天然气类检测的必要性与核心项目
天然气作为清洁能源的重要组成部分,其质量安全直接影响工业生产效率、民用燃气安全和环境保护效果。根据国家能源局统计,2022年我国天然气消费量突破3600亿立方米,庞大的使用规模对检测技术提出了更高要求。天然气类检测通过科学手段对气体成分、污染物含量及物理特性进行系统分析,为输送安全、燃烧效能评估和环保合规提供数据支撑,已成为能源行业质量管理体系的关键环节。
核心检测项目及技术标准
1. 成分分析检测
采用气相色谱-质谱联用技术(GC-MS)测定甲烷(CH₄)、乙烷(C₂H₆)、丙烷(C₃H₆)等主要烃类组分含量,执行GB 17820-2018《天然气》标准。重点监控氮气(N₂)、二氧化碳(CO₂)等不可燃气体比例,其中CO₂含量需控制在3%以下以保证燃烧效率。
2. 硫化物专项检测
使用紫外荧光法检测总硫含量,硫化氢(H₂S)采用碘量法测定,检测限达0.1mg/m³。GB/T 11060-2020规定H₂S浓度应≤20mg/m³,有机硫(如硫醇、硫醚)总量需≤250mg/m³,有效预防管道腐蚀和大气污染。
3. 热值测定与密度检测
依据ISO 6976标准,通过弹式热量计测定高位热值(39-42MJ/m³为合格区间),同时采用振动管密度仪测量气体密度(0.65-0.75kg/m³正常范围),为燃气计价和燃烧设备选型提供依据。
4. 水分及露点监测
配备冷镜式露点仪检测水蒸气含量,燃气管道输送要求水露点低于输送温度5℃以上。依据SY/T 7507标准,压力露点检测范围覆盖-50℃至+20℃,确保无液态水析出风险。
5. 痕量杂质分析
运用激光光谱技术检测汞(Hg)含量(要求≤0.01μg/m³),采用氧弹法测定机械杂质含量。重点关注粉尘粒径分布(>5μm颗粒需过滤清除),防止燃气轮机等精密设备磨损。
质量控制与行业应用
检测过程严格执行 -CL01:2018体系要求,实验数据需通过三次平行测定保证重复性误差<2%。针对不同应用场景实施差异化检测:LNG接收站侧重冷剂残留检测,城市燃气管网强化硫化物监控,化工厂原料气需增加氨(NH₃)等碱性物质检测。齐全检测技术的应用使我国天然气质量合格率从2015年的92.6%提升至2023年的98.3%,有效保障了能源安全与环保达标。
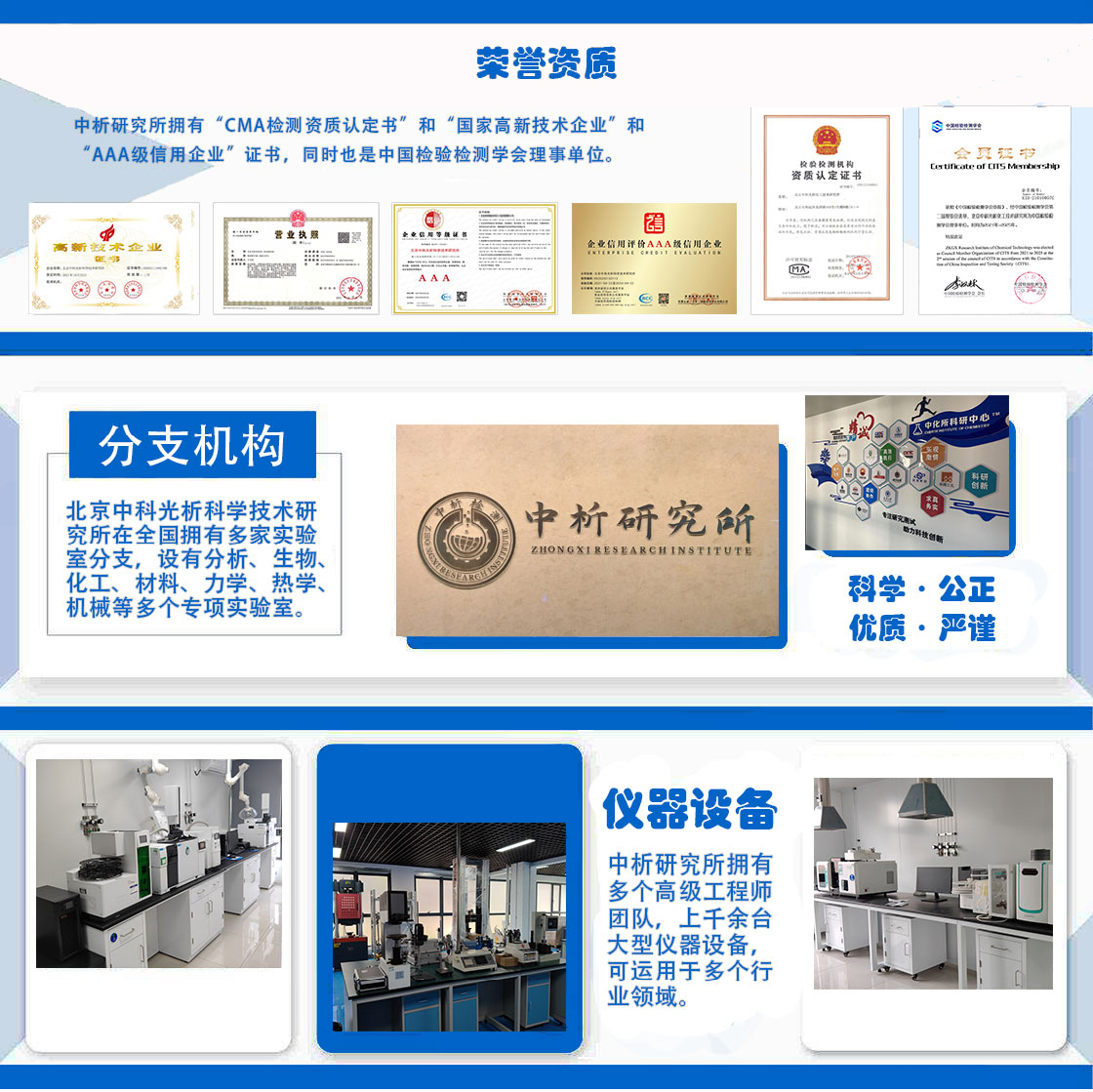
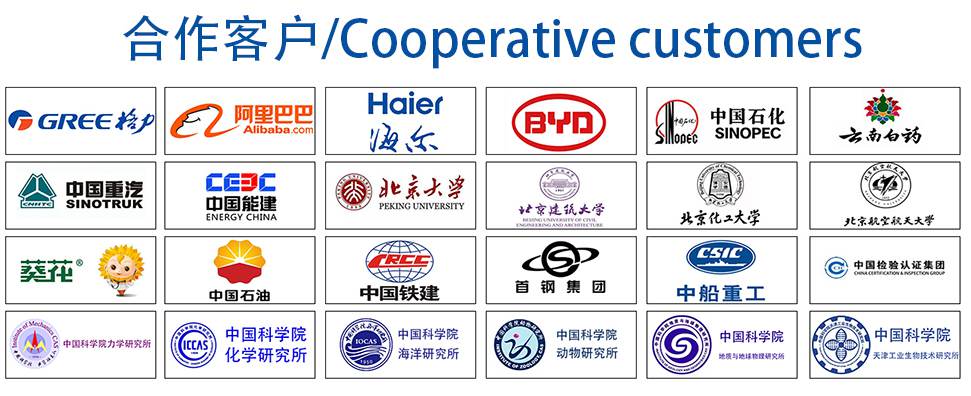