客车车身(安全带固定点)检测的重要性与标准解析
在客车安全性能的评估中,安全带固定点的检测是确保乘客生命安全的关键环节。根据国家标准《GB 14167-2013 汽车安全带安装固定点》和《GB 7258-2017 机动车运行安全技术条件》,安全带固定点需具备足够的强度与稳定性,以在碰撞事故中有效约束乘员身体。客车作为承载多人的公共交通工具,其车身结构的特殊性使得安全带固定点的检测更加复杂,需涵盖材料强度、安装位置、动态响应等多维度指标。
安全带固定点检测的核心项目
安全带固定点检测主要包括以下五个关键项目:
1. 静态强度测试
通过液压缸或专用设备对固定点施加纵向/横向载荷(≥22.2 kN),持续10秒,检测是否存在断裂、变形或松动现象。测试需覆盖所有乘员座椅对应的固定点,并记录位移量是否超出标准限值(≤20 mm)。
2. 动态试验验证
采用碰撞试验台模拟车辆撞击场景,使用假人模型与高速摄像设备观察安全带系统在紧急制动或碰撞时的动态响应。重点监测固定点的位移轨迹、能量吸收特性及连接部位的应力分布。
3. 几何尺寸与位置精度
根据ISO 3833标准,使用激光扫描仪或三坐标测量机对固定点的安装位置进行三维标定,确保Z向(垂直方向)间距≥350 mm,且与座椅中心线的横向偏差≤50 mm。同时检查固定螺栓的规格、拧紧力矩是否符合设计要求。
4. 材料性能分析
对固定点周边车体结构(如立柱、地板加强梁)进行金相检测,验证钢材抗拉强度是否≥340 MPa,并对焊接区域进行超声波探伤,确保焊缝熔深≥板厚的80%且无气孔、夹渣等缺陷。
5. 环境耐久性测试
通过盐雾试验(500小时)和温度循环试验(-40℃~80℃交替100次),评估固定点金属件的耐腐蚀性与热膨胀系数匹配性,避免因环境老化导致结构失效。
检测流程与行业应用
检测机构需依据JT/T 1094-2016《营运客车安全技术条件》建立标准化流程:首齐全行目视检查确认固定点无锈蚀或改装痕迹,再依次完成静动态试验、材料分析及复检。检测周期建议每2年或行驶20万公里进行一次,对于校车等特殊车辆应缩短至每年检测。
当前,随着新能源客车轻量化设计的普及,复合材料与异型钢结构在固定点区域的应用日益增多,检测技术也逐步向数字化方向发展。例如采用光纤光栅传感器实时监测固定点应力变化,或通过有限元仿真预判潜在失效模式。这些创新方法正在推动行业安全标准迈向更高水平。
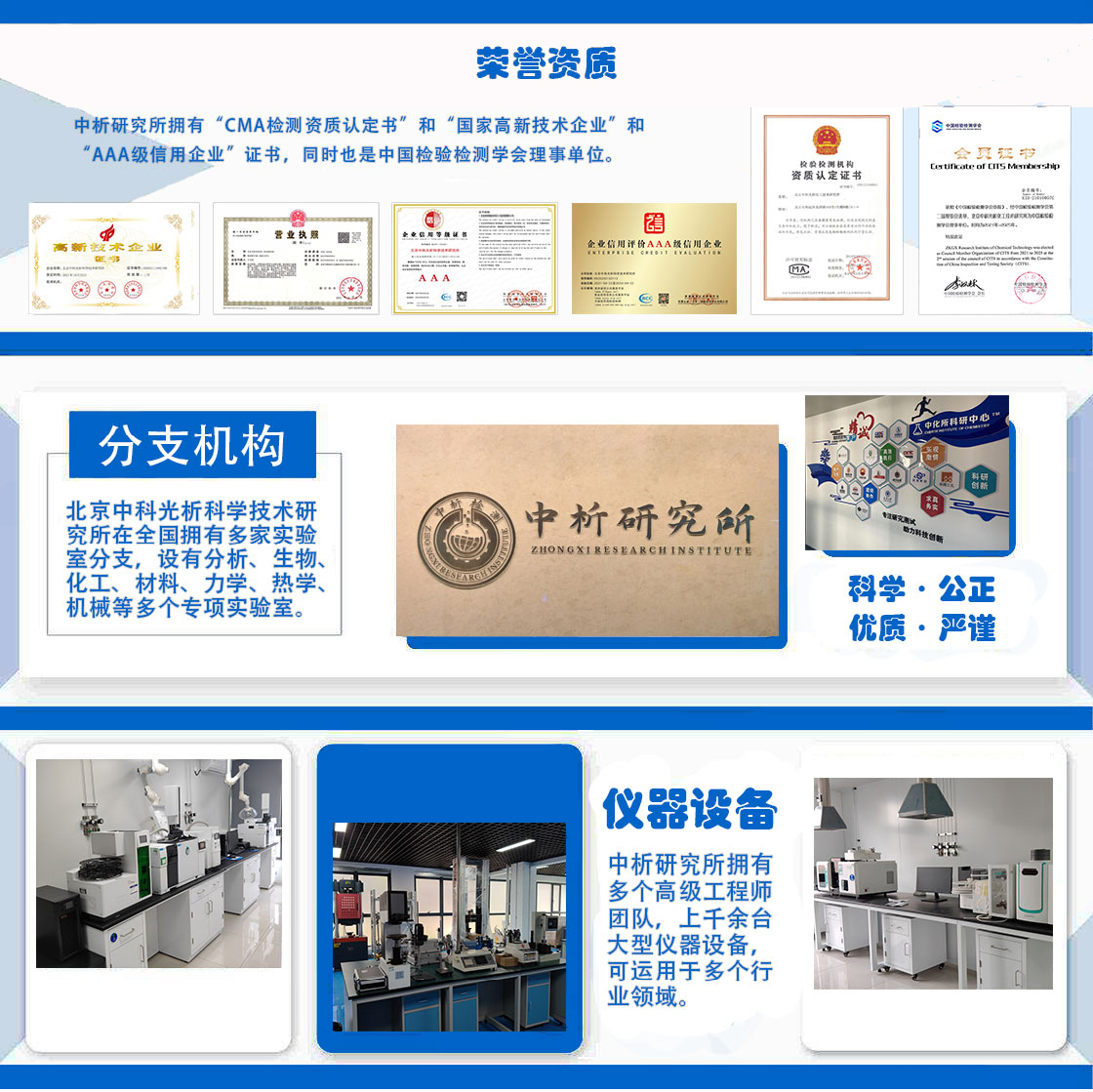
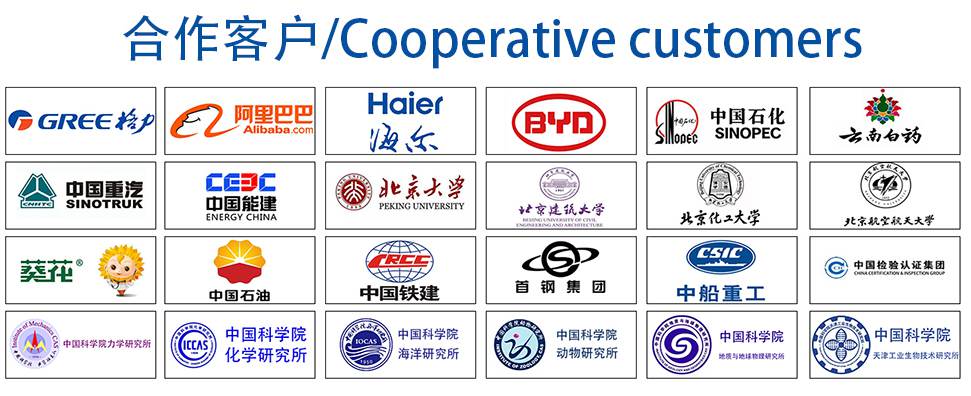