电动汽车用动力蓄电池安全检测的重要性与核心项目解析
随着新能源汽车产业的快速发展,动力蓄电池作为电动汽车的"心脏",其安全性已成为行业关注的核心问题。据中国汽车工业协会统计,2022年我国动力电池装车量达到294.6GWh,同比增长90.7%。在这一背景下,依据国家标准GB 38031-2020《电动汽车用动力蓄电池安全要求》开展的检测工作,成为保障车辆安全、推动产业升级的重要技术支撑。动力蓄电池的检测不仅涉及材料、结构、工艺等基础要素,更需要通过多维度、多场景的测试验证其极端工况下的安全表现。
核心检测项目体系
根据国家标准要求,动力蓄电池安全检测体系主要包含四大类检测项目:
1. 机械安全测试
包含振动测试(模拟车辆行驶工况)、挤压测试(模拟碰撞变形)、针刺测试(内短路防护)等。其中挤压测试要求电池模组在承受100kN压力时不起火、不爆炸,测试后绝缘电阻需保持≥100Ω/V。
2. 环境安全测试
涵盖温度冲击(-40℃~85℃循环)、湿热循环(85%湿度)、海水浸泡(3.5%盐浓度)等恶劣环境模拟。温度冲击试验需进行5次完整循环,每次循环时间不超过6小时,验证电池材料的热稳定性。
3. 电气安全测试
包括过充(1.5倍标称电压)、过放(0V放电)、外部短路(80mΩ阻值短路)等异常工况检测。在过充测试中,要求电池管理系统(BMS)能在120%SOC时触发保护机制,有效切断充电回路。
4. 热安全测试
重点开展热扩散试验,通过局部加热触发单体热失控,要求电池系统在5分钟内不起火。最新标准新增了多层级热蔓延阻断能力评估,测试点温度需控制在300℃以下。
检测技术创新方向
当前检测技术正向智能化方向发展,包括:基于AI的故障模式预测、多物理场耦合仿真测试、云端实时监控系统等。某头部检测机构研发的"全气候动态测试舱",可模拟-50℃~100℃极端温变环境,测试精度达±0.5℃。这些创新技术显著提升了检测效率与结果可靠性。
通过系统化的安全检测,动力蓄电池的故障率已从2018年的0.12%降至2022年的0.035%。随着固态电池、钠离子电池等新技术路线的产业化推进,检测标准将持续迭代更新,为新能源汽车的安全出行构建坚实的技术防线。
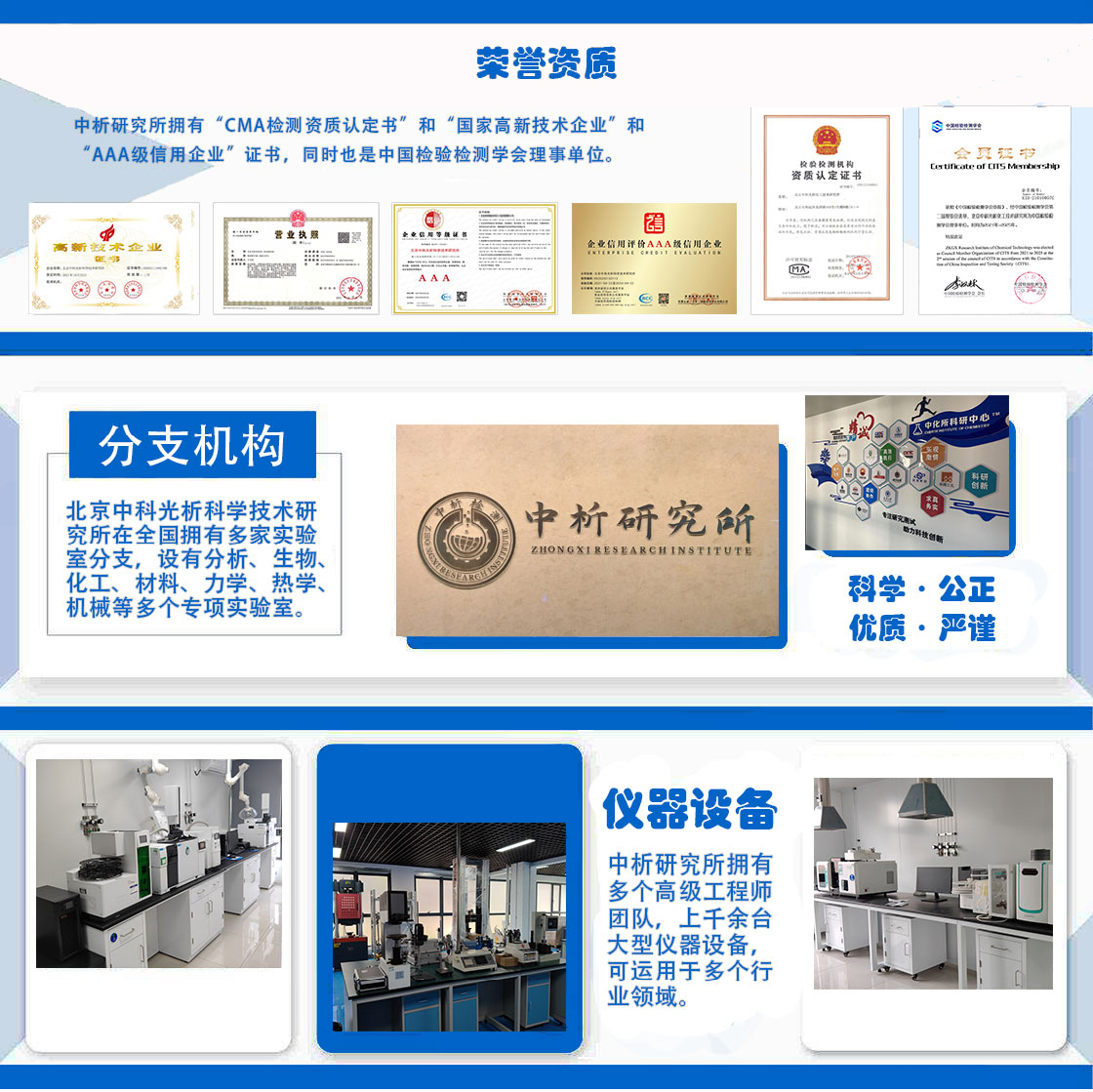
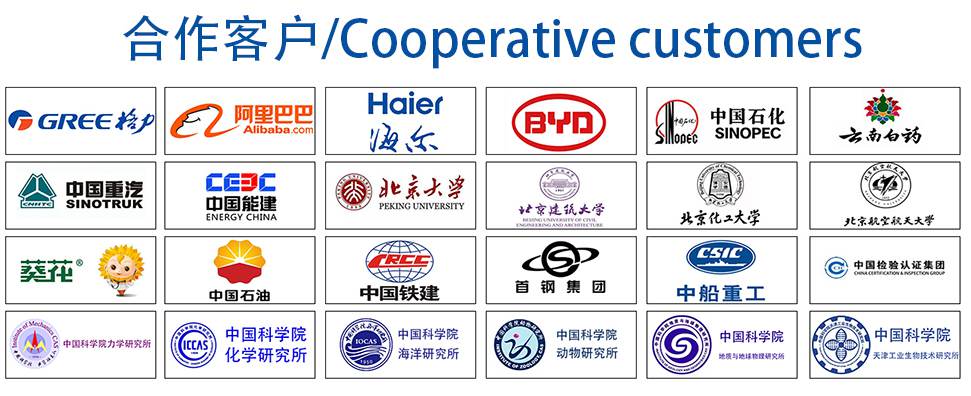