钛铁检测项目及技术要点解析
钛铁合金作为冶金工业中重要的合金添加剂,其质量直接影响钢铁产品的机械性能、耐腐蚀性和高温稳定性。根据GB/T 3282-2023《钛铁》标准要求,正规检测需覆盖化学成分、物理性能、环保指标等多个维度,配合XRF光谱法、ICP-OES等齐全检测手段,确保产品符合冶金、航空航天、化工等领域的特殊要求。
核心检测项目分类
1. 化学成分分析
采用X射线荧光光谱仪(XRF)测定总钛(Ti)含量(25-75%)、铁(Fe)基准值(余量),同步检测铝(Al:0.5-5.0%)、硅(Si:0.5-4.0%)、碳(C≤0.20%)等元素。对磷、硫等有害杂质需进行化学滴定法精准测定,确保P≤0.05%、S≤0.04%。
2. 物理性能测试
通过激光粒度分析仪测定0.2-50mm的颗粒分布,采用真密度仪检测6.5-7.5g/cm³的密度区间。布氏硬度检测需在HRB40-60范围内,同步进行500℃高温稳定性试验。
3. 金相组织检测
使用500倍金相显微镜观察TiFe₂、FeTi相分布,评估晶粒尺寸(10-50μm)、孔隙率(≤3%)等指标。电子探针微区分析可检测微量元素偏析情况。
特色检测技术应用
最新检测体系新增电感耦合等离子体质谱(ICP-MS)法,可检测0.1ppm级的稀土元素残留。动态热分析法(DTA)可精准测定1180-1250℃的熔程特性,结合真空熔样技术显著提升检测精度。部分高端实验室已配置原位XRD装置,实现相变过程的实时监控。
质量控制关键节点
原料阶段需重点监控海绵钛(Ti≥99%)和废钢的杂质含量,熔炼过程实行氧含量在线监测(≤800ppm),成品按5%比例进行破坏性检测。通过建立钛铁合金的数字化质量追溯系统,可实现从原料到成品的全流程数据监控。
权威检测机构应同时具备CMA、 双重认证,配备三级取样制(粗破→中碎→细磨)和专属检测数据库。建议生产企业定期进行ASTM E1941标准比对试验,确保检测结果国际互认。
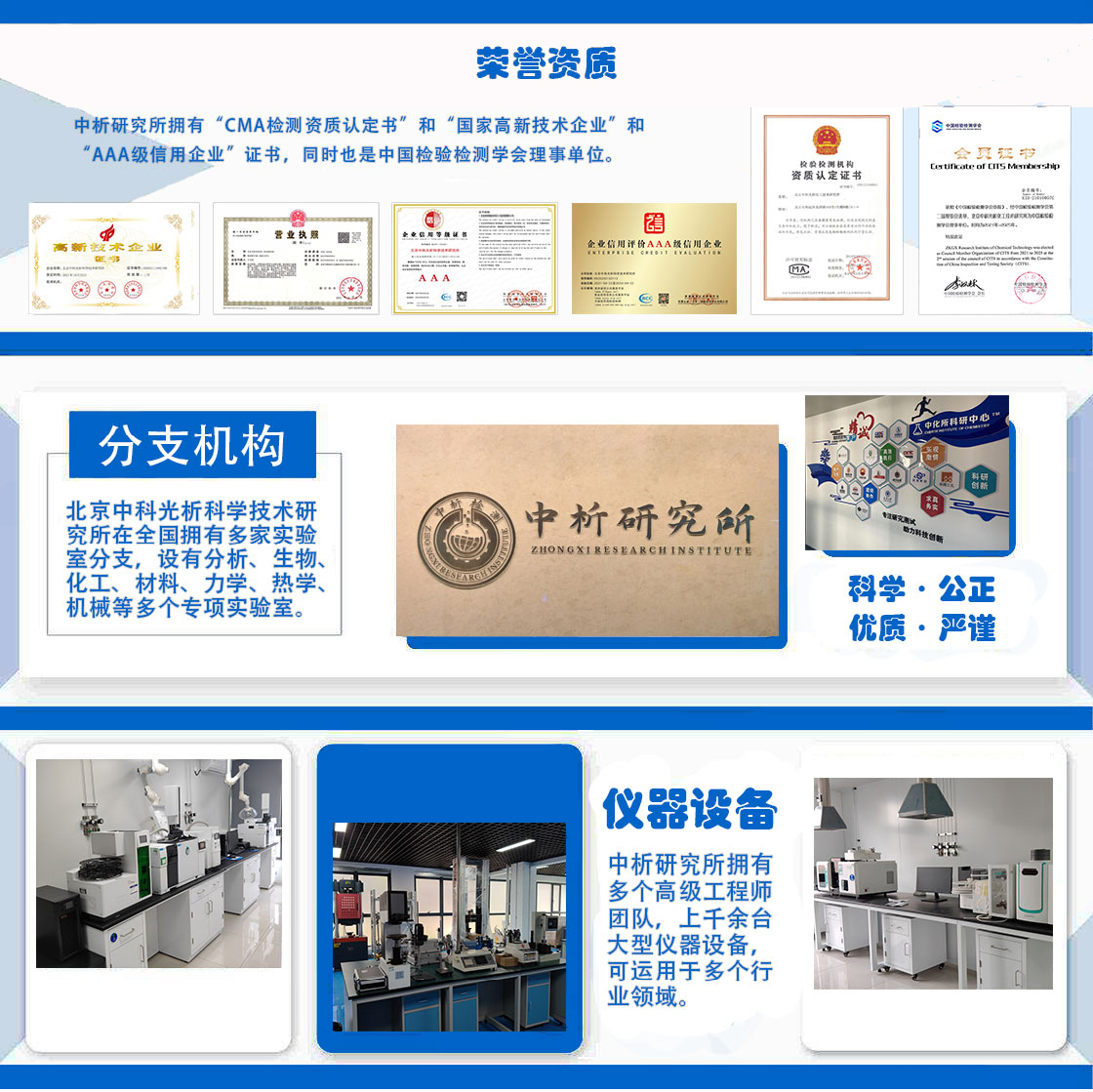
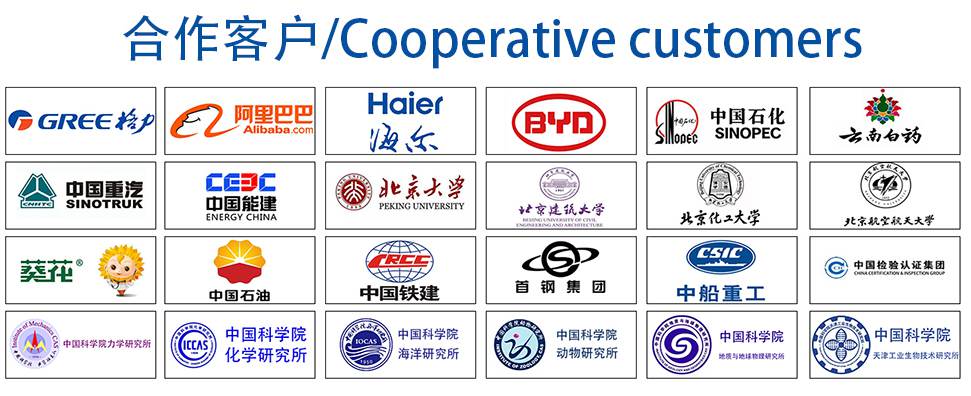