真空镀膜涂料检测的重要性与应用领域
真空镀膜涂料是一种通过物理气相沉积(PVD)或化学气相沉积(CVD)技术在基材表面形成功能性薄膜的材料,广泛应用于光学器件、电子产品、汽车零部件、装饰材料及工业防腐等领域。其性能直接影响涂层的附着力、耐腐蚀性、耐磨性及光学特性。为确保产品质量和工艺稳定性,对真空镀膜涂料进行科学、系统的检测至关重要。检测项目需覆盖物理性能、化学成分、环境适应性以及行业标准符合性,从而保障其在复杂应用场景下的可靠性和长期稳定性。
核心检测项目及方法
1. 物理性能检测
• 附着力测试:通过划格法(百格法)、拉拔试验或弯曲试验评估涂层与基材的结合强度,确保无起皮、剥落现象。 • 耐磨性测试:采用摩擦试验机模拟实际磨损条件,测定涂层的耐刮擦和抗磨耗能力。 • 厚度均匀性检测:利用扫描电镜(SEM)或X射线荧光光谱仪(XRF)分析涂层厚度的分布均匀性。
2. 化学成分分析
• 溶剂残留检测:通过气相色谱-质谱联用(GC-MS)测定涂料中有机溶剂的残留量,避免挥发物影响涂层质量。 • 重金属含量测试:符合RoHS、REACH等环保法规要求,确保涂料中铅、镉、汞等有害物质不超标。
3. 光学性能评估
• 透光率与反射率:使用紫外-可见分光光度计(UV-Vis)检测涂层在特定波长下的光学特性,适用于镜头、显示屏等光学器件。 • 色差与光泽度:通过色差仪和光泽度计验证涂层颜色一致性及表面光泽是否符合设计要求。
4. 环境适应性测试
• 耐腐蚀性测试:通过盐雾试验(如ASTM B117)模拟高湿、高盐环境,评估涂层的抗腐蚀能力。 • 耐高温/低温性能:将涂层样品置于高低温试验箱中,测试其在极端温度下的稳定性及是否发生龟裂、脱落。
检测流程与注意事项
检测流程通常包括取样→预处理→选择测试方法→数据分析→结果判定。需注意: 1. 样品制备需严格遵循标准(如ISO 2409),避免污染或损伤; 2. 检测设备需定期校准,确保数据准确性; 3. 结合应用场景选择针对性项目(如汽车部件需重点检测耐磨与耐候性)。
行业标准与法规要求
真空镀膜涂料检测需参考多项标准,包括但不限于: • ISO 2409(附着力测试); • ASTM D3363(铅笔硬度法); • GB/T 1771(盐雾试验)。 同时需符合欧盟CE认证、美国FDA等国际法规,确保产品市场准入。
结语
真空镀膜涂料的检测是保证其性能稳定性和市场竞争力的核心环节。通过多维度、多方法的科学检测,可有效控制涂层缺陷、优化生产工艺,并为后续研发提供数据支持。企业应选择具备 /CMA资质的专业实验室,确保检测结果的权威性与可靠性。
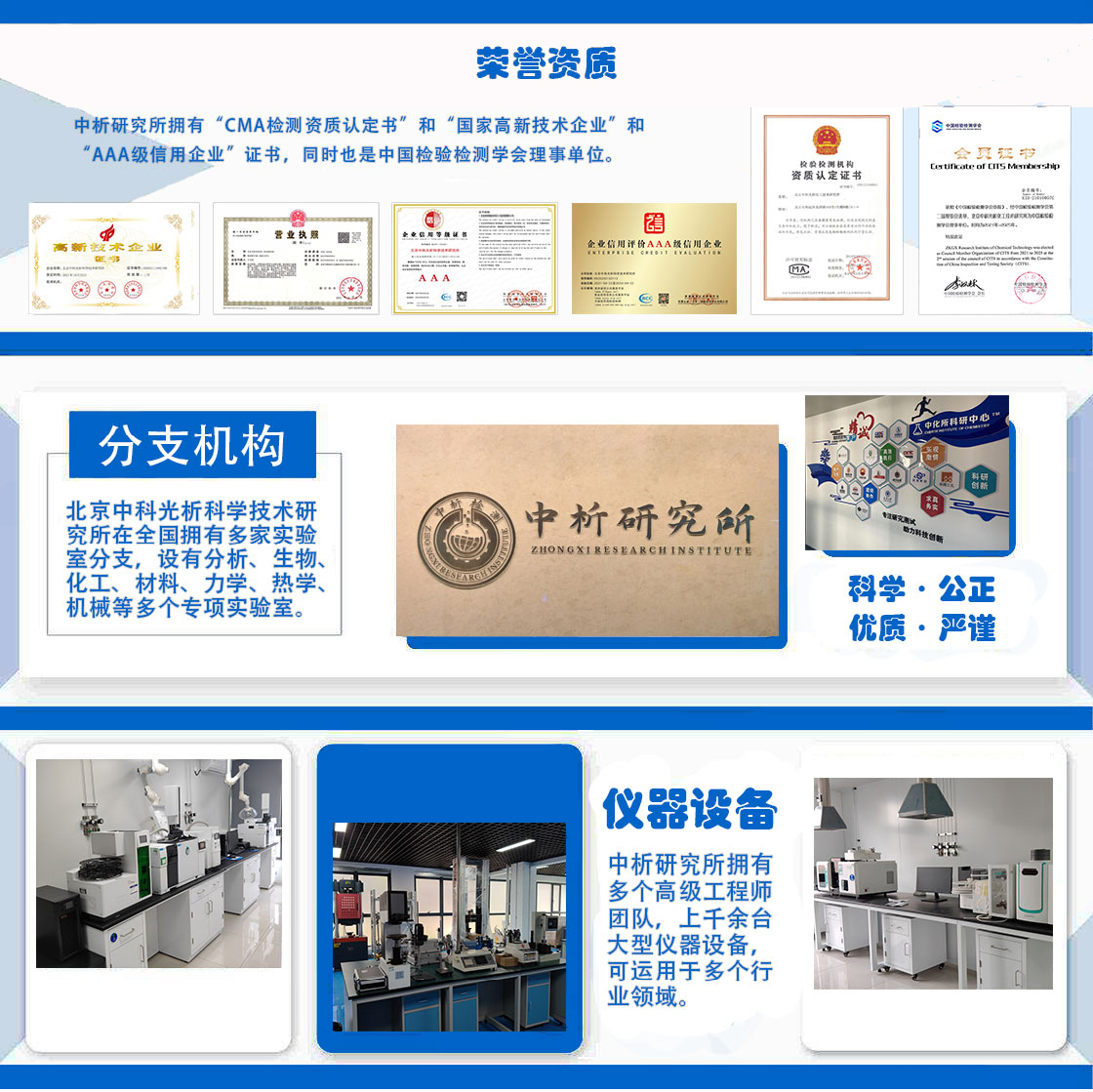
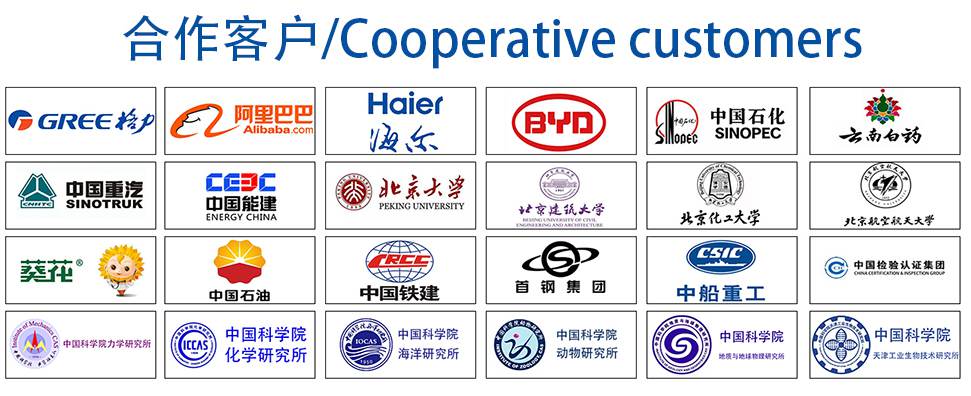