汽车车轮表面油漆涂层检测的重要性
在汽车制造与维护领域,车轮不仅是车辆行驶的核心部件,其外观品质也直接影响用户对品牌的信任度。表面油漆涂层作为车轮的第一道“保护屏障”,需兼具防腐蚀、耐候性、抗冲击及美观性等多重功能。涂层质量缺陷可能导致氧化锈蚀、漆面剥落等问题,进而引发安全隐患或降低产品使用寿命。因此,通过科学的检测项目对车轮涂层进行系统性评估,已成为汽车制造产业链中不可或缺的环节。
核心检测项目及技术标准
1. 涂层附着力测试
采用划格法(ASTM D3359)或拉开法(ISO 4624),通过刀具在涂层表面划出网格后观察脱落面积,评估涂层与金属基底的结合强度。行业标准通常要求附着力等级≥4B(划格法)。
2. 涂层厚度检测
利用涡流测厚仪(非磁性基材)或超声波测厚仪,测量干膜厚度(DFT)。乘用车轮涂层总厚度一般需达到80-120μm,且同一圆周面厚度偏差不超过±15%。
3. 表面外观检测
通过目视检查结合影像分析系统,识别橘皮、流挂、颗粒、气泡等缺陷。高端车型要求涂层表面粗糙度Ra≤0.3μm,光泽度需满足60°角测量≥90GU。
4. 耐腐蚀性能测试
执行中性盐雾试验(NSS)或循环腐蚀试验(CCT),依据ISO 9227标准进行500-1000小时加速老化,要求涂层无起泡、开裂且划痕处单边扩蚀≤2mm。
5. 耐候性检测
通过氙灯老化试验(SAE J2527)或紫外线加速老化测试,模拟5年自然暴晒环境,检测涂层色差(ΔE≤1.5)及光泽保持率(≥80%)。
6. 抗冲击测试
采用落球冲击试验(ASTM D2794),用1kg钢球从50cm高度自由下落,评估涂层抗机械冲击能力,要求冲击区域无裂纹或剥落现象。
7. 色差与光泽度检测
使用分光测色仪测量涂层与标准色板的色差(ΔE),工业级设备可精确到0.1ΔE值,确保批次间颜色一致性。
检测技术发展趋势
现代检测已融合机器视觉(AOI)与人工智能技术,通过高精度CCD相机捕捉微米级缺陷,结合大数据算法实现实时质量判定。例如,某德系车企的智能检测线可实现每分钟12只车轮的360°全自动扫描,缺陷识别准确率达99.7%。
常见问题与解决方案
针对涂层附着力不足问题,需优化前处理工艺(如磷化时间控制);厚度不均可通过静电喷涂参数调整改善;而抗UV性能提升则建议采用含氟树脂改性涂料。通过系统检测数据分析,可有效降低质量不良率30%-50%。
行业应用价值
完善的涂层检测体系不仅能预防售后索赔风险,更能推动车企实现全生命周期质量管理。某国际轮胎企业统计显示,严格执行涂层检测标准可使车轮产品保修期内故障率下降42%,同时提升终端市场溢价能力达15%-20%。
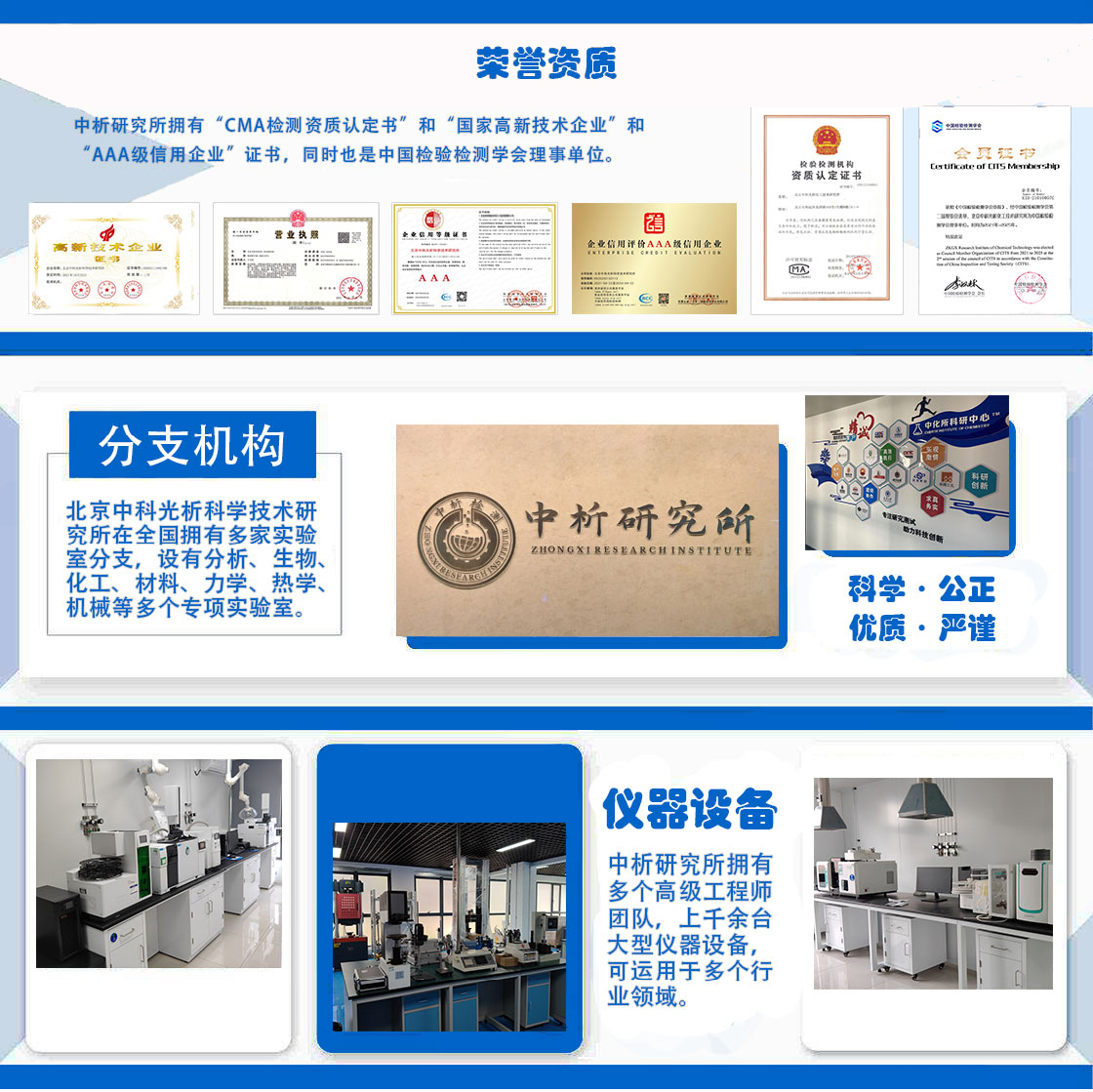
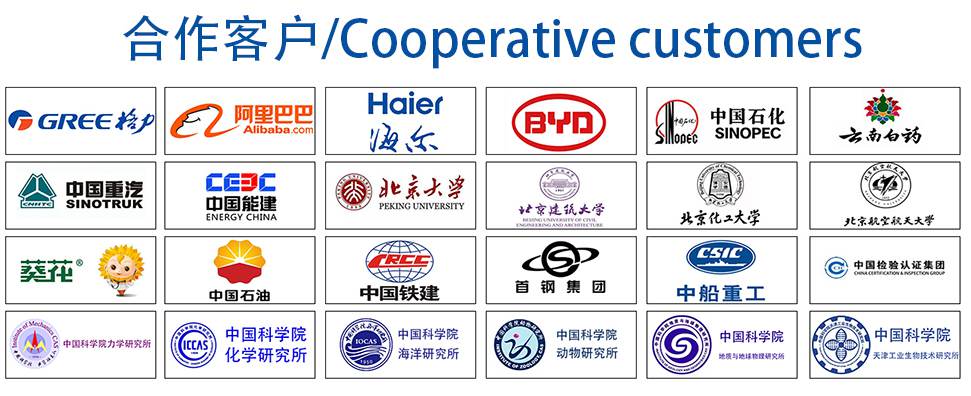