专用装备检测:保障工业安全与效能的基石
在工业生产、军事装备、特种设备等领域,专用装备作为核心技术载体,其性能与可靠性直接关系到作业安全与运营效率。随着装备智能化、精密化程度不断提升,检测工作已从传统的外观检查演变为涵盖材料性能、功能验证、环境适应性等20余项指标的综合性技术体系。通过系统化的专用装备检测,企业能够在设备全生命周期内实现故障预警、效能优化和风险规避,避免因设备失效导致的重大经济损失甚至安全事故。
核心检测项目体系解析
1. 结构完整性检测
采用X射线探伤、超声波检测等技术,对焊接部位、承重结构进行无损检测,确保装备在极限工况下的抗压抗扭能力。通过三维建模对比装配精度,公差控制可达0.01mm级,特别适用于航空航天精密部件检测。
2. 功能性能验证
搭建模拟工况测试平台,对液压系统压力稳定性、传动装置效率衰减率等动态参数进行72小时持续监测。军用特种车辆需额外通过40°坡道驻车、70km/h涉水等极端场景测试,数据采集频率高达5000次/秒。
3. 环境适应性检测
在气候模拟舱内进行-50℃~150℃温度冲击试验,配合盐雾、沙尘等复合环境测试,验证装备在极地、沙漠等特殊地域的可靠性。防爆类设备需通过EX认证,确保在甲烷浓度9.5%环境中持续安全运行。
智能化检测技术革新
基于工业物联网的预测性检测系统正逐步普及,通过装备内置的200+个传感器节点,可实时监测振动频谱、温度梯度等关键参数。大数据平台运用机器学习算法,提前14天预判齿轮箱磨损趋势,使维护成本降低37%。数字孪生技术实现虚拟与现实检测数据双向验证,检测效率提升4倍。
标准化认证体系构建
检测机构依据ISO 19443核工业标准、GJB 9001C军工标准等42项国际国内规范,建立分级认证制度。第三方检测报告需包含失效模式分析(FMEA)、平均故障间隔时间(MTBF)等核心指标,部分特种设备还需取得ATEX、API等行业准入认证。
当前专用装备检测市场规模已达680亿美元,检测技术的突破正在重塑装备制造业质量管控体系。企业通过建立PDCA检测循环机制,可将设备综合效率(OEE)提升至92%以上,为产业升级提供坚实的技术保障。
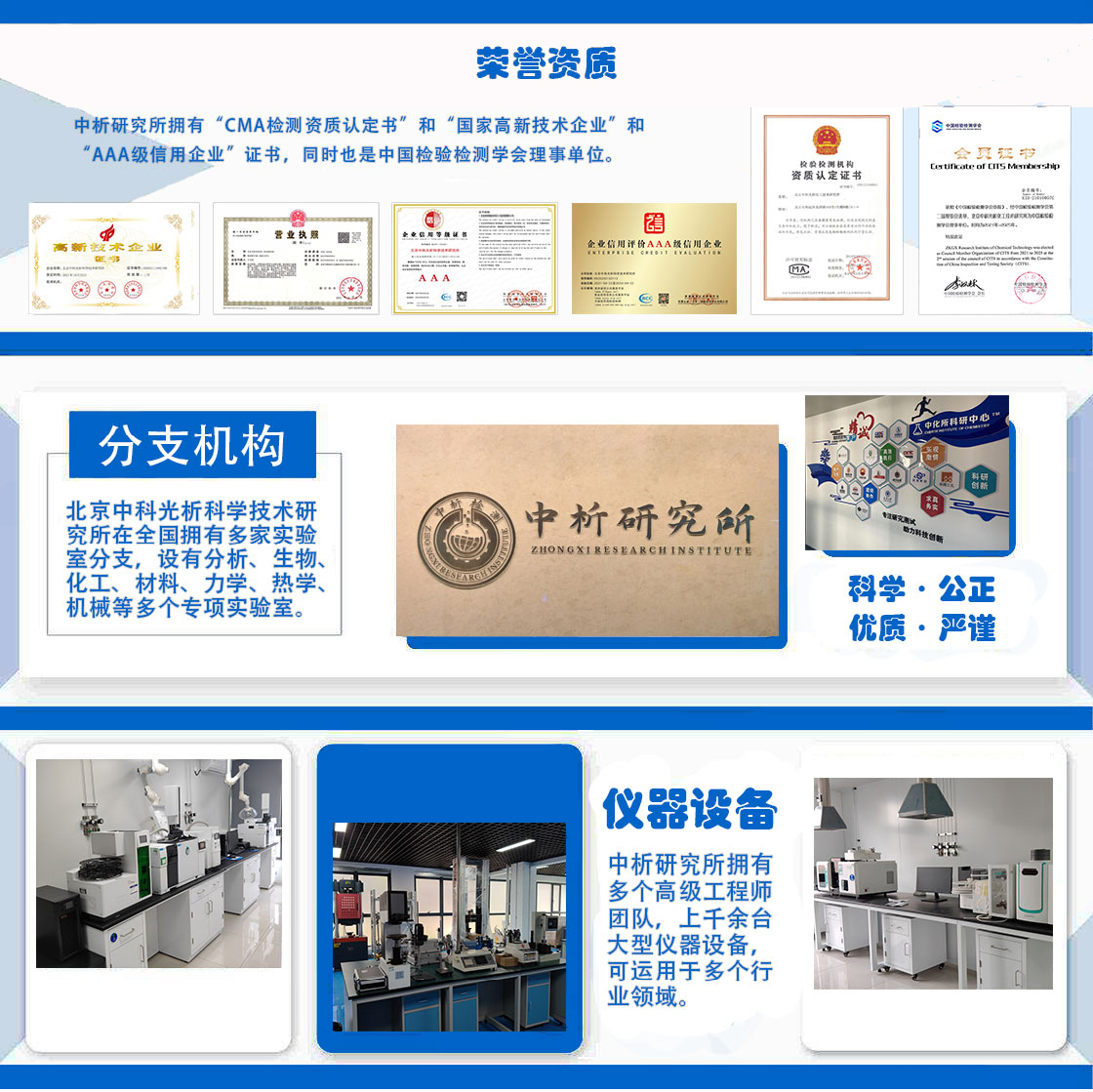
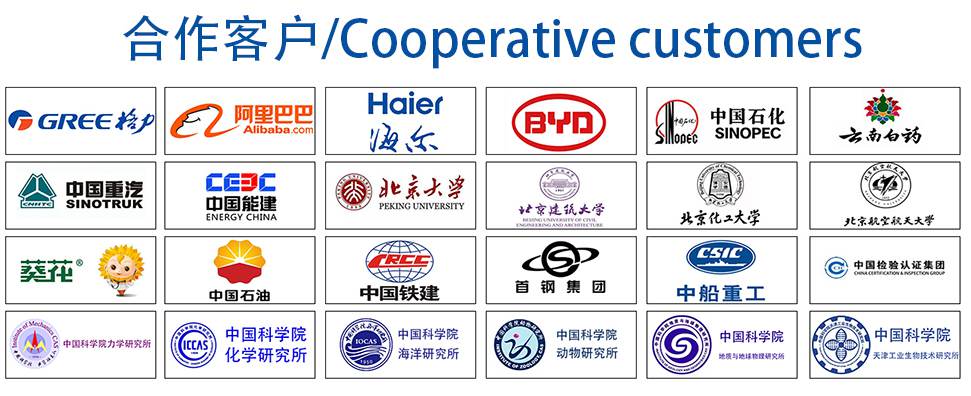