随着能源结构向清洁化、低碳化转型,沿海及海上风电作为可再生能源的重要组成部分,迎来了快速发展期。然而,海洋环境特有的高盐雾、高湿度、强紫外线辐射以及微生物侵蚀等复杂腐蚀因素,对风电机组塔筒、叶片、基础结构等部件的耐久性提出了严峻挑战。防腐涂料作为抵御腐蚀的第一道防线,其性能直接关系到机组20-25年设计寿命的实现以及运维成本的控制。因此,建立科学、系统的防腐涂料检测体系,成为确保风电设备全生命周期安全运行的关键环节。
一、防腐涂料基础性能检测
涂层的基础性能检测包括附着力、硬度、柔韧性等机械性能测试。采用划格法(ASTM D3359)和拉开法(ISO 4624)评估涂层与基材的结合强度,确保在极端风载荷下不发生剥落。铅笔硬度测试(ASTM D3363)与杯突试验(ISO 1520)则分别验证涂层抗划伤能力和形变适应性,满足海上机组动态运行需求。
二、耐候性加速老化测试
通过盐雾试验(ISO 9227)模拟海洋大气环境,连续喷射5% NaCl溶液,评估涂层2400小时后的起泡、锈蚀情况。QUV紫外老化测试(ASTM G154)模拟太阳光谱中UV波段,检测涂层粉化、变色等光老化特征。湿热循环测试(IEC 60068-2-30)则验证涂层在温度40℃、湿度95%条件下的抗水解性能。
三、电化学腐蚀防护性能检测
针对含锌环氧底漆等牺牲阳极型涂料,采用电化学阻抗谱(EIS)测定涂层电阻值(>1×10^9 Ω·cm²为优),结合开路电位监测评估阴极保护效果。对于有机硅改性聚氨酯面漆,通过划痕加速试验(ASTM B117)量化涂层破损处的蔓延腐蚀速率,要求单边扩蚀<2mm/年。
四、特殊环境适应性检测
针对海上风电特有的飞溅区工况,设计动态海水冲击试验(DNVGL-RP-0416),以4m/s流速含砂海水连续冲击涂层表面500小时,检测抗冲蚀磨损性能。低温固化特性测试(NORSOK M-501)验证涂料在-5℃施工环境下的成膜完整性,确保冬季维修作业质量。此外,微生物附着试验(ISO 22196)评估涂层表面抑菌率,要求海洋生物附着量减少≥90%。
五、环保与长效性综合评估
依据IMO《船舶压载水管理系统公约》,检测涂料中生物杀伤剂释放浓度,确保海洋生态安全。采用气相色谱-质谱联用(GC-MS)分析挥发性有机物(VOC)含量,满足GB 30981-2020标准要求。通过5年实海挂片试验获取涂层保光率(>80%)、锈蚀扩展面积(<3%)等数据,建立实验室加速老化与现场服役性能的对应关系模型。
当前,国际认证机构如DNV GL、TÜV等已推出风电专用涂层认证体系,要求检测项目覆盖原材料筛查、施工工艺验证、服役性能预测全链条。随着石墨烯改性涂料、自修复涂层等新材料的应用,检测技术正向智能化、原位化方向发展,如采用电化学噪声监测、无人机光学检测等手段,实现腐蚀防护状态的实时评估与预警,为海上风电大规模开发提供可靠保障。
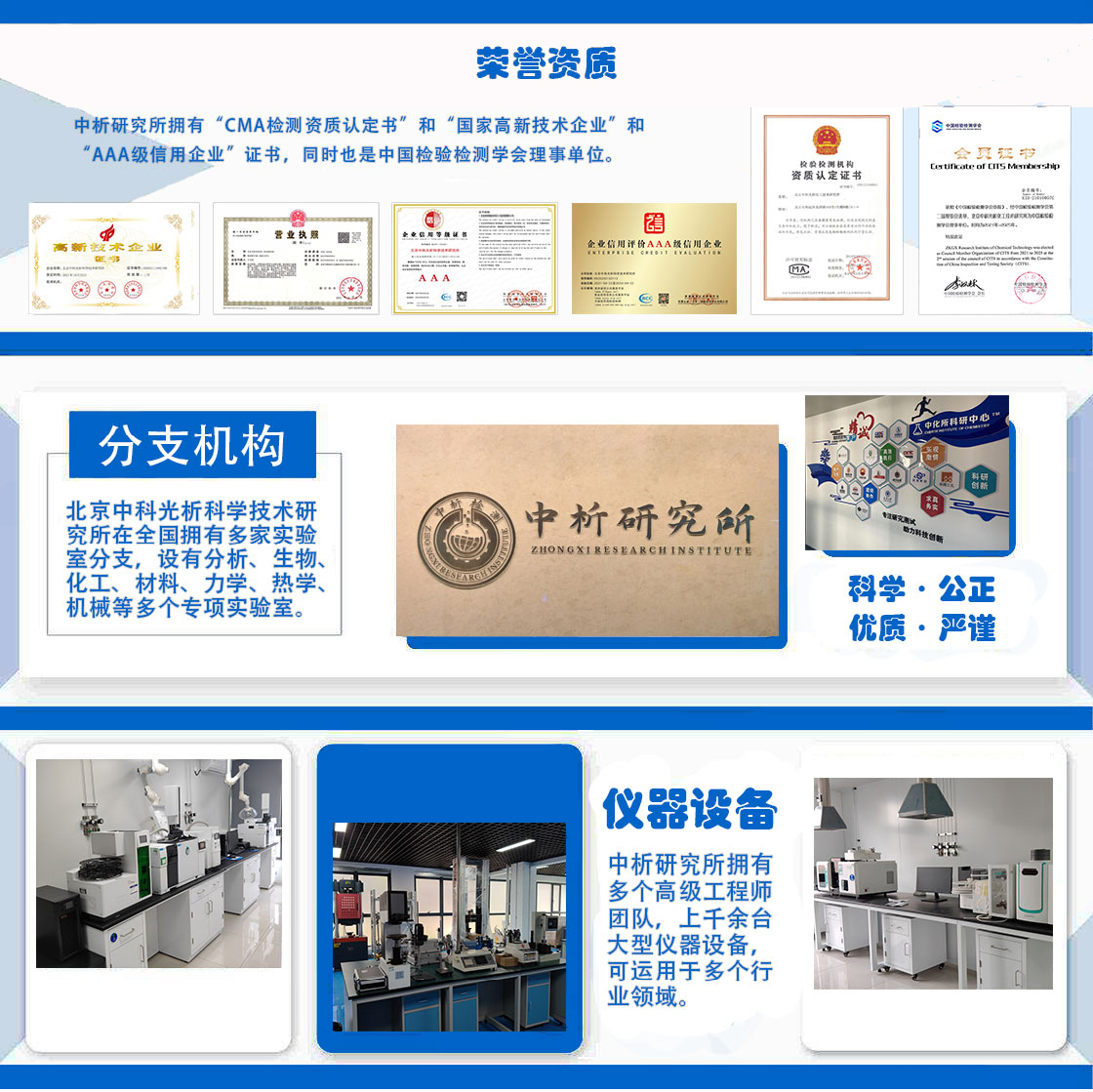
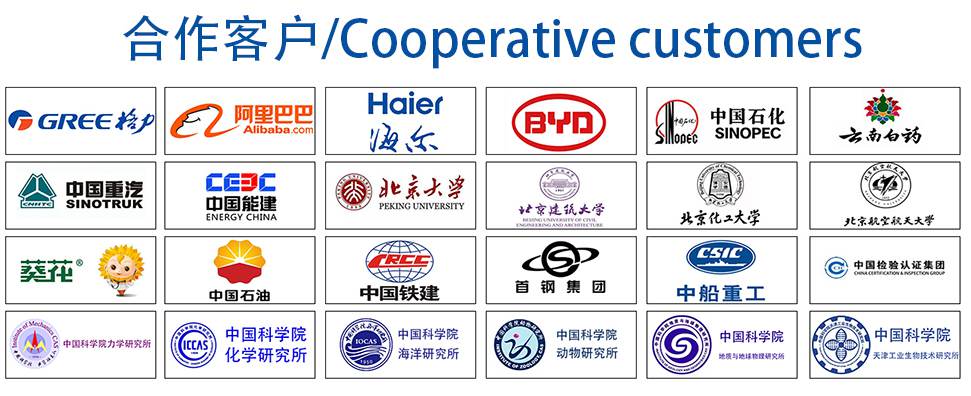