结构胶粘剂检测的重要性与核心内容
结构胶粘剂作为建筑、航空航天、汽车制造等领域的核心连接材料,其性能直接关系到工程的安全性和耐久性。随着现代工业对材料强度、耐候性及环保要求的提升,结构胶粘剂的检测成为保障工程质量的关键环节。检测项目不仅覆盖力学性能和化学稳定性,还需关注长期使用下的老化反应与环保指标。通过科学的检测手段,可有效避免因胶粘剂失效引发的结构隐患,同时为产品研发和质量控制提供数据支持。
核心检测项目分类
1. 力学性能检测
包括拉伸强度、剪切强度、剥离强度及压缩强度测试,评估胶粘剂在不同受力条件下的承载能力。需参照GB/T 7124、ASTM D1002等标准,通过万能试验机进行定量分析。
2. 耐久性检测
模拟实际环境中的老化条件,如湿热循环(ASTM D1183)、冻融循环(GB/T 50448)及紫外线加速老化(ISO 4892)。检测胶粘剂在长期暴露下的强度衰减和界面稳定性。
3. 化学性能分析
通过红外光谱(FTIR)和色谱法检测胶粘剂的成分纯度、固化程度及有害物质(如VOC)含量。重点监控游离甲醛、苯系物等污染物是否符合GB 18583等环保标准。
4. 相容性试验
评估胶粘剂与被粘材料(混凝土、金属、复合材料等)的界面结合效果,包括粘接面破坏模式分析(内聚破坏率≥90%为合格)及热膨胀系数匹配性测试。
5. 施工性能验证
检测胶粘剂的适用期、初粘力及固化速度,确保其满足现场操作需求。需结合触变性、流挂性等参数,优化施工工艺。
6. 环保与安全性检测
依据REACH、RoHS等法规,检测重金属、卤素等有害物质,并通过阻燃性(UL94等级)和毒性气体释放测试保障使用安全。
检测方法的选择与实施
检测需由CMA/ 认证实验室完成,结合破坏性试验与非破坏性检测(如超声波探伤),并根据应用场景选择加速老化或自然暴露试验。检测报告应明确数据偏差范围,为工程验收提供法律依据。
通过系统化的检测流程,不仅能筛选出符合标准的结构胶粘剂,还可推动行业向高性能、低环境负荷的方向发展。企业应建立定期复检机制,确保材料在全生命周期中持续满足设计要求。
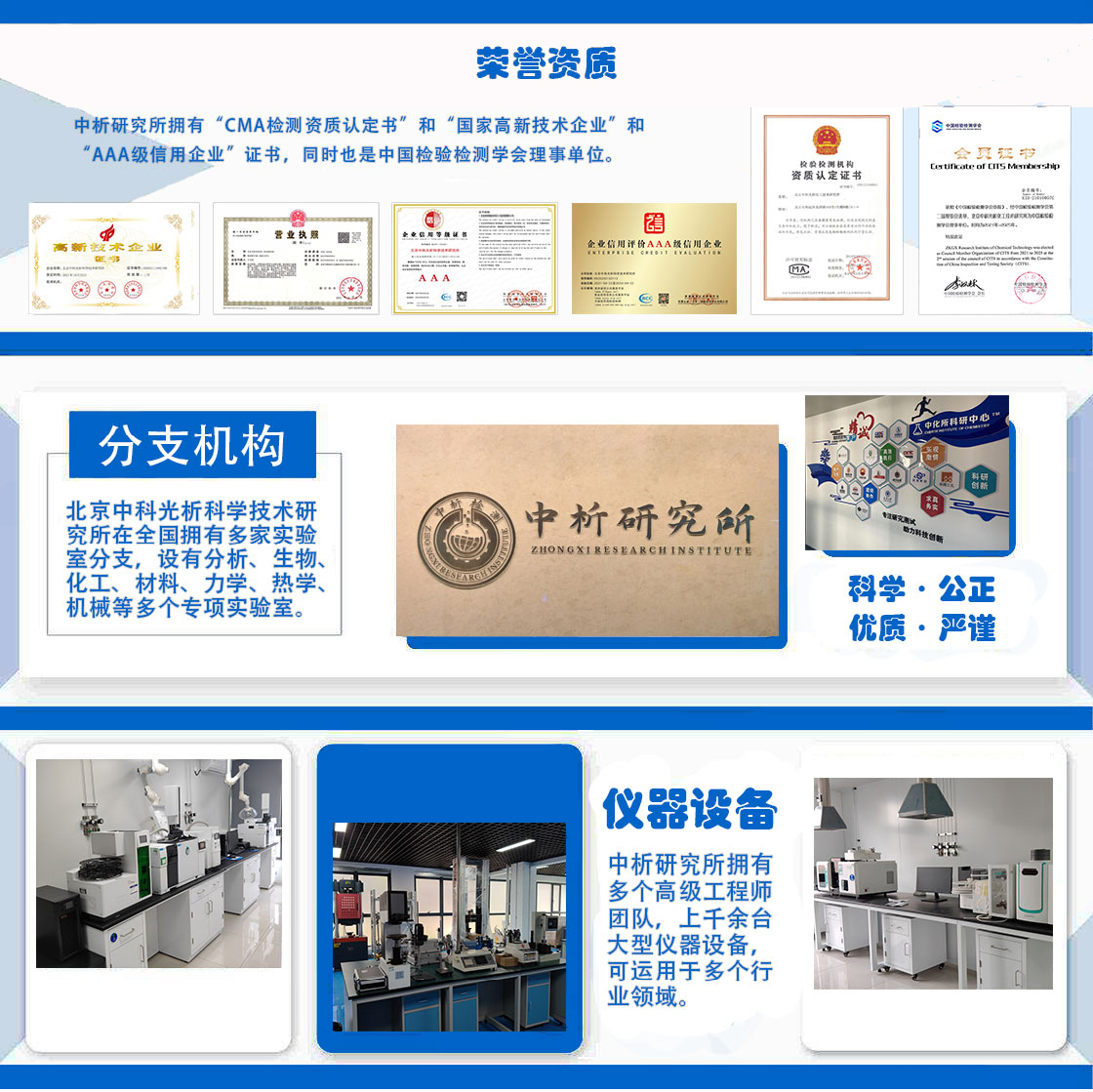
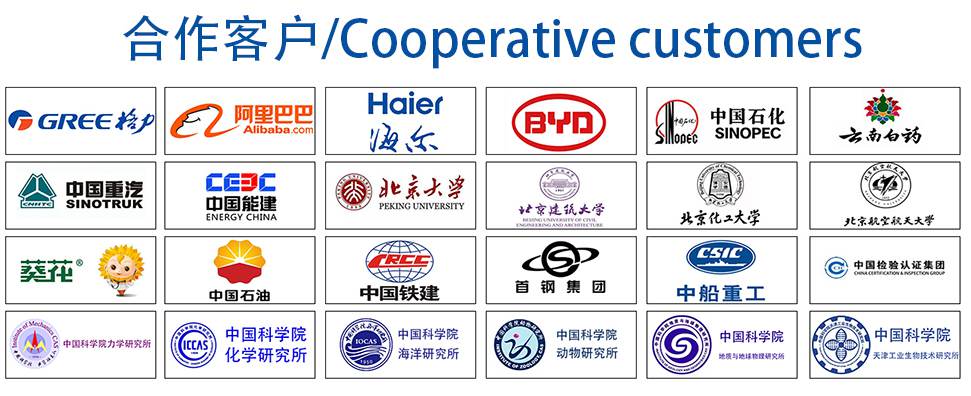