密封圈检测的重要性与行业应用
密封圈作为工业设备、汽车部件、航空航天等领域的关键元件,其性能直接影响系统的密封效果与安全性。在高压、高温、腐蚀性介质等复杂工况下,密封圈的失效可能导致设备泄漏、环境污染甚至安全事故。因此,通过系统化的密封圈检测项目,评估其物理性能、化学稳定性及耐久性,成为保障产品质量的核心环节。国际标准如ISO 3601、ASTM D2000等均对密封圈检测提出了明确要求,覆盖从原材料到成品全生命周期的质量验证。
密封圈检测的核心项目
1. 尺寸与几何精度检测
通过光学投影仪、三坐标测量仪(CMM)等设备,检测密封圈的内外径、截面厚度、圆度及表面平整度。重点验证是否符合设计公差(通常要求±0.1mm以内),确保与配合部件的装配适配性。
2. 材料性能测试
包括硬度(邵氏A/D)、拉伸强度、断裂伸长率等指标检测。例如:橡胶材料需满足ASTM D412标准,氟橡胶(FKM)的典型硬度范围在70-90 Shore A,拉伸强度需≥10MPa。同步开展热老化测试(如70℃×72h)评估材料稳定性。
3. 密封性能验证
采用气密性试验台或液压测试系统,模拟实际工况压力(可达50MPa)。记录泄漏量、形变恢复率等数据,例如汽车燃油系统密封圈需通过SAE J1203标准要求的1000次压力循环测试。
4. 耐介质与耐候性测试
将密封圈浸泡于燃油、润滑油、酸碱溶液等介质中(按ISO 1817标准),检测体积膨胀率(通常要求<15%)和质量变化。同时进行紫外线老化、臭氧暴露试验(ASTM D1149),评估抗龟裂性能。
5. 动态工况模拟检测
通过往复运动试验机模拟密封圈在活塞、旋转轴等场景下的长期磨损情况。记录摩擦系数变化,分析唇口磨损量(如要求500万次循环后磨损深度≤0.2mm),验证使用寿命。
检测技术的创新方向
随着工业4.0发展,密封圈检测正朝着智能化方向升级。例如:采用机器视觉自动识别表面缺陷,利用有限元分析(FEA)预测密封接触应力分布,以及基于AI算法的寿命预测模型。这些技术将进一步提升检测效率与精度,为高端装备制造提供更可靠的质量保障。
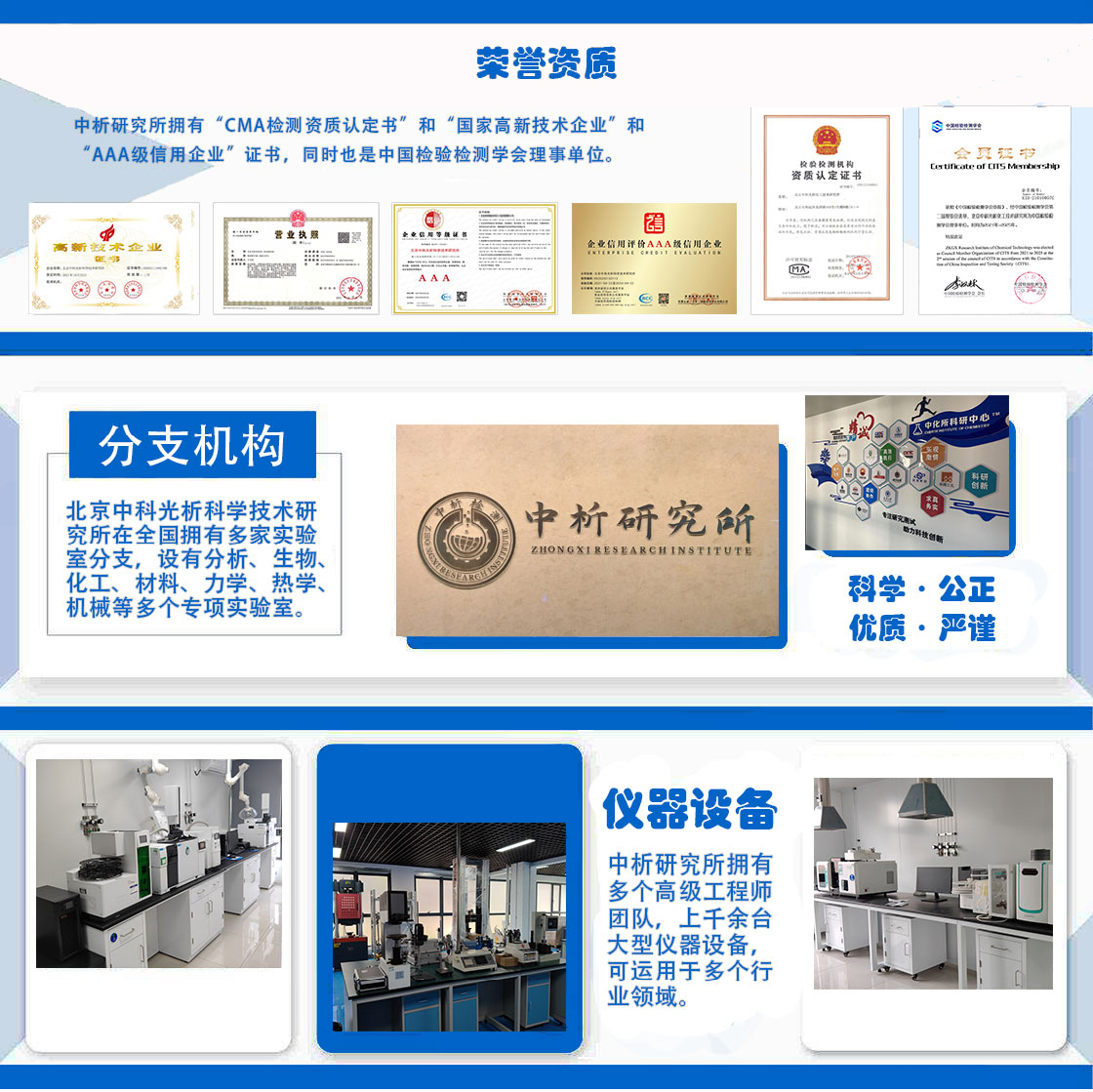
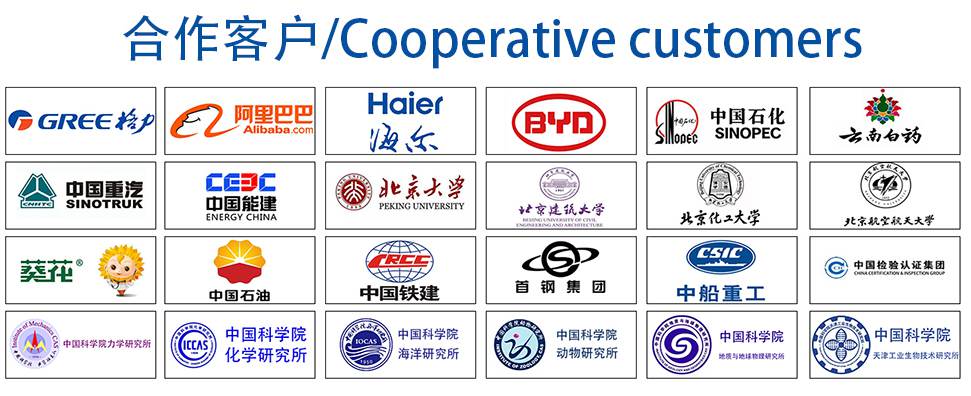