钢、镍、铜、铝、钛及钛合金设备及管道熔化焊对接接头检测技术规范
在石油化工、电力、航空航天等领域,钢、镍、铜、铝、钛及钛合金设备及管道的熔化焊对接焊接接头质量直接关系到设备的安全性和使用寿命。由于不同金属材料在焊接过程中易产生气孔、裂纹、未熔合等缺陷,需依据材料特性、服役环境及行业标准制定针对性的检测方案。本文系统阐述各类材质的焊接接头检测项目、方法及标准规范,为工程实践提供技术参考。
一、钢制设备及管道焊接接头检测
1. 无损检测项目:采用射线检测(RT)、超声波检测(UT)进行内部缺陷筛查,磁粉检测(MT)用于表面及近表面裂纹检测。
2. 理化性能测试:包括焊缝拉伸试验、弯曲试验、冲击韧性试验(-20℃低温冲击),硬度检测需满足HB≤350的限值要求。
3. 验收标准:执行NB/T 47013-2015《承压设备无损检测》及GB 50236《现场设备、工业管道焊接工程施工规范》,Ⅱ级焊缝合格率需达100%。
二、镍及镍合金焊接接头专项检测
1. 微观组织分析:采用金相显微镜观察焊缝晶间腐蚀倾向,检测碳化物析出情况。
2. 渗透检测(PT):对高温镍基合金焊缝表面开口缺陷进行高灵敏度检测,显示剂停留时间≥10分钟。
3. 腐蚀试验:按ASTM G28进行晶间腐蚀试验,要求腐蚀速率≤0.5mm/a。
三、铜及铜合金焊接质量管控
1. 超声波相控阵检测:针对铜材高声衰减特性,采用聚焦探头提高缺陷检出率。
2. 气密性试验:对制冷用铜管实施0.6MPa氮气保压试验,压降率≤1%/h。
3. 电导率测试:使用涡流导电仪检测焊缝区电导率,偏差值应控制在母材的±5%以内。
四、铝及铝合金焊接缺陷防控
1. X射线数字成像(DR):识别气孔、夹渣等典型缺陷,单个气孔直径≤1.5mm且不超过壁厚的10%。
2. 泄漏检测:对压力容器实施氦质谱检漏,允许泄漏率≤1×10^-6 Pa·m³/s。
3. 阳极氧化检测:通过氧化膜厚度测量(≥10μm)评估焊缝耐蚀性能。
五、钛及钛合金焊接特殊要求
1. α相含量检测:采用金相法测定焊缝α相比例,要求≤30%以防止脆化。
2. 真空氦检漏:对核级钛管实施1×10^-9 Pa·m³/s级超高灵敏度检测。
3. 高温持久试验:按AMS 4911标准进行500℃/100h持久强度测试,断裂时间≥48h。
在具体工程应用中,应根据材料牌号(如TA2钛材、316L不锈钢)、壁厚范围(2-50mm)、服役介质(酸性/高温环境)等参数优化检测工艺。通过建立多手段联检体系(如RT+UT+PT组合检测),可实现对焊接缺陷的三维定位和定量评价,确保设备全生命周期安全运行。
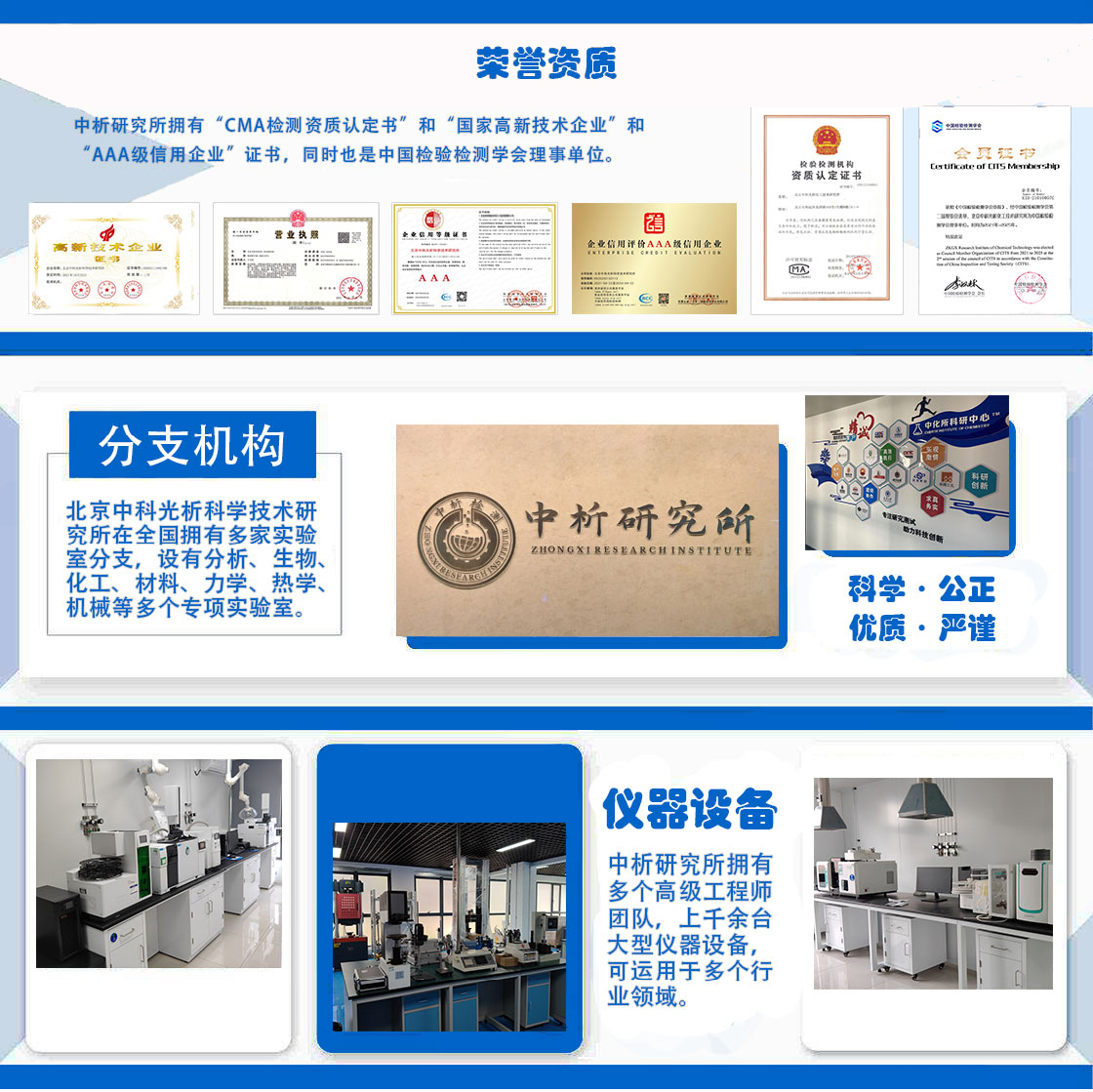
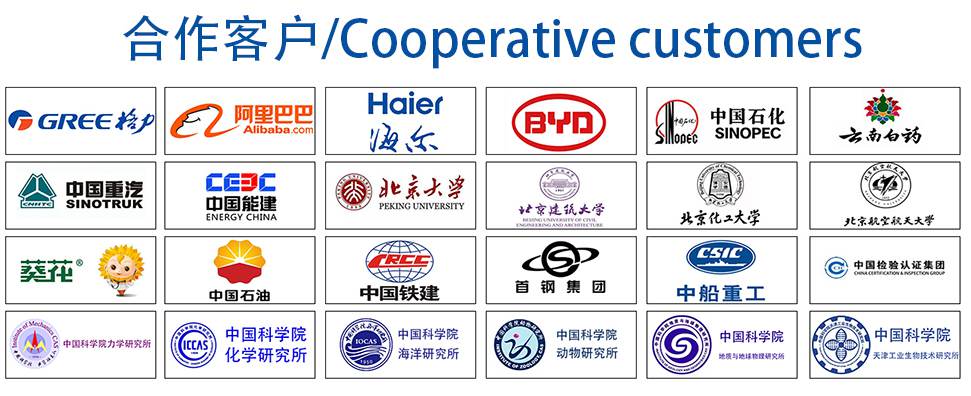