工业锅炉水检测的重要性与必要性
工业锅炉作为热能转换的核心设备,其水质直接影响设备运行效率、能源消耗及使用寿命。未经处理的锅炉水易产生结垢、腐蚀和汽水共腾等问题,导致传热效率下降30%以上,燃料消耗增加5%-15%,严重时可能引发爆管等安全事故。根据《GB/T 1576-2018工业锅炉水质》标准,定期开展锅炉水检测已成为法定要求。通过科学的水质监控,可延长锅炉寿命2-3倍,降低维护成本40%以上,同时确保蒸汽品质符合生产需求。
核心检测项目解析
1. pH值检测
锅炉水的pH值需控制在10-12之间,碱性环境可有效抑制金属腐蚀。检测采用玻璃电极法,当pH<7时会加速Fe³+腐蚀反应,pH>12则可能引发苛性脆化。现场快速检测需配备便携式pH计,实验室分析则应使用经过校准的数字酸度计。
2. 硬度检测(总硬度/钙镁离子)
总硬度检测通过EDTA滴定法实现,要求≤0.03mmol/L。当硬度超标时,钙镁盐类在受热面上形成2-5mm厚度的水垢,导致热效率每下降1%就增加2%燃料消耗。采用原子吸收光谱法可精确测定钙(Ca²+)、镁(Mg²+)离子浓度。
3. 溶解氧含量测定
溶解氧应严格控制在≤0.1mg/L,采用靛蓝二磺酸钠分光光度法或电化学探头法检测。氧腐蚀可造成管壁每年0.5-1mm的损耗,通过联氨处理或真空除氧可将氧含量降至安全范围。
4. 氯离子检测
氯离子浓度需≤400mg/L,硝酸银滴定法是常用检测手段。Cl⁻超过限值会引发点蚀和应力腐蚀,特别在高温高压条件下,氯离子浓缩可导致奥氏体钢发生晶间腐蚀。
5. 磷酸盐与碱度检测
总碱度应维持2-8mmol/L,磷酸根浓度控制在5-20mg/L。采用酸碱滴定法测定甲基橙碱度,钼酸铵分光光度法检测PO₄³⁻。合理的磷酸盐处理可形成保护性磷化膜,预防钙垢生成。
配套检测项目体系
完整的检测体系还应包括:电导率(反映总溶解固体)、悬浮物(重量法测定)、含油量(红外分光法)、二氧化硅(硅钼蓝法)等指标。对于高压锅炉需增加联氨残余量检测,采用对二甲氨基苯甲醛比色法确保含量在0.01-0.05mg/L之间。
智能检测与数据分析
现代检测技术已实现在线监测系统应用,通过离子选择电极、光谱探头等传感器实时传输数据。结合LIMS实验室管理系统,可建立水质变化趋势模型,当TDS(总溶解固体)达到临界值时自动触发排污程序,实现预测性维护。
检测周期与实施规范
根据TSG G5001-2010锅炉水(介)质处理规则,运行中锅炉应每4小时进行1次现场检测,每周完成全套实验室分析。新安装或大修后的锅炉需进行72小时连续监测,确保给水、炉水、蒸汽三项指标完全达标。
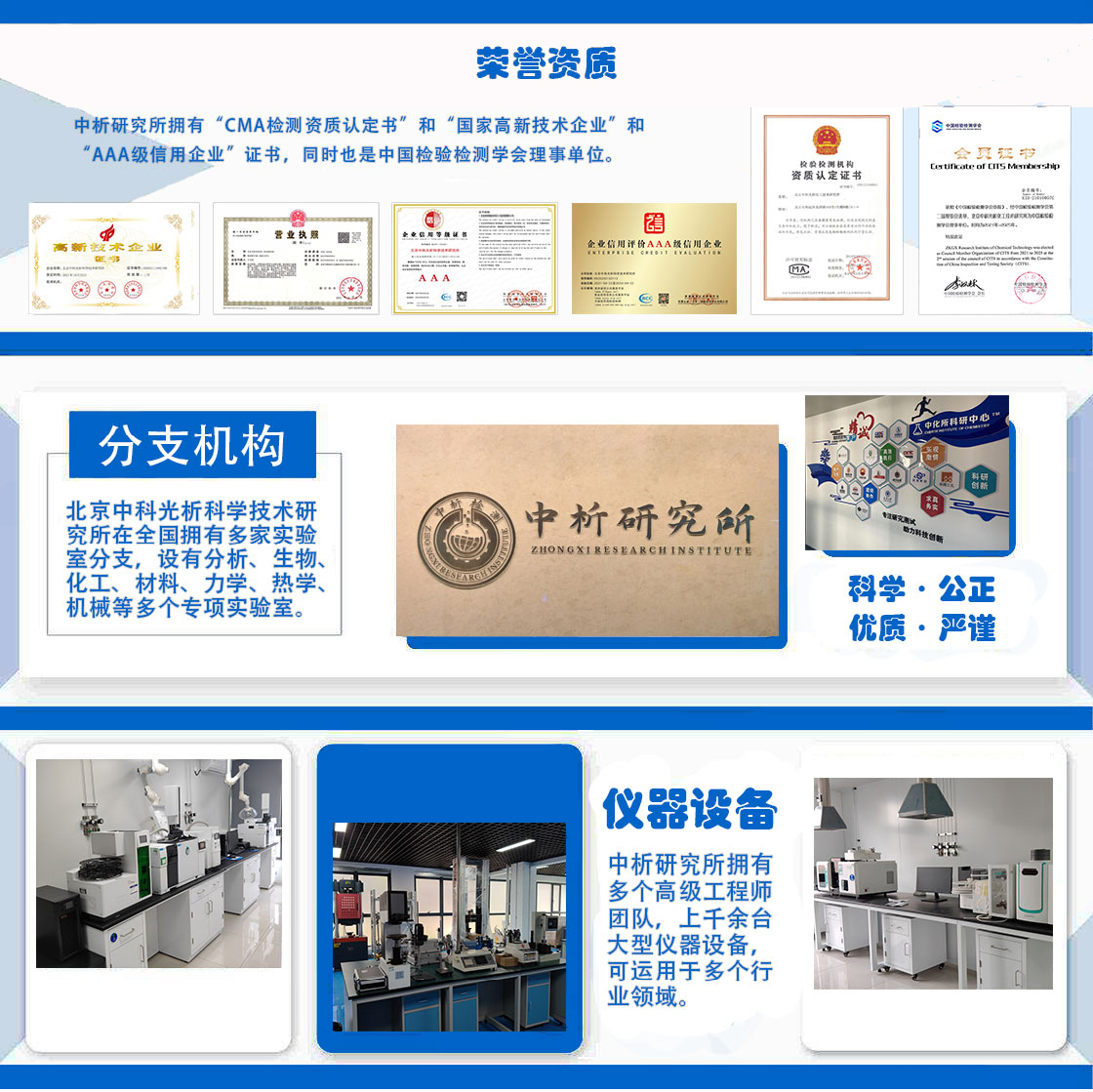
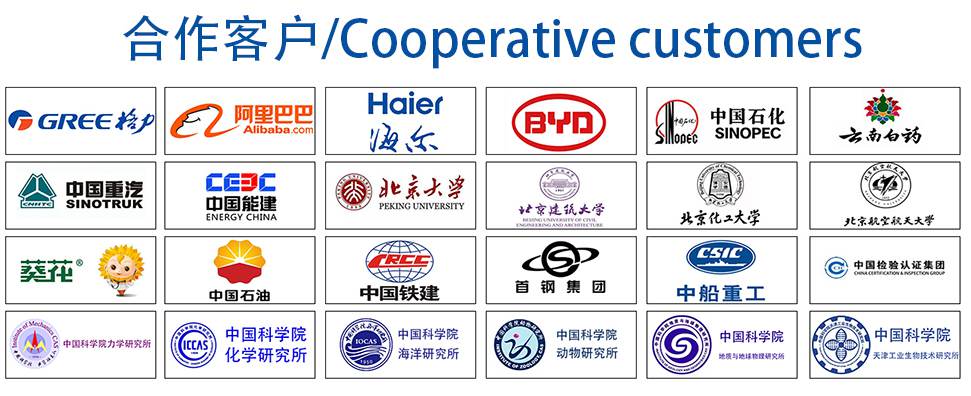