水分离性检测概述
水分离性是评价油品、乳化液及其他工业流体在特定条件下与水分离能力的重要指标,广泛应用于石油化工、润滑油生产、金属加工液及环保监测等领域。该检测通过模拟实际工况条件,分析材料中水分的析出速度、分离效率及稳定性,对产品质量控制、设备防腐和使用寿命预测具有关键意义。例如,润滑油中水分残留会导致氧化变质,燃油含水可能引发燃烧不充分或腐蚀发动机部件,因此水分离性检测成为工业流程中不可或缺的质量控制环节。
核心检测项目与方法
1. 水分含量测定(静态分离法)
采用卡尔费休滴定法(Karl Fischer Titration)或蒸馏法,定量分析样品中游离水、乳化水及溶解水的总含量。ASTM D6304标准规定了精确测定石油产品水含量的操作流程,需配合专用仪器确保误差小于0.03%。
2. 破乳化性测试
通过离心分离法(ASTM D1401)或搅拌静置法模拟油水混合物的分离过程。检测时将试样与去离子水按比例混合,在标准温控下观察油层、水层及乳化层的形成时间与体积比,计算破乳效率(通常要求>90%)。
3. 界面张力测试
使用悬滴法或旋转滴张力仪测量油水界面张力值,ASTM D971标准规定在25℃下检测。低界面张力(如<15 mN/m)表明油水易乳化,需结合抗乳化剂性能分析。
4. 动态分离模拟实验
利用高压釜或循环流动装置模拟管道输送、机械剪切等实际工况,连续监测油水分离效率。例如,参照ISO 6614标准进行循环热冲击测试,评估润滑脂在高温高压下的水分释放特性。
5. 长期稳定性监测
通过加速老化试验(如85℃/85%RH恒温恒湿箱存储)观察样品随时间的水分吸附与分离趋势,结合显微镜观测乳化液滴粒径分布变化,预测产品储存寿命。
检测结果的应用与标准
水分离性检测数据需对照行业标准(如GB/T 260、ISO 9029)进行分级判定。航空液压油要求40℃下30分钟内完成99%水分离,车用柴油需通过2000转离心5分钟的破乳测试。检测报告需涵盖分离时间、分层体积、浊度变化等关键参数,为工艺改进和配方优化提供量化依据。
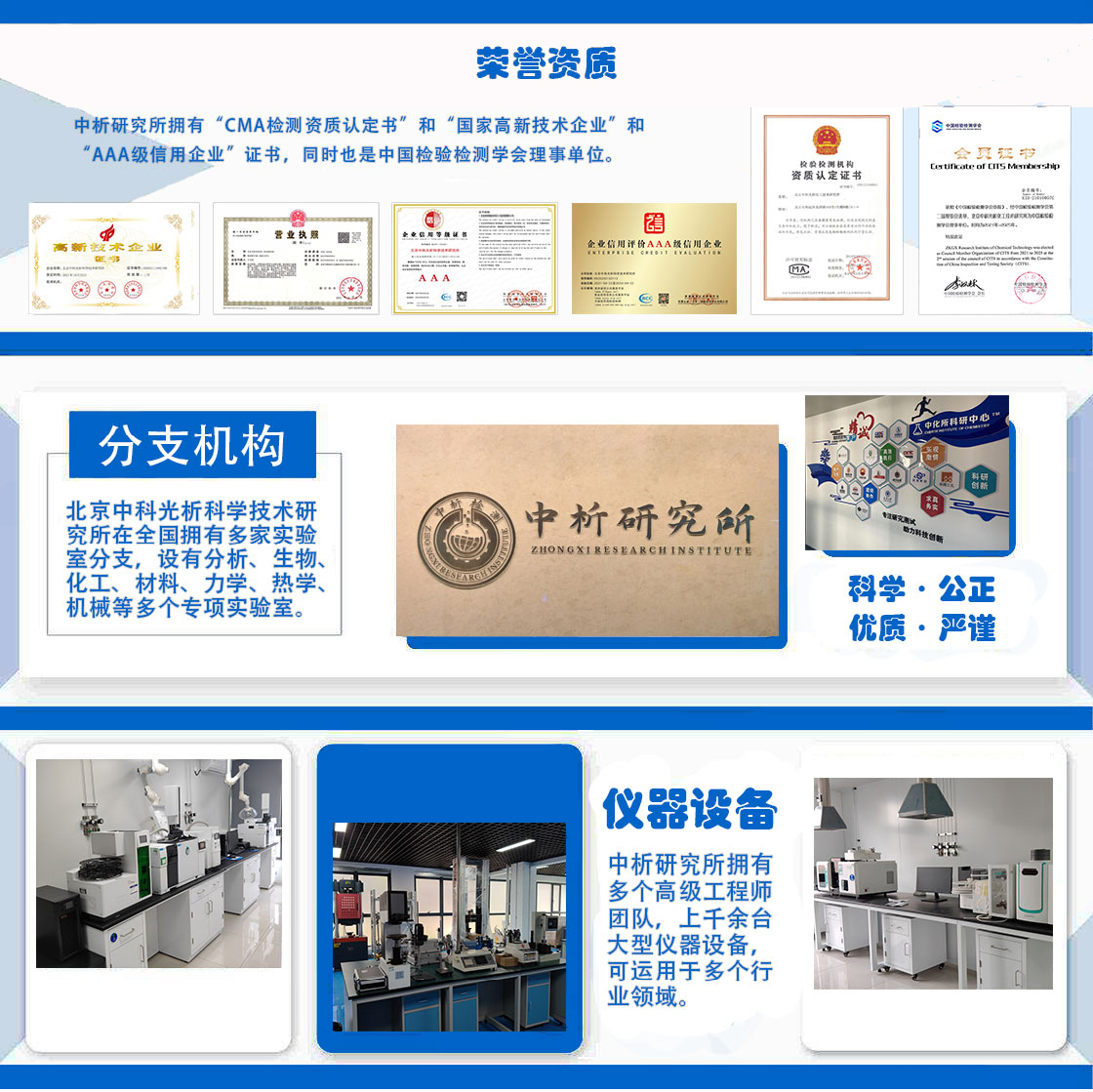
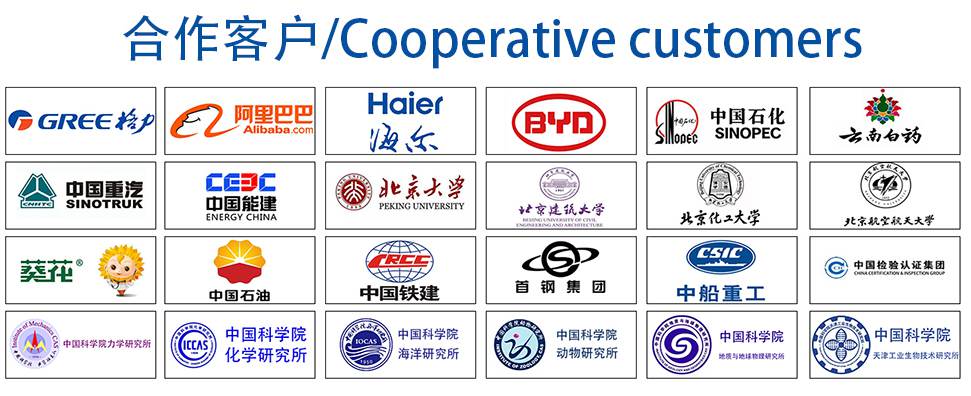