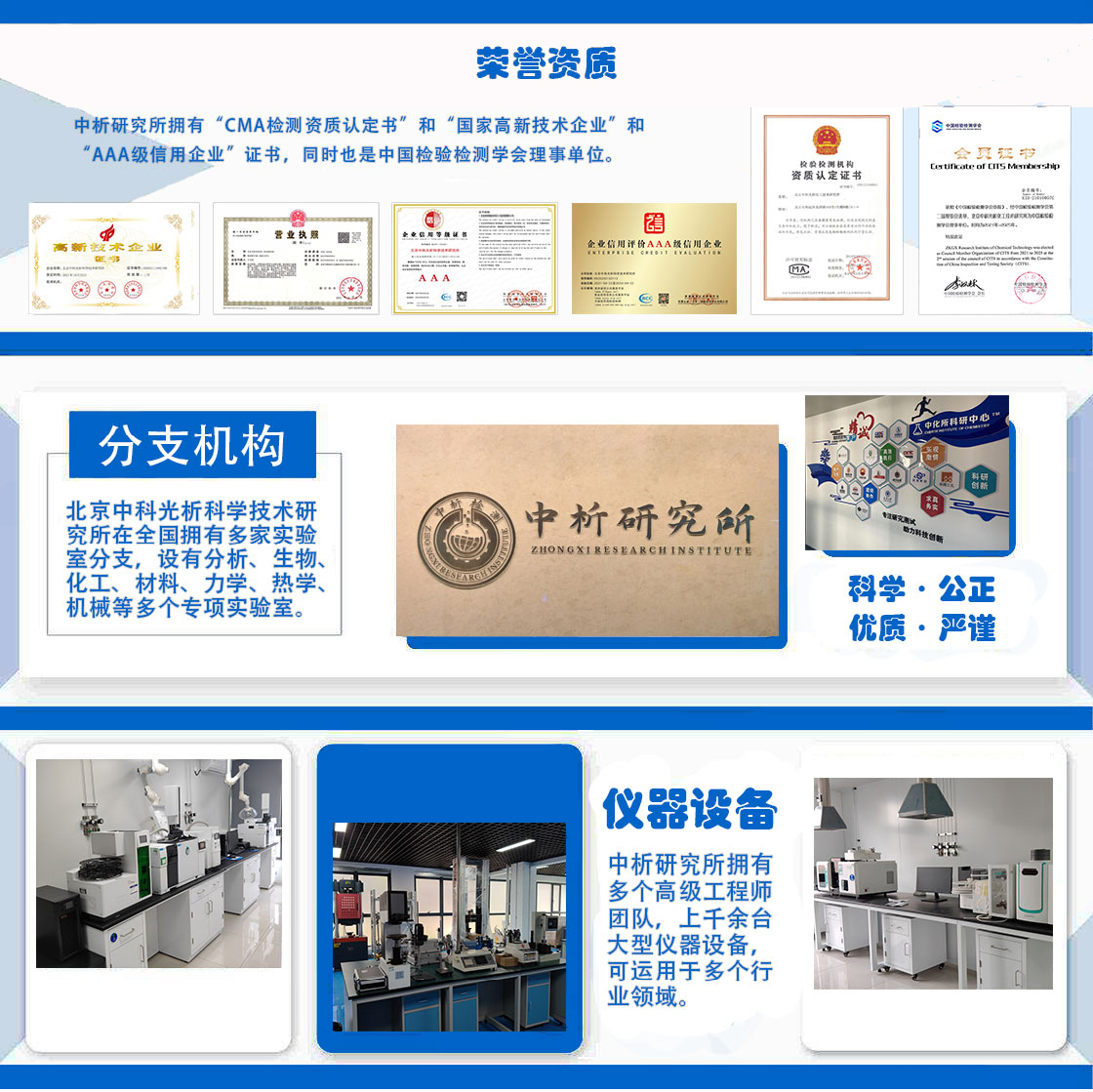
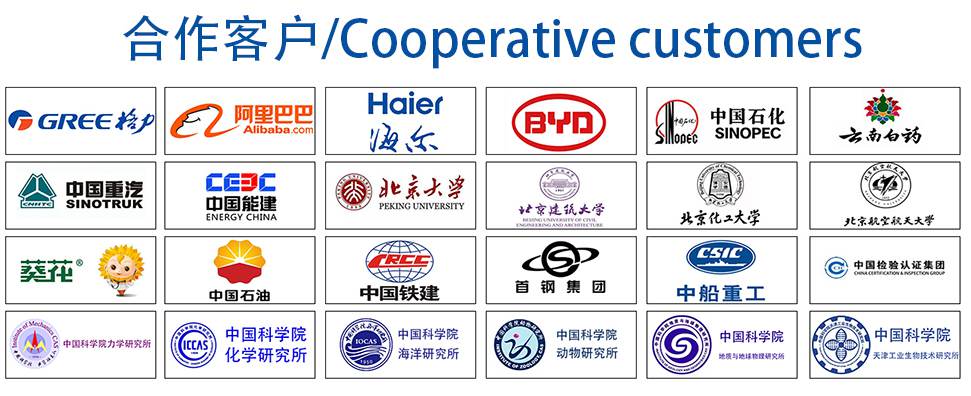