往复运动橡胶密封圈材料检测的重要性
往复运动橡胶密封圈是工业设备中不可或缺的关键部件,广泛应用于液压缸、气动装置、发动机活塞等领域。其核心功能是防止介质泄漏并承受动态压力与摩擦,工作环境通常面临高温、高压、腐蚀性介质和频繁机械运动的考验。因此,材料性能的优劣直接决定了密封圈的使用寿命和系统安全性。为确保产品可靠性,从原材料到成品需通过系统化检测,涵盖物理机械性能、耐介质性、老化特性等多维度测试。严格的材料检测不仅能预防设备故障,还能优化产品设计,降低维护成本。
核心检测项目及方法
1. 物理机械性能测试
硬度、拉伸强度、断裂伸长率是衡量橡胶材料基础性能的核心指标。通过邵氏硬度计可评估材料的抗变形能力,万能材料试验机用于测定拉伸强度(≥15MPa)和断裂伸长率(≥300%),确保密封圈在往复运动中保持结构完整性。压缩永久变形测试(参照GB/T 7759)则模拟长期受压后的弹性恢复能力,要求变形率≤25%。
2. 耐介质性能检测
针对不同工况,需测试材料在液压油、润滑油、酸碱溶液等介质中的耐受性。将试样浸泡于标准介质(如IRM903油)72小时后,检测体积变化率(±5%以内)、硬度变化(±10IRHD以内)及质量损失(≤3%)。特殊场景还需进行低温脆性试验(-40℃/4h)和高温抗溶胀测试(150℃/24h)。
3. 动态密封性能评估
采用模拟往复运动试验台,在设定压力(0-40MPa)、速度(0.5-1.5m/s)和温度(-40-120℃)下进行10^6次循环测试。通过泄漏量监测(≤0.1ml/h)、表面磨损量(≤0.2mm)及摩擦系数变化(波动<15%),验证密封圈的实际工况表现。同步使用红外热像仪分析摩擦生热对材料的影响。
4. 老化与寿命预测
通过热空气老化试验(GB/T 3512)评估材料在150℃/72h后的性能保留率,要求拉伸强度下降≤30%。臭氧老化测试(GB/T 7762)模拟含臭氧环境,观测表面龟裂程度(0级为无裂纹)。结合阿累尼乌斯方程进行加速老化实验,推算材料在常温下的使用寿命(通常≥10年)。
5. 微观结构分析
利用SEM电镜观察填料分散均匀性,防止因团聚导致的应力集中。DSC差示扫描量热法检测玻璃化转变温度(Tg需低于最低工作温度20℃),FTIR红外光谱分析硫化体系完整性,确保交联密度达到最优值(2.5×10^-4mol/cm³±10%)。
检测标准的应用与选择
检测需依据GB/T 3452.1(液压密封件)、ISO 3601(流体动力系统密封件)或ASTM D2000等行业标准。对于汽车领域,需额外满足SAE J200橡胶材料分类要求;医疗设备密封圈则必须通过USP Class VI生物相容性测试。企业应建立基于风险分析的检测方案,结合有限元仿真优化检测项目优先级。
通过系统化的材料检测体系,可精确把控橡胶密封圈的质量边界,推动从经验型制造向数据化质量管控的转型,为高端装备的可靠性提供坚实保障。
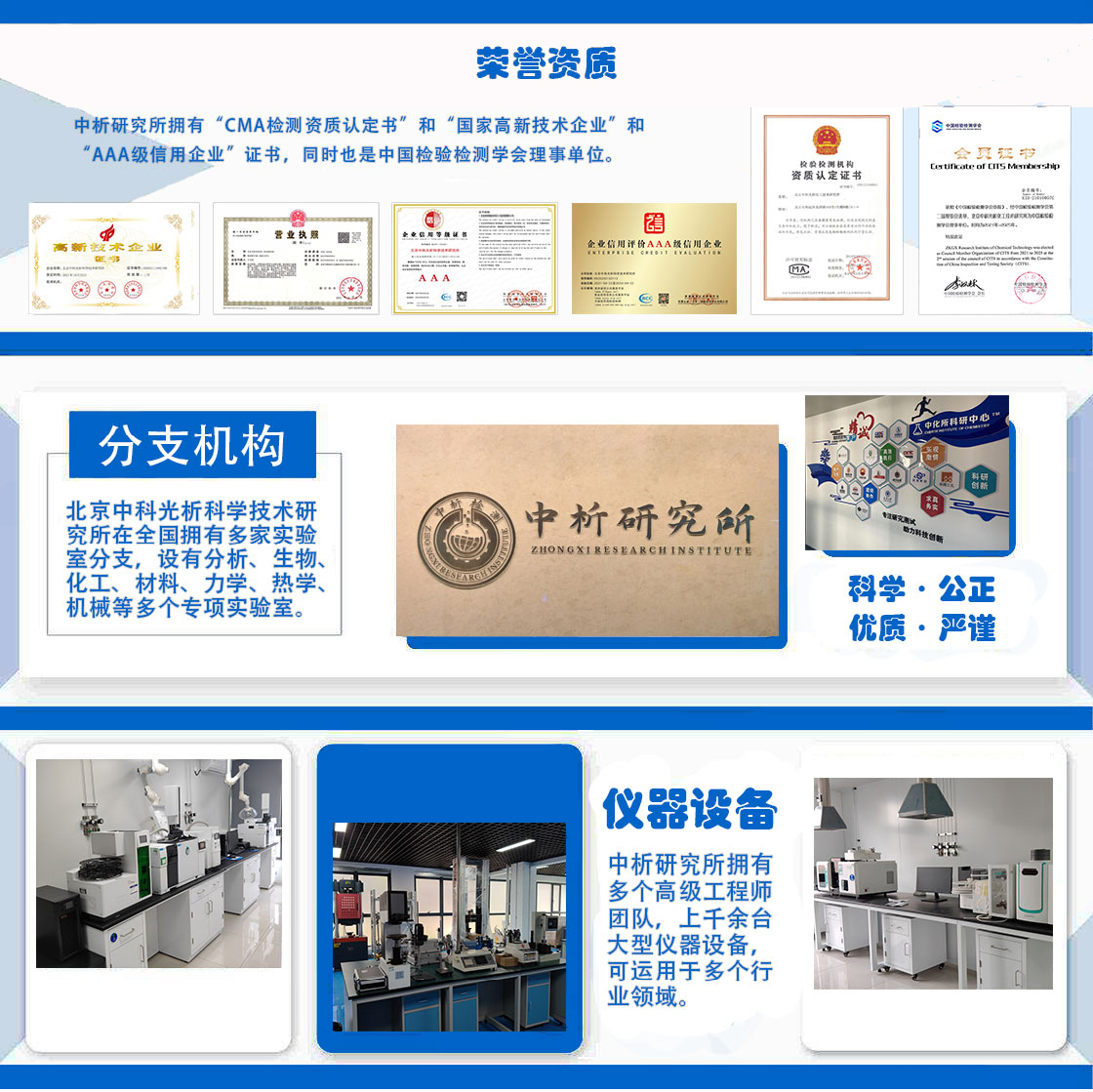
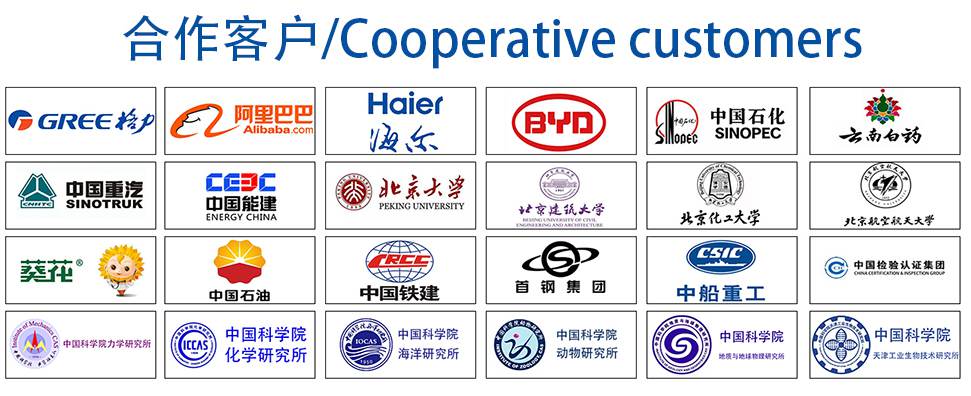