腐蚀测试检测:守护材料寿命的关键防线
在工业制造、航空航天、海洋工程及基础设施领域,材料腐蚀是导致设备失效、结构损毁和安全事故的隐形杀手。腐蚀测试检测作为评估材料耐蚀性能的核心手段,通过模拟不同环境条件下的腐蚀过程,精准定位材料薄弱环节,为产品选材、工艺优化和寿命预测提供科学依据。国际标准化组织(ISO)、美国材料与试验协会(ASTM)等机构已建立超过200项腐蚀测试标准,覆盖从金属到复合材料的全品类检测需求。
核心检测项目体系
盐雾试验
采用5%氯化钠溶液模拟海洋大气环境,通过中性盐雾(NSS)、乙酸盐雾(AASS)和铜加速乙酸盐雾(CASS)三种模式,评估镀层、涂层及金属基体的耐腐蚀性能。ASTM B117和ISO 9227标准规定试验箱需保持35℃恒温,喷雾沉降量1-2ml/80cm²·h,是汽车零部件、电子元器件的必检项目。
电化学测试
通过极化曲线测试(Tafel分析)、电化学阻抗谱(EIS)等技术,定量测定材料的腐蚀电流密度、极化电阻等关键参数。可精准识别304不锈钢的点蚀电位、铝合金的晶间腐蚀倾向,检测精度达到微安级,广泛应用于新能源电池集流体、油气管道材料的研发验证。
循环腐蚀试验
结合湿热、干燥、盐雾等多环境交替模拟,典型循环包含:4小时盐雾→4小时湿度95%RH→16小时干燥。相比传统盐雾试验,其检测结果与户外暴露试验的相关性提升60%,已成为汽车主机厂验证车身镀锌板防腐性能的首选方法。
应力腐蚀开裂测试
采用U型弯曲试样或预裂纹试样,在特定介质中施加80%以上屈服强度的持续载荷,检测高强度钢、铝合金等材料在拉应力与腐蚀介质协同作用下的断裂敏感性。参照NACE TM0177标准,试验溶液需精确控制硫化氢浓度与pH值,是油气钻采设备安全评估的核心指标。
微生物腐蚀检测
针对硫酸盐还原菌(SRB)、铁氧化菌等微生物代谢产物引发的腐蚀,通过荧光显微镜计数、ATP生物发光法量化微生物活性,结合表面形貌分析(SEM/EDS)鉴定生物膜导致的点蚀特征。特别是在深海管道、核电站冷却系统中,该检测可提前预警80%以上的生物腐蚀风险。
创新检测技术发展
随着微区腐蚀分析技术的突破,扫描开尔文探针(SKP)可实现纳米级电位分布测绘,激光诱导击穿光谱(LIBS)能实时监测腐蚀产物的元素演变。智能腐蚀监测系统集成无线传感器网络,可对化工厂反应釜、跨海大桥锚链等关键部位进行365天不间断腐蚀速率追踪,数据采集频率达每分钟1次,预警准确率超过95%。
腐蚀测试检测正在从单一环境模拟向多场耦合检测演进,通过建立温度-湿度-应力-化学介质的四维检测模型,可精确复现南海钻井平台、高原输电线塔等极端环境下的材料腐蚀行为,为重大工程装备提供全生命周期的腐蚀防护解决方案。
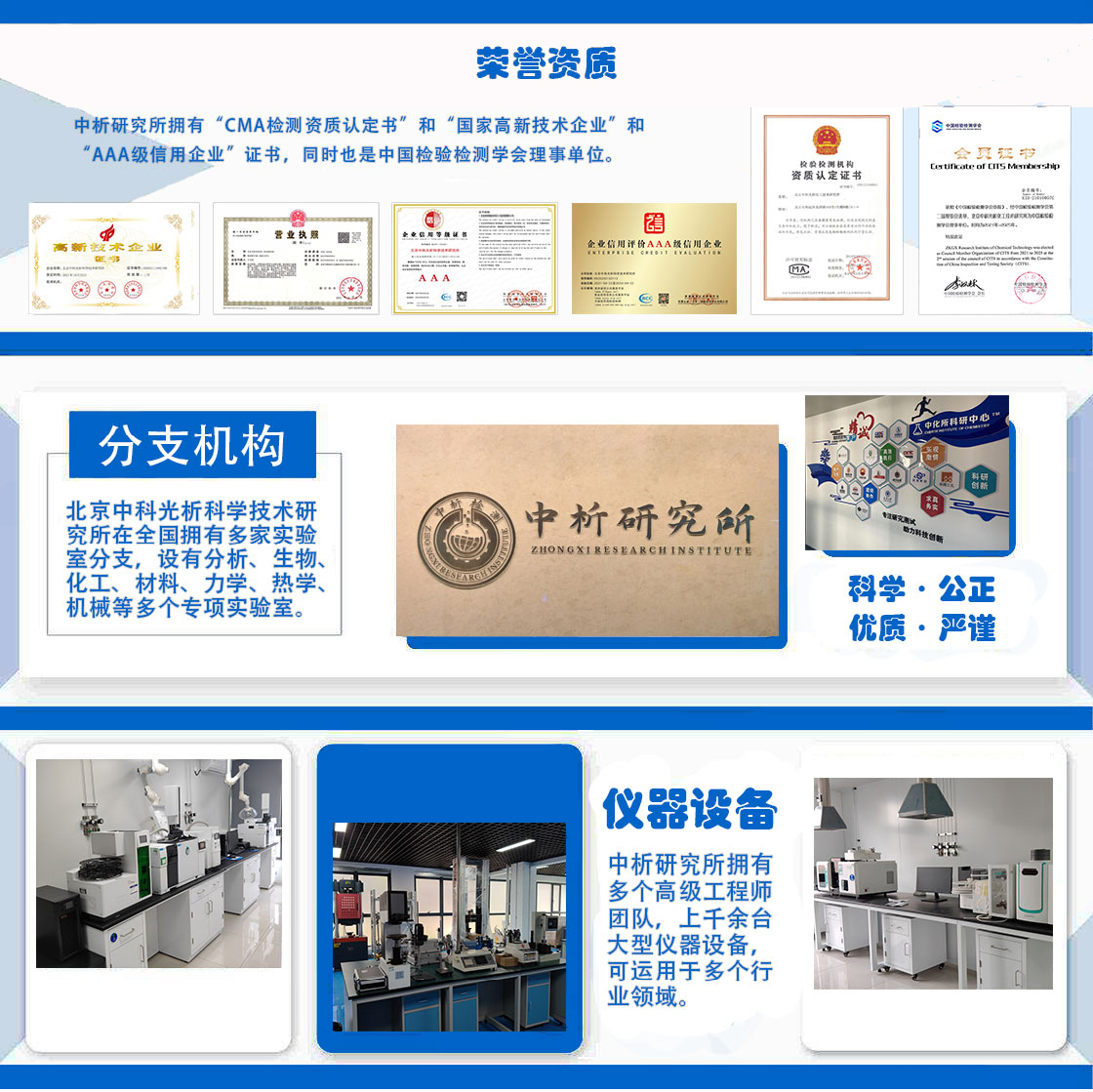
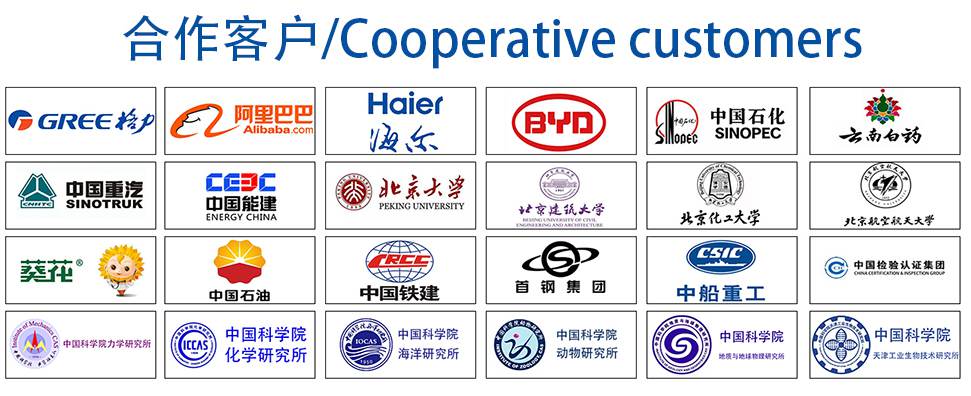