汽车用塑料密封条检测的重要性与必要性
汽车用塑料密封条作为车身结构的重要组成部分,承担着防水、隔音、减震及提升驾乘舒适性的关键作用。随着汽车工业对轻量化、耐候性和环保性的要求不断提高,密封条的材质从传统橡胶逐渐向改性TPE、EPDM等高分子材料过渡。然而,复杂的使用环境(如高低温循环、紫外线照射、化学腐蚀等)和长期机械应力作用可能导致密封条出现老化、变形或开裂等问题。因此,建立系统化的检测体系对保障密封条性能稳定性、延长使用寿命至关重要。通过科学检测可预防因密封失效引发的漏水、风噪、能耗增加甚至安全风险,同时为材料研发和工艺改进提供数据支撑。
核心检测项目分类与标准
1. 尺寸精度与外观检测
使用精密卡尺、投影仪等设备测量密封条的截面尺寸、长度公差及安装配合间隙,确保符合GB/T 3672.1-2002《橡胶制品公差》要求。外观检测需通过目视或光学仪器检查表面是否存在气泡、杂质、划痕及变形缺陷,同时验证密封唇口的几何形状完整性。
2. 物理力学性能测试
• 拉伸强度与断裂伸长率:依据ISO 37标准,在万能材料试验机上以500mm/min速率测试,评估材料抗拉性能
• 压缩永久变形:参照GB/T 7759-2015,将试样压缩至原高度50%后70℃恒温22小时,计算残余变形量
• 撕裂强度:采用直角撕裂法测定材料抗撕裂能力,要求达到QB/T 1130规定值
• 硬度测试:使用邵氏A型硬度计在23±2℃环境下测量,典型值范围为50-80 Shore A
3. 环境适应性试验
• 高低温循环测试:在-40℃至120℃范围内进行100次循环冲击,观察密封条形变恢复能力
• 湿热老化试验:85℃/85%RH环境下持续1000小时,检测质量变化率≤5%
• 紫外线加速老化:通过QUV老化箱模拟5年自然暴晒,评估表面龟裂、粉化程度
• 耐油耐化学性:浸泡于汽油、制动液等介质72小时后检测体积膨胀率,要求≤15%
4. 功能性验证
• 密封性能测试:搭建模拟车门/车窗系统,在3kPa压差下检测漏气量≤15L/min
• 摩擦系数测定:使用滑块法测试与玻璃/金属接触面的动态摩擦系数,需稳定在0.8-1.2范围
• 装配力测试:记录安装过程中的最大插入力和保持力,避免装配困难或脱落风险
检测技术创新趋势
当前检测技术正向智能化、高精度方向发展,包括应用红外热成像技术检测密封条装配均匀性,采用激光扫描三维重建分析压缩回弹性,以及通过有限元仿真预测长期应力松弛特性。同时,行业正推动建立基于大数据的产品全生命周期质量追溯系统,实现从原材料到终端产品的数字化检测闭环管理。
结语
完善的汽车塑料密封条检测体系是保障车辆品质的重要防线。通过涵盖材料特性、机械性能、环境耐受性和功能可靠性的多维度检测,可有效降低产品失效风险。随着新能源汽车对气密性要求的提升和智能座舱的发展,检测标准将持续迭代更新,推动行业向更高性能、更环保的方向迈进。
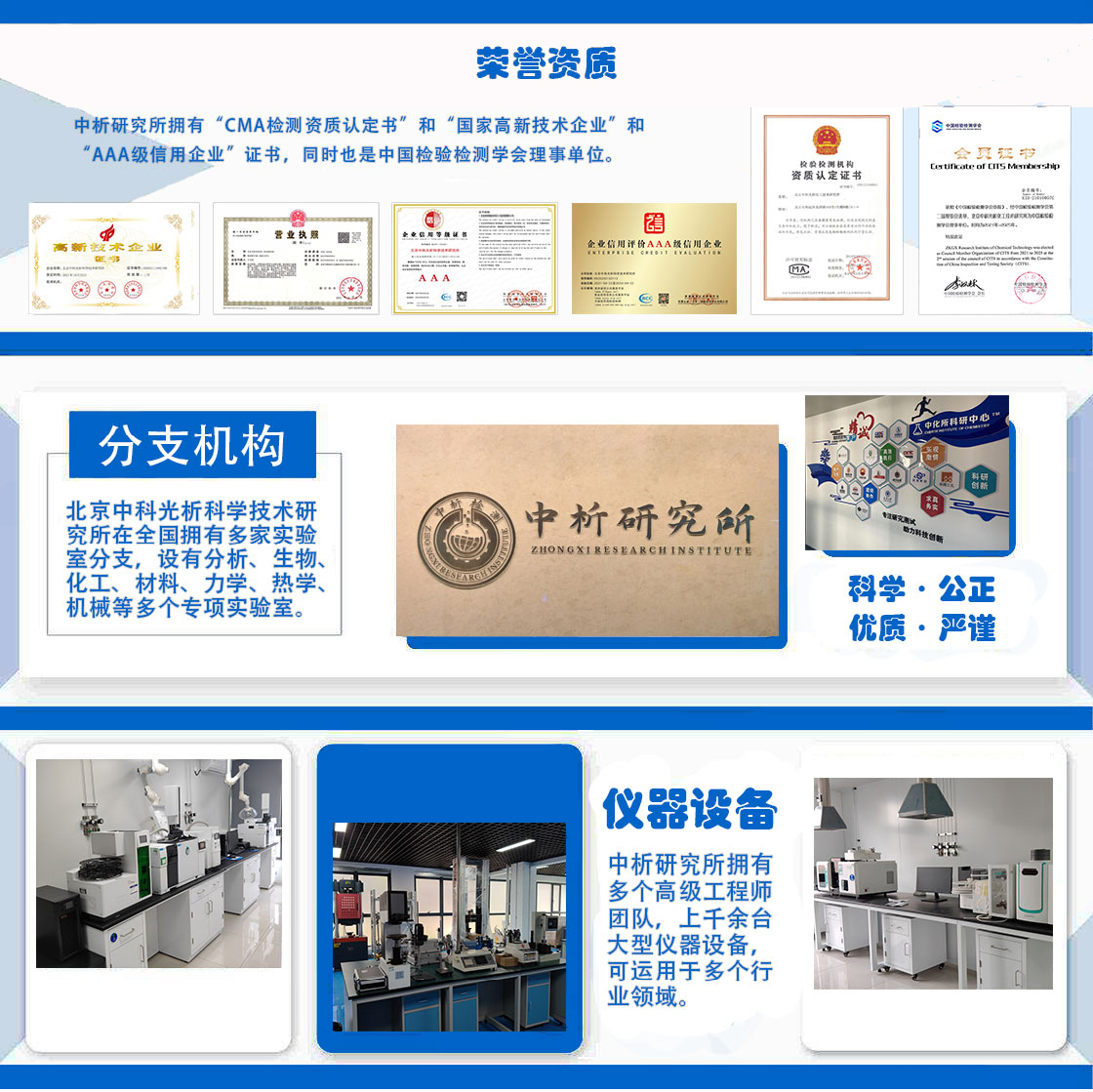
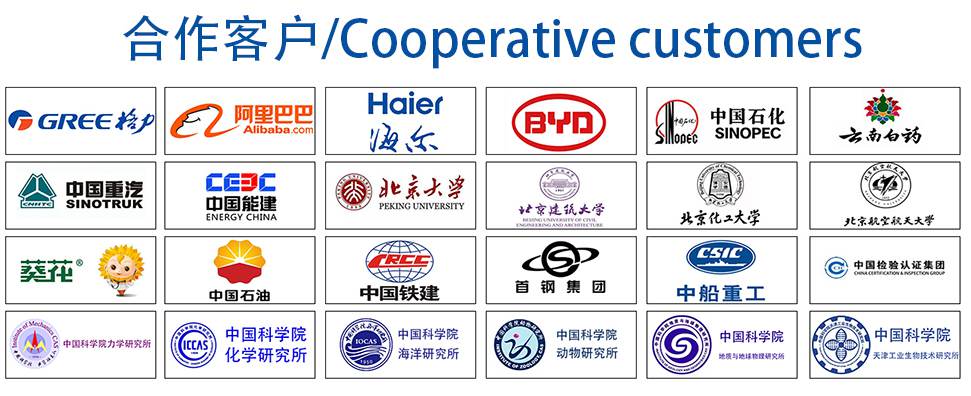