石油化工钢结构防腐蚀涂料检测的重要性
石油化工行业的生产环境通常具有高温、高湿、强腐蚀性等特点,其钢结构设施(如储罐、管道、反应塔等)长期暴露在酸性气体、盐雾、化学介质等恶劣条件下,极易发生腐蚀。防腐蚀涂料作为保护钢结构的第一道屏障,其性能直接影响设施的使用寿命和安全性。若涂料质量不达标或施工工艺存在缺陷,可能导致涂层剥落、基材锈蚀,甚至引发泄漏、爆炸等重大事故。因此,对防腐蚀涂料进行系统性检测是确保石油化工装置安全稳定运行的关键环节。
防腐蚀涂料检测的核心项目
1. 涂层厚度检测
采用磁性测厚仪或超声波测厚仪,依据GB/T 4956标准测量干膜厚度(DFT)。石油化工钢结构通常要求底漆、中间漆和面漆的总厚度达到200-400μm,特殊区域需更高标准。过薄可能导致防护不足,过厚则易产生开裂风险。
2. 附着力测试
通过划格法(ASTM D3359)或拉开法(ISO 4624)评估涂层与基材的结合强度。石化设施要求附着力不低于5MPa,关键部位需达到8MPa以上。测试中需注意基材表面处理质量(如Sa2.5级喷砂)对结果的影响。
3. 耐化学性试验
模拟工况环境,将试样浸泡于特定浓度的酸(如H2SO4)、碱(如NaOH)、有机溶剂(如二甲苯)中,按GB/T 9274标准评估涂层的溶胀、变色、起泡等现象。石化涂料需满足720小时无显著劣化的要求。
4. 盐雾试验
依据ASTM B117进行中性盐雾测试,验证涂层在Cl-环境下的抗腐蚀能力。石化海洋平台等设施通常要求3000小时无基材锈蚀,涂层起泡等级≤2级(ASTM D714)。
5. 耐候性检测
通过QUV加速老化试验(ASTM G154)模拟紫外线、温湿度循环作用,评估涂层抗粉化(ASTM D4214)、保光率(GB/T 9754)等性能。沿海石化区面漆需满足2000小时老化后保光率≥80%。
6. 电化学性能测试
采用电化学阻抗谱(EIS)和开路电位监测,定量分析涂层的孔隙率与屏障效应。优质环氧富锌底漆的阻抗值应>1×10^9 Ω·cm²(ASTM G106),确保长效阴极保护。
检测流程的规范实施
检测工作需遵循HG/T 20679-2014《化工建筑防腐蚀工程施工质量验收规范》,涵盖材料入场复验、施工过程监控及竣工验收三个阶段。重点把控基材表面清洁度(灰尘≤3级)、涂层连续性(电火花检测电压≥5000V)等指标,并结合红外热像仪进行隐蔽缺陷排查。
结语
石油化工钢结构防腐蚀涂料的系统化检测是保障工业安全的核心技术手段。通过科学的检测方法与严格的质量控制,可显著延长设施寿命、降低维护成本,并为高风险区域的腐蚀防控提供数据支撑。建议企业建立全生命周期检测档案,定期开展涂层健康状态评估,以实现主动式安全管理。
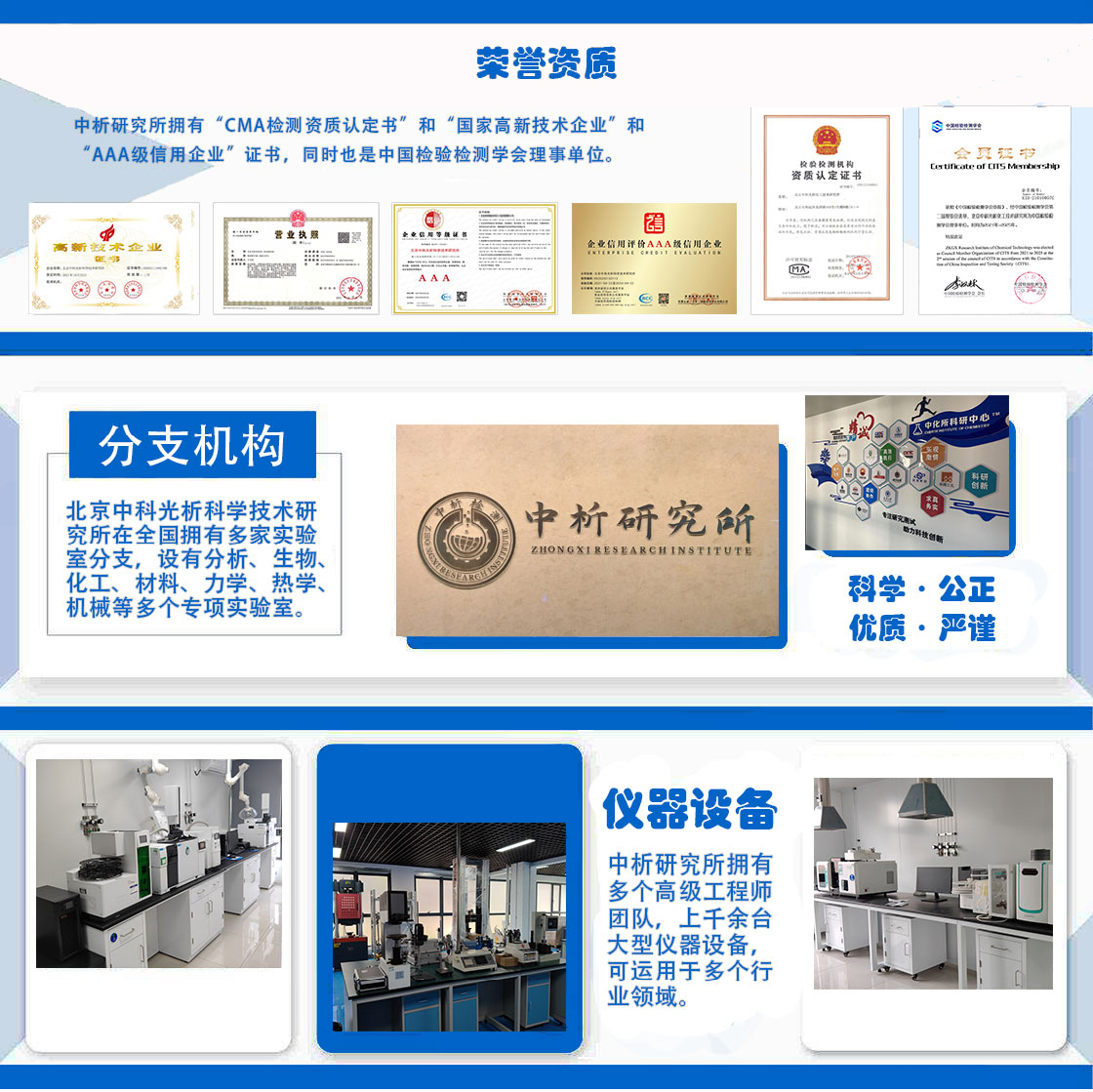
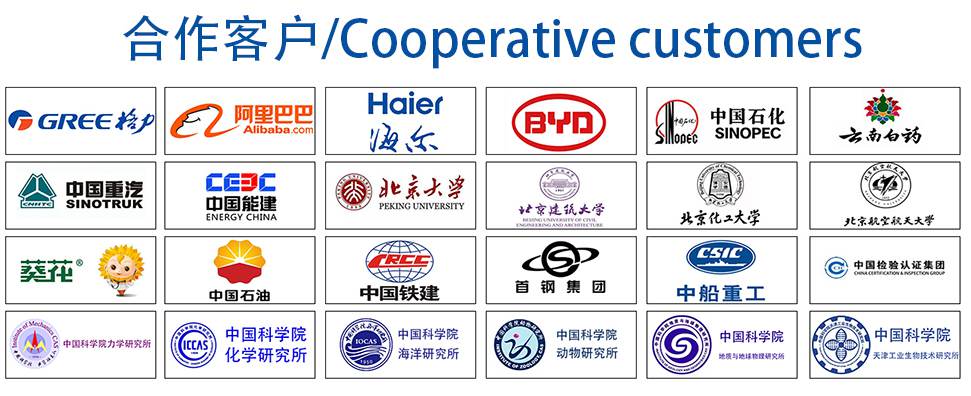