皱缩检测的核心价值与应用场景
皱缩检测是工业制造与材料科学领域的重要质量控制手段,主要针对金属冲压件、注塑件、复合材料制品等在成型过程中产生的表面凹陷或体积收缩缺陷。这类缺陷可能引发应力集中、强度下降等问题,直接影响产品使用寿命和安全性能。根据ASTM E155标准,皱缩率超过0.5%即被视为不合格,在航空航天、汽车制造等对精密性要求严苛的行业,检测精度要求甚至达到微米级。
核心检测项目体系
现代皱缩检测已形成多维度的项目体系:
1. 三维形貌扫描分析
采用白光干涉仪或激光扫描仪获取工件表面三维点云数据,通过Geomagic Control X等专业软件进行三维重建,对比设计模型计算局部曲率变化。某汽车主机厂实测显示,该方法可捕捉深度0.02mm的微皱缩,检测效率比传统卡尺测量提升80%。
2. 残余应力分布检测
运用X射线衍射法(XRD)或超声临界折射纵波法(LCR波)测定材料内部应力状态。某航空铝合金构件检测案例中,通过测量V形槽区域的残余应力梯度,成功预测了服役过程中的皱裂风险。
3. 金相组织观测
对可疑区域进行截面取样,经镶嵌、抛光、腐蚀处理后,使用扫描电镜(SEM)观察晶粒变形情况。某3C产品镁合金外壳分析发现,皱缩区晶粒长宽比达到3:1,显著高于正常区域1.5:1的水平。
4. 热力学特性监测
通过差示扫描量热仪(DSC)测定材料玻璃化转变温度(Tg),结合红外热像仪记录成型冷却过程中的温度场变化。某注塑企业通过优化模具冷却水道布局,使聚碳酸酯件皱缩率从1.2%降至0.3%。
智能检测技术演进
当前检测体系正在向智能化方向升级:基于深度学习的视觉检测系统可实现每分钟120件的高速在线检测;工业CT与数字孪生技术结合,能构建缺陷演变预测模型。某新能源电池壳体生产线应用多传感器融合检测后,不良品拦截率提升至99.7%,质量成本降低42%。
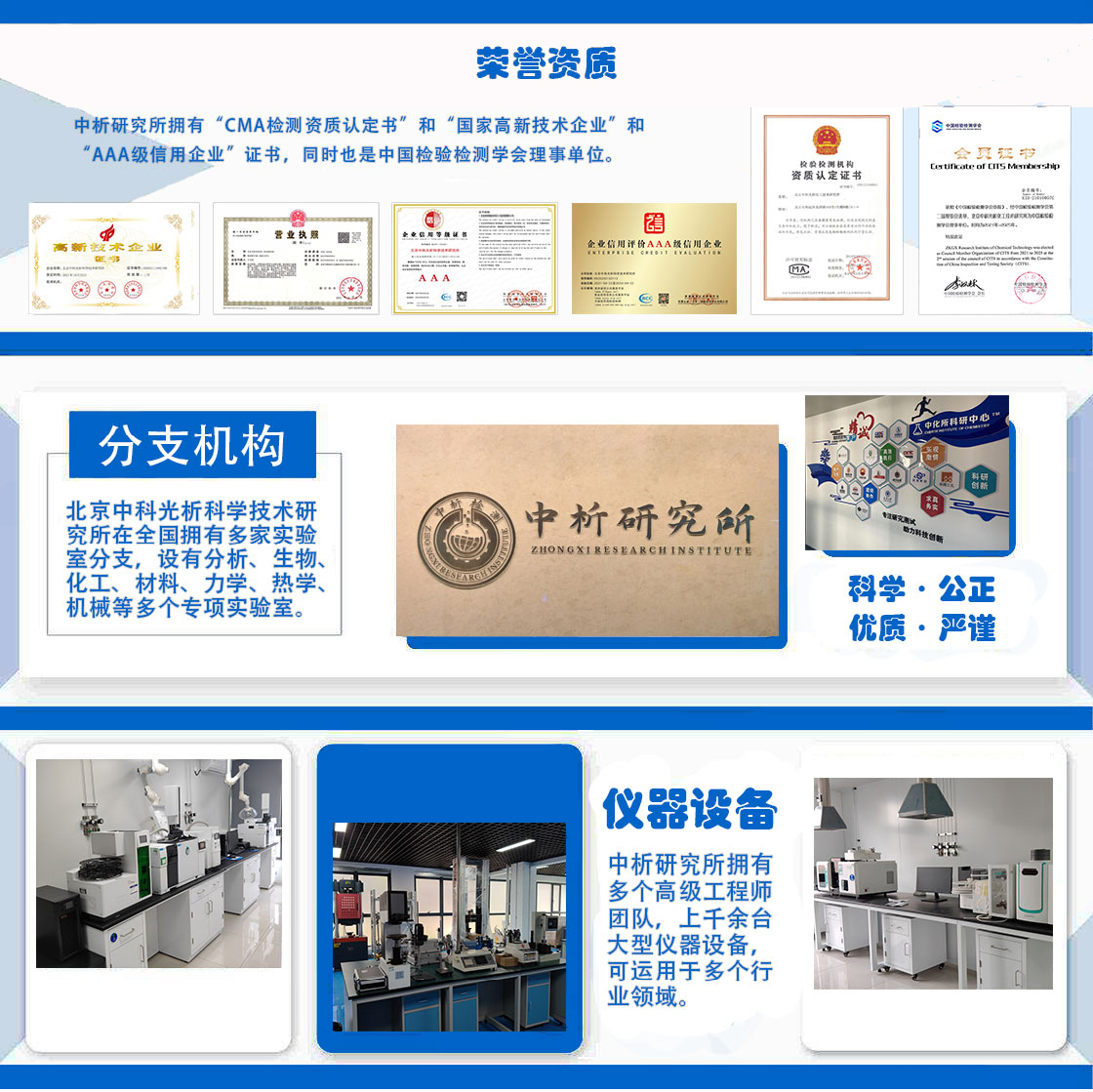
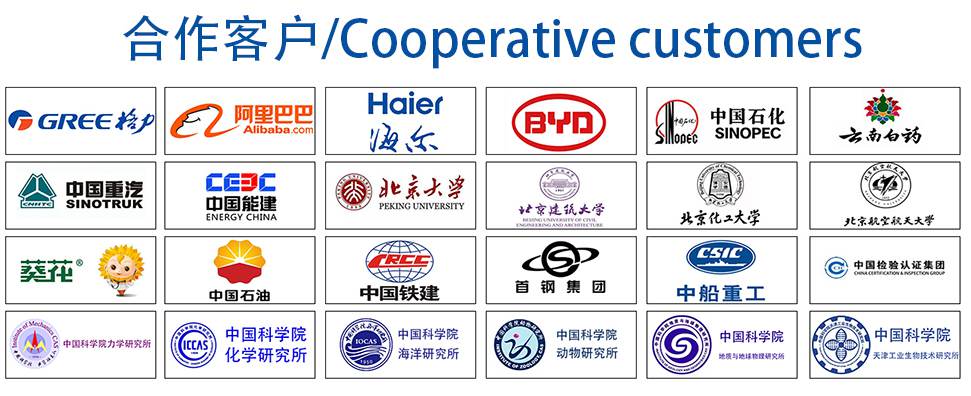