客车电涡流缓速器检测的重要性与核心项目
电涡流缓速器作为客车辅助制动系统的关键部件,在车辆减速、长下坡工况及紧急制动中发挥着重要作用。其通过电磁感应原理将动能转化为热能,有效降低传统摩擦制动器的负荷,提升行车安全性和制动系统寿命。然而,长期使用可能导致缓速器性能衰减或部件损坏,因此定期检测成为保障车辆安全运营的核心环节。检测需覆盖电气性能、机械结构、热管理效率及控制系统的可靠性,结合行业标准(如JT/T 721《客车电涡流缓速器》)进行全面评估。
核心检测项目及技术要求
1. 电气系统检测
包括线圈绝缘电阻测试(要求≥5MΩ)、绕组匝间短路检测、磁轭与转子间隙测量(标准值0.8-1.2mm)以及控制器输出电压稳定性验证。需使用兆欧表、万用表和示波器对缓速器的工作电流、电压波形进行动态分析,确保电磁场生成效率符合设计值。
2. 机械性能检测
重点检查转子盘径向跳动量(允许误差≤0.1mm)、轴承游隙(轴向间隙≤0.3mm)以及散热叶片完整性。通过振动测试仪监测运行时的异常振动频率,同时对安装支架的紧固扭矩进行复验(通常为120-150N·m)。
3. 制动效能测试
在台架试验中模拟不同转速(500-3000rpm)下的制动力矩输出,要求最大扭矩不低于标称值的90%。通过热电偶监测制动盘表面温度分布,连续制动时温升应≤280℃且无局部过热现象。同步检测制动响应时间,要求控制器指令到产生90%最大扭矩的时间≤0.5秒。
4. 热管理系统检测
评估强制风冷系统的风量(≥800m³/h)和导流罩密封性,使用红外热像仪监测散热通道的温度梯度。水冷型缓速器需检测冷却液流量(≥15L/min)及热交换器效率,确保连续制动工况下的散热能力。
5. 控制系统验证
通过CAN总线分析仪检测控制信号的稳定性和抗干扰能力,验证多级制动档位的线性响应特性。需模拟电压波动(18-32VDC)和温度变化(-40℃至85℃)环境,确保系统在极端条件下的可靠性。
检测流程与结果判定
标准检测流程包括预检目测→静态参数测量→空载试验→负载试验→数据对比分析。检测后需出具包含制动力矩曲线、温升数据、电气参数的综合报告,对转子剩磁量(应≤2mT)、绝缘老化程度等潜在风险进行专项评估。未通过检测的缓速器必须进行针对性维修或更换,复检合格后方可重新投入使用。
通过系统的检测流程和技术指标把控,可有效预防因缓速器失效引发的制动距离延长、热衰退等问题,为客车安全运营提供技术保障。运输企业应建立每12个月或10万公里的强制检测周期,结合日常维护数据实现预测性维护。
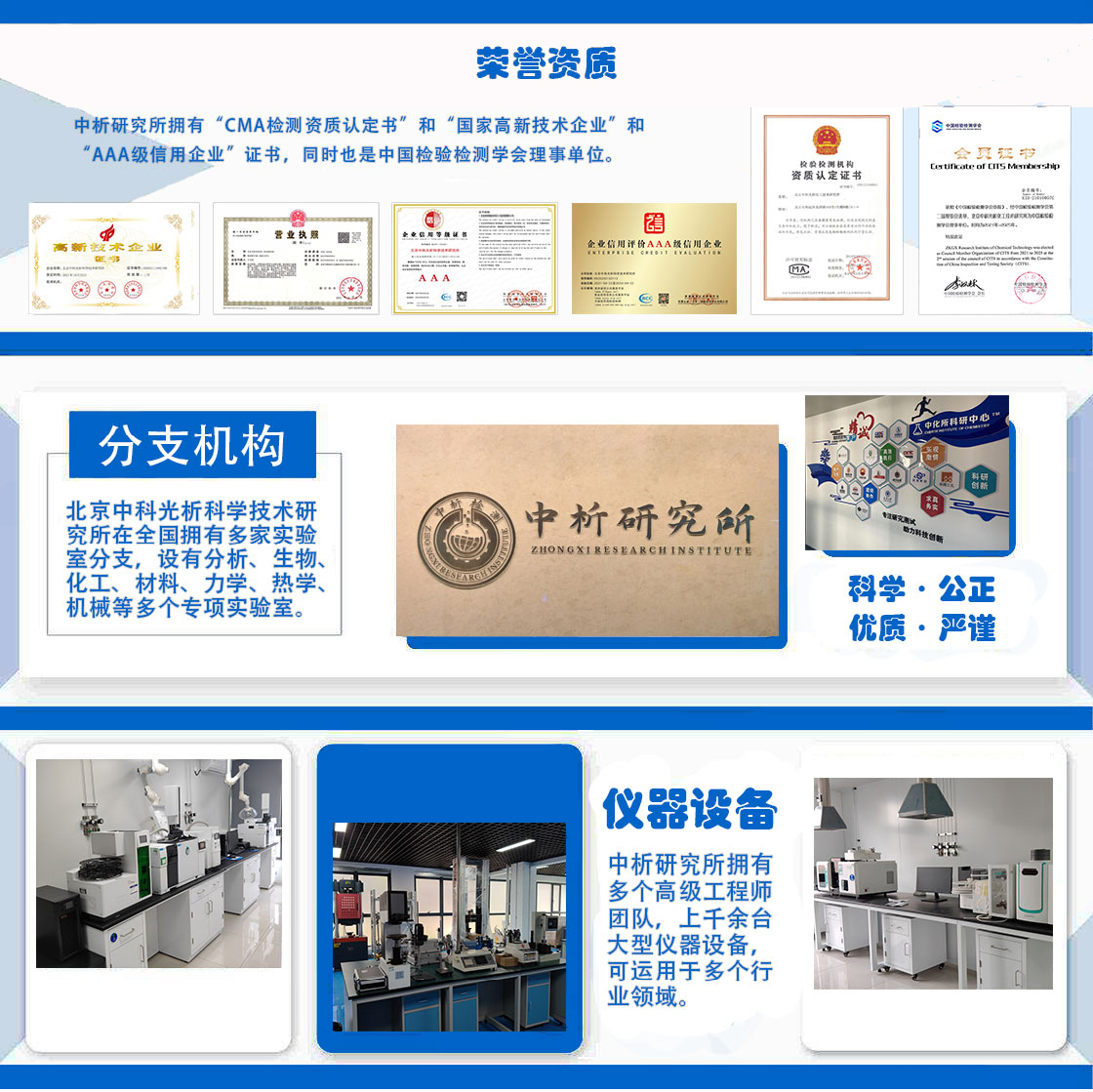
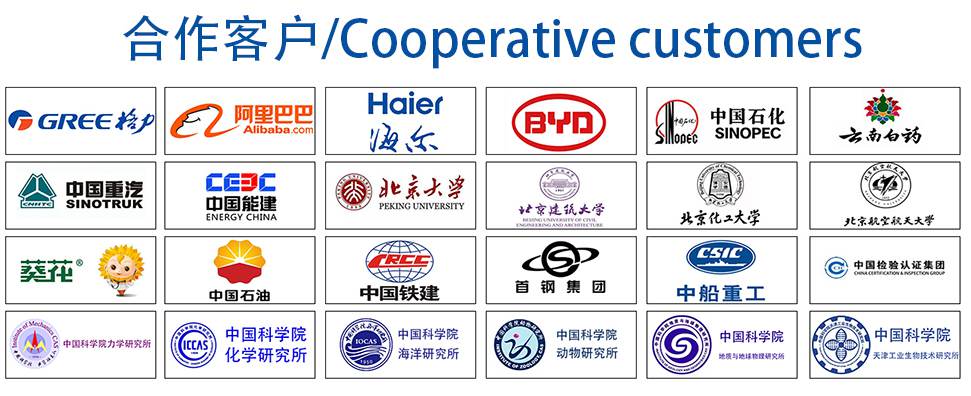