涡轮机油检测的重要性与核心项目解析
涡轮机油作为汽轮机、燃气轮机等大型旋转设备的核心润滑介质,承担着减少摩擦、冷却部件、密封防锈及传递能量的多重作用。其性能的优劣直接影响机组运行效率、设备寿命和安全性。据统计,约60%的涡轮系统故障与油品劣化直接相关,因此定期开展专业涡轮机油检测已成为工业设备预防性维护的重要环节。通过系统化的检测分析,可精准掌握油液状态,预测潜在风险,为设备健康管理提供科学依据。
涡轮机油关键检测项目分类
基础理化指标检测
1. 运动黏度检测(ASTM D445):通过测量40℃和100℃下的黏度值,判断油品是否出现氧化聚合或稀释现象。黏度变化超过±15%即需关注
2. 酸值检测(ASTM D664/D974):检测总酸值(TAN)和强酸值(SAN),酸值突增表明油品发生氧化变质,可能引发金属腐蚀
3. 水分含量检测(ASTM D6304):采用卡尔费休法精准测定游离水和溶解水,当含水率超过500ppm可能引发油膜破裂和锈蚀
污染物分析
1. 颗粒污染度检测(ISO 4406):采用自动颗粒计数器评估油液清洁度等级,NAS 1638标准规定涡轮系统应保持≤7级
2. 闪点测试(ASTM D92):检测油品可燃特性,闪点下降10%以上提示可能存在燃油污染
3. 傅里叶红外光谱分析(FTIR):识别氧化产物(1720cm⁻¹)、硝化产物(1630cm⁻¹)等特征峰,量化抗氧化剂消耗程度
性能衰减评估
1. 抗氧化性测试(RBOT,ASTM D2272):通过旋转氧弹试验测定氧化安定性,剩余寿命低于初始值50%需换油
2. 抗乳化性检测(ASTM D1401):测量油水分离时间,超过30分钟表明抗乳化性能劣化
3. 泡沫特性测试(ASTM D892):评估油品消泡能力,泡沫倾向性超过500ml/0ml需重点关注
检测周期与结果应用
推荐每6个月或累计运行4000小时进行系统检测,对于关键机组应缩短至3个月。检测数据应建立趋势分析档案,当出现以下预警时需立即采取应对措施:酸值上升0.3mgKOH/g以上、黏度变化超±10%、颗粒污染度升高2级、水分含量突破警戒值。通过科学的检测维护,可使涡轮系统维护成本降低35%,设备寿命延长20%以上。
涡轮机油的综合检测不仅是简单的指标比对,更是设备健康状态的深度体检。采用光谱分析、铁谱分析等齐全技术,配合工业大数据的趋势预测,形成从被动维修到主动预防的智能运维体系,为现代工业设备的可靠运行提供坚实保障。
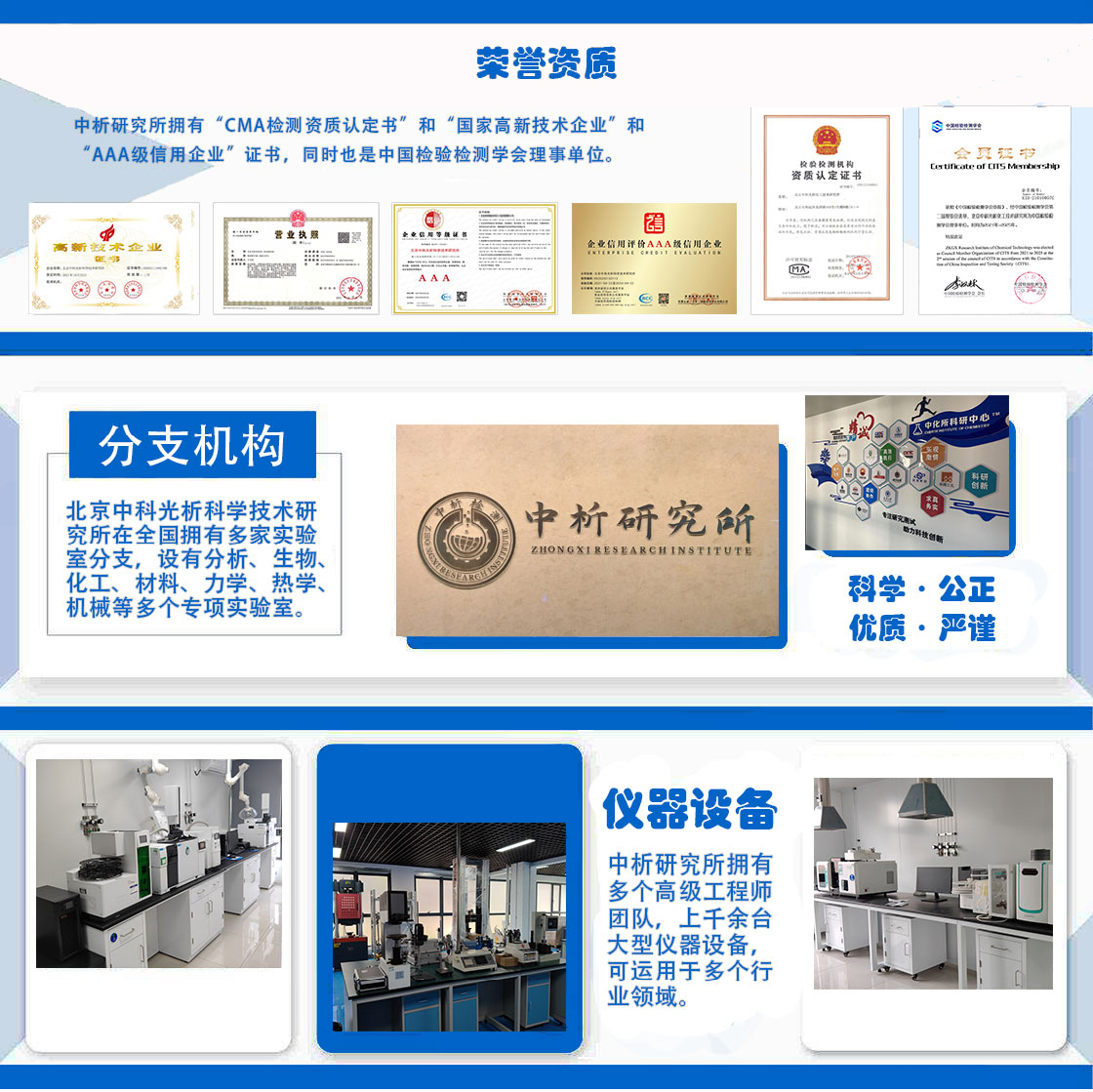
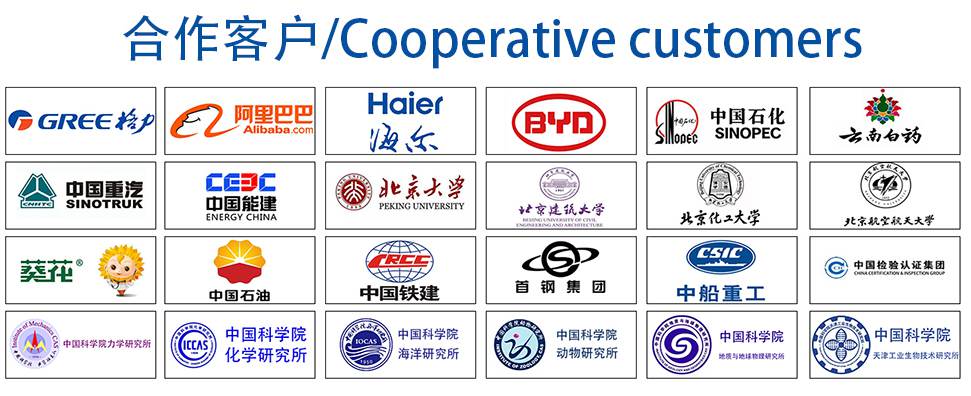