船舶压载舱漆检测的重要性
船舶压载舱作为维持船体平衡的关键结构,长期处于高湿度、盐雾和微生物侵蚀的复杂环境中。压载舱涂层不仅是防腐防锈的第一道防线,还直接影响船舶结构安全和运营寿命。由于舱内环境封闭且难以维护,涂层的完整性、附着力及耐腐蚀性能需要通过专业检测手段进行定期评估。国际海事组织(IMO)和各国船级社均对压载舱涂层的检测标准提出了严格要求,规范的检测流程能有效预防涂层失效导致的舱体腐蚀、渗漏等安全隐患。
核心检测项目及方法
1. 涂层附着力测试
采用划格法(ISO 2409)或拉开法(ASTM D4541)评估涂层与基材的结合强度,确保涂层在高压水冲洗或机械冲击下不发生剥离。检测时需根据涂层厚度选择不同间距的刀具,并通过显微镜观察切口边缘的脱落情况。
2. 干膜厚度测量
使用磁感应测厚仪(ISO 19840)或超声波测厚仪对涂层进行多点检测,验证干膜厚度是否符合设计规范(通常要求≥320μm)。特别注意焊缝、边缘等易腐蚀区域的厚度均匀性,允许偏差需控制在±20%以内。
3. 针孔缺陷检测
通过高压电火花检测仪(10-30kV)扫描涂层表面,识别微米级针孔缺陷。检测电压需根据涂层厚度调节,每发现1m²内超过3个针孔即判定为不合格区域。
4. 耐腐蚀性能试验
在实验室模拟环境下进行盐雾试验(ASTM B117)和循环腐蚀试验(ISO 11997-2),评估涂层在2000小时盐雾暴露后的起泡、锈蚀等级,要求达到ISO 4628标准中Ri0级(无可见缺陷)。
5. 表面清洁度检测
采用可溶性盐分测试(Bresle法)和表面粗糙度测量(ISO 8503),确保喷砂处理后的钢板表面盐分含量<20mg/m²,粗糙度介于40-75μm,为涂层提供最佳附着基础。
检测周期与标准依据
根据IMO PSPC标准要求,新建船舶需在涂装后3年内进行首次全面检测,后续每5年复检。检测过程需严格遵循ISO 15741、NACE SP0188等行业规范,所有检测数据应形成三维数字模型存档,便于寿命预测和维护决策。
结论
系统化的压载舱漆检测不仅能及时发现涂层老化问题,更能通过数据积累优化涂装工艺。随着智能检测机器人(AUV)和太赫兹成像技术的应用,船舶涂层检测正朝着数字化、无损化方向快速发展,为航运安全提供更强保障。
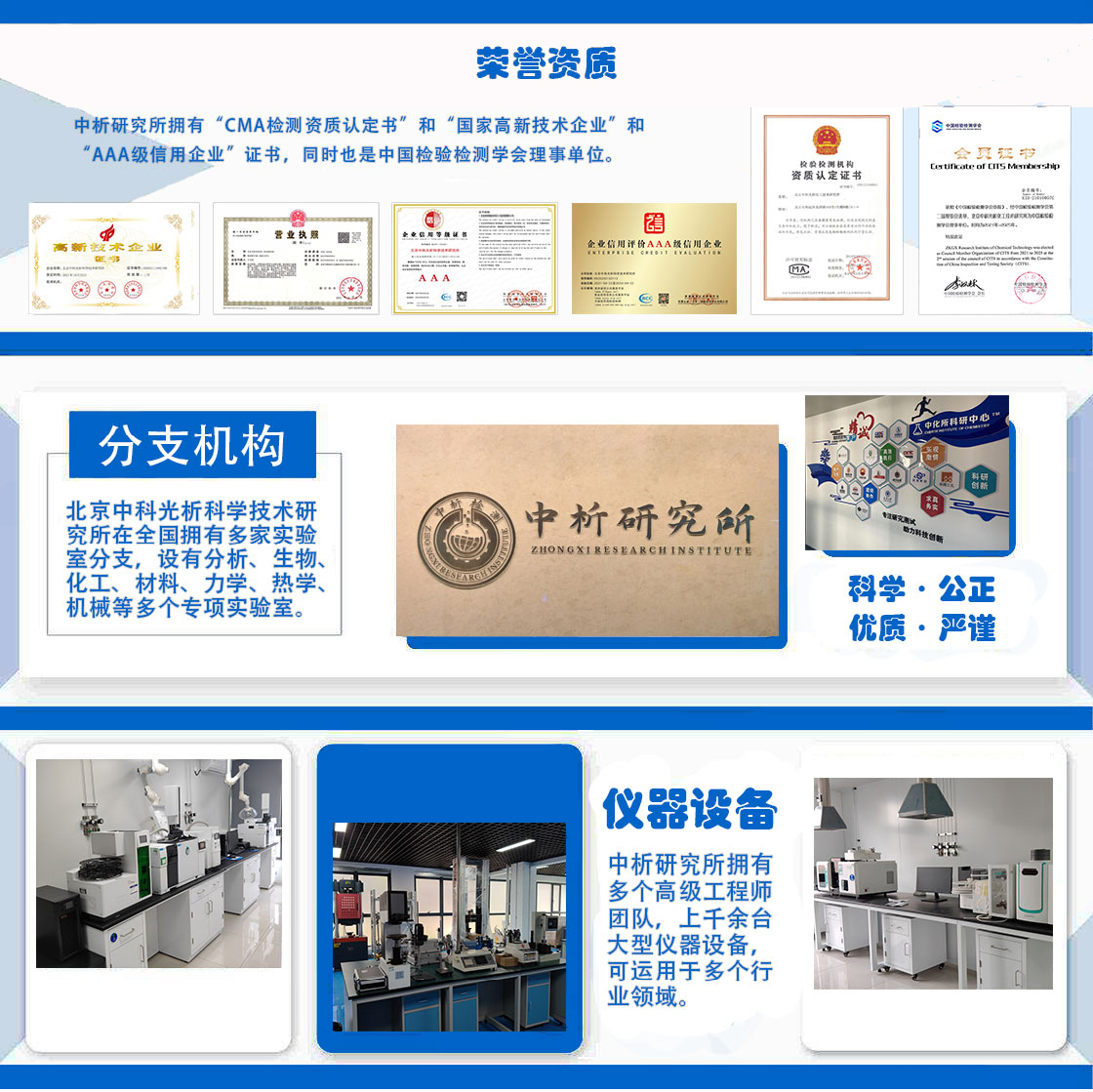
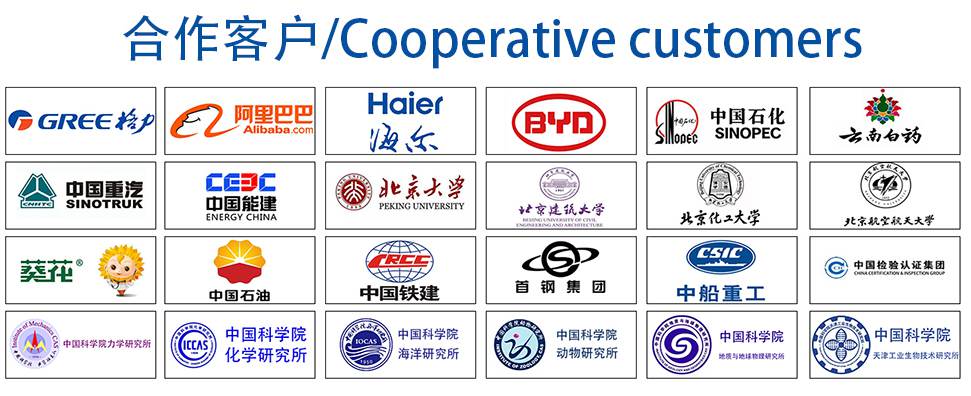