胶粘带作为广泛应用于包装、建筑、电子、汽车等领域的工业材料,其性能直接影响产品的密封性、固定效果及使用寿命。为确保胶粘带在实际应用中满足不同场景的需求,需要对其物理性能、化学稳定性和耐久性进行全面检测。胶粘带检测不仅是产品质量控制的关键环节,也是企业提升市场竞争力的重要手段。通过科学规范的检测项目,可以精准评估胶粘带的粘接强度、耐候性、抗老化能力等核心指标,从而避免因性能缺陷导致的失效问题。
1. 初粘性测试
初粘性是指胶粘带在极短时间内与被粘物表面接触时的初始粘接能力。该指标直接影响胶带的快速固定效果,常用斜面滚球法或环形初粘法进行测试。检测时需控制环境温度、湿度等条件,并依据GB/T 4852标准进行评定,确保胶带在低压力下仍能有效附着。
2. 持粘性测试
持粘性反映胶粘带在持续负载下的抗位移能力,通常通过悬挂标准砝码并记录胶带脱落时间来评估。测试需模拟实际应用场景的静载荷条件,例如高温或低温环境下的稳定性。ASTM D3654和GB/T 4851标准对此有详细规定,要求胶带在长时间受力后仍保持有效粘接。
3. 剥离强度测试
剥离强度用于衡量胶带从被粘物表面剥离时所需的力值,是评价粘接持久性的核心指标。测试方法包括180°剥离和90°剥离两种模式,需使用万能材料试验机记录最大剥离力。根据GB/T 2792和ASTM D3330标准,不同应用场景对剥离强度的要求差异显著,例如工业胶带需达到10 N/cm以上。
4. 厚度与均匀性检测
胶层厚度直接影响粘接性能和材料成本。通过高精度测厚仪对胶带进行多点测量,可评估其厚薄均匀性及胶层分布状态。检测时需关注局部厚度偏差是否超过±5%的行业允许范围,避免因厚度不均导致粘接失效或溢胶问题。
5. 耐温性与老化测试
模拟极端温度环境对胶粘带性能的影响,包括高温持粘试验(如80℃下保持48小时)和低温弯曲测试(-40℃冷冻后弯折无裂纹)。老化测试则通过紫外线加速老化箱或湿热试验箱评估胶带在长期使用后的性能衰减,确保其满足5年以上的使用寿命要求。
6. 耐介质腐蚀测试
针对特殊应用场景(如汽车油液环境),需测试胶带接触水、油、酸碱等介质后的粘接强度变化。将试样浸泡于指定化学试剂中72小时,取出后检测其剥离强度保留率。合格产品应保持80%以上的原始强度,且胶层无溶胀或脱落现象。
7. 拉伸强度与断裂伸长率
通过拉伸试验机测定胶粘带基材的机械性能,包括最大抗拉强度和断裂时的伸长率。该指标反映胶带在受拉应力下的抗变形能力,电子行业用胶带通常要求断裂伸长率≥200%,而重型包装胶带则更注重高拉伸强度(≥30 MPa)。
胶粘带的综合性能需要通过上述系统化检测项目进行验证。生产企业应结合产品应用领域选择对应的检测标准,并定期委托第三方检测机构进行质量复核,以确保产品符合国内外法规要求。规范的检测流程不仅能降低质量风险,还可为产品创新提供数据支撑,助力企业建立长期市场优势。
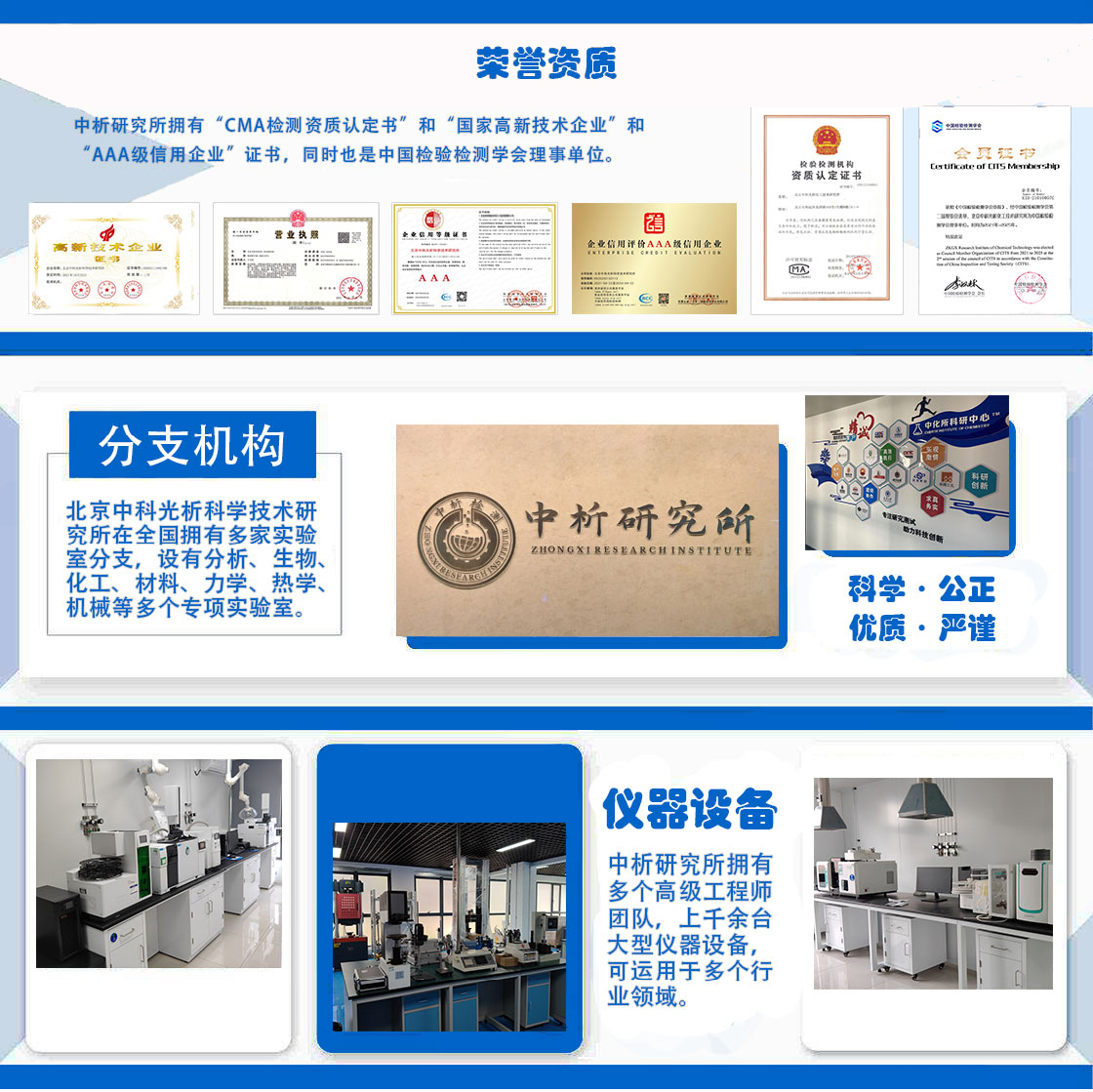
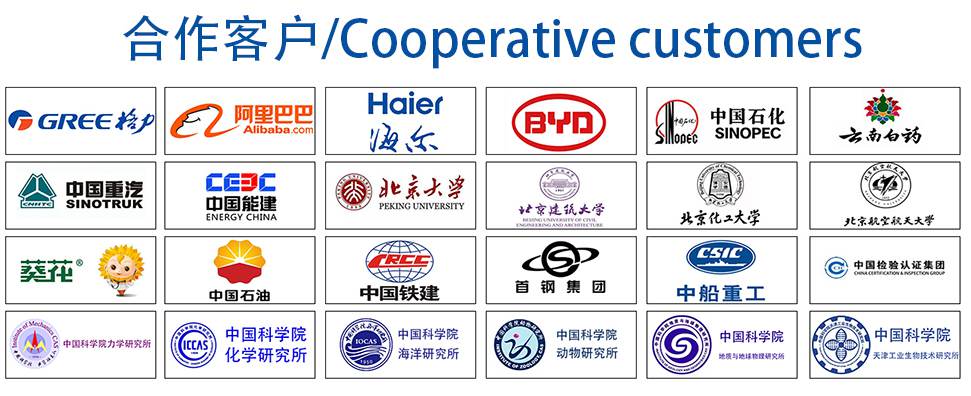